Questions to ask yourself during a pipeline install coating inspection
May 27, 2020 •Corrosion CONTROLLED, Corrosion Essentials, M&I
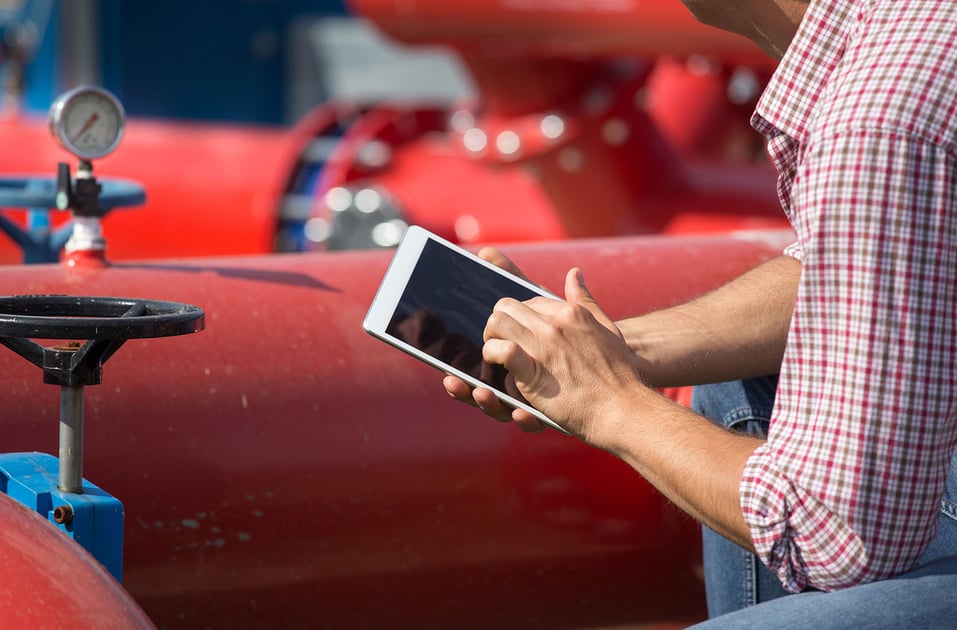
For pipeline coating inspectors, every day on the job is different; every case is unique in some way; and many parameters can be behind the reason for the inspection. As a result, learning follows you wherever you go and with it, a series of questions you should be asking yourself to help you do your best inspection work.
What is my role as a pipeline coatings inspector?
Financial loss or even a meltdown is an unpleasant condition for any pipeline construction company or asset owner. A pipeline coating inspector is responsible for saving money, providing the right standards for coating, and ensuring the consistency of quality in the pipeline industry. Therefore, a third-party coating inspector is the hidden backbone of pipeline construction companies and asset owners. Performing the inspection correctly and with diligence at initial installation is essential and your role, important.
Do I know what to inspect and how to inspect pipeline coatings?
There are two kinds of third-party inspectors for pipeline coatings: pipeline coating inspectors and cathodic protection inspectors. If one of these inspectors is missing, sadly the job won’t be completed. The job involves detail-oriented teamwork between the two types of inspectors in the following ways:
Specs and Definition - Imagine how great it would be if the correct specifications and a full understanding of the job were always in place and followed. Jobs would take half the time! This is why it is so important to meet all the demands of the specification documents given by the contractor companies and/or asset owners.
Visual and Sensor Detection - Being a good observer makes the field day much easier. For example, always keep in mind how to block water and oxygen on both the pipelines and weld joints. Corrosion control of external pipelines is always applied in the field thus, the golden rule of corrosion prevention on pipelines is “No oxygen, no cry!” This precaution helps one develop a keen eye for visual detection, which improves with every inspection. Whether it’s rust, a run or sag, improper paint color, dry spray, poorly feathered edges, a missing stripe coat, a wrong wrapping technique or material, joint position, root spacing, or dirt — “if it’s visible, it counts.” Additionally, sometimes it is helpful to see the failure via excessive film build, holidays, or mechanical damage.
If something is missed visually, rely on inspection equipment. Painting is not a fully robotic job and, mistakes can happen. Correcting mistakes on time and based on the standards can be a detail-oriented and collaborative job, however. Therefore, it’s important to look around at the surroundings and collect additional data for inspection. Climate, soil quality, and other underground structures may come into play. Smell the soil and air; if there is leakage, especially in oil pipelines or sewer pipelines, odor is a good indicator that will make decisions easier. If lucky, you will smell the sulfur, which is released as a product of microbial corrosion.
Field Tools and Coating Standards - Using the proper certified and calibrated equipment in the field makes inspection more comfortable. Many simple but technological tools can be used. Must-have tools include a dry film thickness gage, wet film thickness gage, magnifier, painting mirror, depth gage, replica tapes, holiday detectors, thermometer, hygrometer, and adhesion testers. Convenient to carry in the field, these are all small, pocket-sized instruments that fit into a small toolbox. Today, smartphones can be used as a flashlight, map, and camera, making them good companions to your tool kit. Also, make sure to have a copy of NACE International and Society for Protective Coatings (SSPC) standards with you anytime you’re in the field.
