Cathodic Protection Advancement Reduces Travel to Remote Locations
June 29, 2021 •Corrosion CONTROLLED, Corrosion Essentials, CP
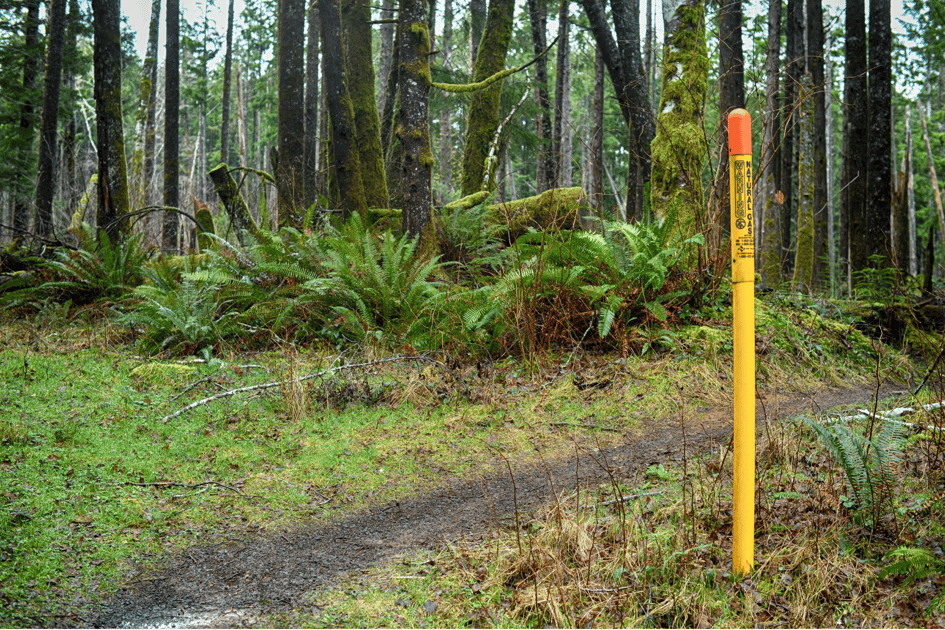
Utilities and pipeline operators can now remotely perform interruption, obtain CP measurement data, and dramatically reduce travel to remote locations with MOBILTEX’s CorTalk RMU1+INT1 package. In a recent Materials Performance podcast interview, Tony da Costa, vice president of engineering at the company discusses how technology is a game changer for this industry and how it has helped advance remote cathodic protection (CP) monitoring.
The amount of technology going into pipelines today is incredible. Previously, we saw people doing manual, tedious work to maintain these pipelines, and now it is possible to sit in your office and