Hopping for Holidays - The technical term “holiday” represents voids or pinholes in coating. Hopping, also known as “jeeping for holidays” means using high-voltage holiday detectors in certain points to detect the holidays. Electrical current catches even the tiniest flaws.
Surface Preparation, Material Selection, and Coating Applications - Surface preparation, material selection, coating application, and cannot be separated from the inspection job. Keep in mind the importance of the whole process while performing an inspection.
Am I knowledgeable of new materials, coating techniques, and policies?
Previous coating materials, which were used for many years until the late 1980s and early 1990s, were coal tar and asphalt. This old trend is still used at times, but for the most part, there has been a smooth transition into non-metallic pipeline coating materials (plastics have a big role in coating). These are known as anti-corrosion coating materials. Classifying non-metallic external pipeline coatings with respect to application location can serve as an example: liquid epoxy, coal tar epoxy, and liquid polyurethane are applied in the field on the joints and the pipeline itself. Occasionally, fusion-bonded epoxy (FBE/mill-applied pipeline coating) is applied to the joints. For reasons of safety, timeliness, and cost, FBE is not recommended. However, even liquid polyurethane is sometimes chosen as a joint coating — the most labor- and time-intensive joint coating in the field.
The U.S. Environmental Protection Agency (EPA) has gradually improved policies regarding anti-corrosion coatings. According to the EPA, the most notable features of coating materials are: “safe for humans during application, environmentally friendly, capable of isolating the substrate (to protect it from oxidation), chemical resistance, and durability.” In terms of reducing mechanical damage through installation and coating, the material is required to be resistant to such damage. In addition to being chemically resistant, some physically resistant requirements are critical such as cathodic disbondment, bendability and application in a large range of process temperatures. Newer coating technologies can provide safe, functional, fast, and optimized labor and material costs in pipeline coating systems, however, note that all features of newer coatings must match the applicable standards.
Do I know my responsibilities and qualifications?
The field job requires some personal safety responsibilities, which in the United States are enforced by the EPA. Personal protective equipment (PPE) safeguards inspectors from hazards, such as toxic vapors, corrosive substances, fire and electrical hazards, and physical hazards such as falls. Choosing the appropriate PPE will vary depending on the type of job.
Repairs down the road repairs may be necessary with the aging of the substrate and coating, but if the inspection was performed correctly and thoroughly during initial installation their number should be far fewer.
Want a career as a coating inspector? The NACE Institute’s Coating Inspector Certification Program is recognized and specified worldwide. Start your career with the educational courses that prepare you for this certification in NACE's Coating Inspector Program.
Source: “The Hidden Backbone: Field Pipeline Coating Inspectors,” by Deniz G. Illeez, Principal of AGEZ Corrosion/Engineering Consulting and Inspection Services. Originally appearing in CoatingsPro Magazine, May 2020.
FREE DOWNLOADS
White Paper: An Action Plan for Reducing Pipeline Failures, Costs with Corrosion in the Water Sector
Special Report: The Future of Corrosion Control, Insights from the Experts
Get Updates
Featured Articles
Categories
- 2024 Olympics (1)
- 2024 Water Resource Development Act (1)
- Abrasive Blasting (1)
- Advanced coating materials (9)
- advanced coatings (1)
- Advanced Corrosion Control in Oil and Gas Industry (2)
- Advocacy (3)
- AI (2)
- Aircraft (1)
- Alkanization (1)
- AMPP (4)
- AMPP Annual Conference + Expo (5)
- ampp awards (1)
- ampp certification (2)
- Ampp Chapters (1)
- AMPP conference (1)
- AMPP logo (1)
- Ampp Membership (2)
- Ampp Standards (2)
- ampp training (2)
- Amusement parks (4)
- Architectural (1)
- Architectural Coatings (2)
- argonne national laboratory (1)
- Artificial Intelligence (1)
- Asset integrity (12)
- Asset maintenance (3)
- Asset Protection (1)
- awards (3)
- B2B Marketing (1)
- Bim Software (1)
- Biodeterioration of materials (5)
- Biofouling (4)
- Blasting (1)
- Bridges (4)
- career advancement (3)
- career development (2)
- cathodic protection (2)
- Cathodic Protection-CP (16)
- Ceramic epoxies (1)
- Certification (3)
- certification study guide (1)
- Chemical Injection (1)
- CIP (1)
- Civil Engineering (1)
- clean energy (1)
- Coating inspector (2)
- coating inspector job roles (1)
- Coating inspector jobs (2)
- Coating inspector program (2)
- Coatings (18)
- Coatings Application (3)
- coatings certification (1)
- Coatings failures (2)
- Coatings Industry (2)
- coatings inspection (1)
- Coatings inspector (2)
- Coatings measurement and inspection (9)
- coatings project management (1)
- Coatings Systems (1)
- Cold stress (1)
- Concrete (13)
- Concrete corrosion (1)
- concrete cracking (1)
- Conference and Events (2)
- Corrosion (26)
- Corrosion Basics (5)
- corrosion certification (1)
- Corrosion Control (17)
- Corrosion Control and Management (23)
- Corrosion detection (1)
- corrosion engineering (1)
- Corrosion Essentials (20)
- Corrosion Inspection (1)
- Corrosion Management (1)
- corrosion mitigation (1)
- corrosion of steel (1)
- corrosion policy (1)
- Corrosion Prevention (12)
- corrosion resistance (1)
- corrosion resources (1)
- Corrosion Under Insulation (2)
- cost of corrosion (1)
- Crevice Corrosion (1)
- Cui (2)
- Data Monitoring (1)
- decarbonization (1)
- defense infrastructure (1)
- Department of Defense (4)
- Deposition corrosion (1)
- Dissimilar Metal Corrosion (1)
- Dissolved gases (1)
- DoD (3)
- Education (2)
- EMERG (1)
- Energy industry (9)
- entertainment industry (1)
- Epoxy (3)
- exam preparation (1)
- FBE Application (1)
- FBE Inspection (1)
- Fireproofing (1)
- Flexible coatings (2)
- Flint, Michigan (1)
- Fluoropolymer coating (3)
- Forms of Corrosion (4)
- Freshwater salinization (1)
- Fusion-bonded epoxy (1)
- Galvanic (1)
- Galvanic Corrosion (4)
- General Corrosion (4)
- General Tips (1)
- glossary (1)
- Hand tools (1)
- honoree night (1)
- Industrial Application (3)
- Industrial Safety (3)
- Industry Best Practices (1)
- Industry Standards (2)
- Infrared Thermography (1)
- infrastructure (4)
- Infrastructure Durability (1)
- Inspection (1)
- integrity management (1)
- Intergranular Corrosion (1)
- Intumescent Coatings (1)
- key note speaker (1)
- leader (1)
- Machine Learning (2)
- Maintenance (2)
- Maintenance Best Practices (1)
- Maritime Coatings (11)
- Maritime industry (11)
- Master Painters Institute (2)
- material protection (1)
- materials performance (1)
- materials science (1)
- Membership (2)
- Membership Benefits (2)
- Michio Kaku (1)
- Microbiological forms (1)
- Microbiologically influenced corrosion-MIC (11)
- Military (2)
- Mineral constituents (1)
- MnDOT (1)
- MPI (3)
- mpi awards (1)
- mpi champion awards (1)
- mpi training (1)
- MPI Update (1)
- National Defense Authorization Act (1)
- national security (1)
- Navy (1)
- nickel-based alloys (1)
- Non-Destructive Testing (1)
- nuclear (1)
- nuclear Materials (1)
- nuclear reactor technology (1)
- Oil and Gas (2)
- Oil Fields (1)
- Organic matter (1)
- Oxgen (1)
- Paint and Protective coatings (32)
- Paint specification (1)
- pcs certification (1)
- Personal Protective Equipment (3)
- Petrochemical Plant Fireproofing Methods (1)
- Petrochemical Plants (1)
- Pipeline (2)
- Pitting Corrosion (2)
- Pitting Detection (1)
- Polymer-Based Coatings (1)
- Power plant (1)
- Power tools (1)
- PPE (3)
- Print Advertising (1)
- Print Marketing Strategy (1)
- professional certification (2)
- professional development (1)
- Protective Coatings (7)
- protective coatings industry (1)
- protective coatings specialist (1)
- quality assurance (1)
- radiation-resistant materials (1)
- Real-Time Corrosion Monitoring in Oil Fields (1)
- Rebar Corrosion (2)
- rectifier (1)
- Reliability (1)
- Remote monitoring and drones (4)
- Repaint (1)
- Restoration (1)
- ride maintenance (1)
- Risk-Based Inspection (1)
- Road deicers (1)
- Roads and bridges (1)
- Roller coaster (1)
- Rust (1)
- sacrificial anodes (1)
- Safety (5)
- Safety Standards (3)
- Salt pollution (1)
- Sensors (1)
- service awards (2)
- Ship Coatings (9)
- Shiptanks (1)
- Standards (10)
- Standards Committees (2)
- Steel (8)
- Steel Reinforcement (2)
- Stress Corrosion Cracking (1)
- Structural Steel (1)
- study tips (1)
- Surface Preparation (13)
- Sustainability (1)
- Sustainability and corrosion (7)
- terminology (1)
- Tools (1)
- Turbine (1)
- Types of Corrosion (1)
- Ultrasonic Testing (1)
- Uniform Corrosion (1)
- us army core of engineers (1)
- Wastewater Systems (1)
- Water crisis (1)
- Water pipe corrosion (1)
- Water quality (1)
- Water tank coatings (5)
- Water/treatment infrastructure (20)
- Waterway salinity (1)
- Workforce development (1)
- WRDA (1)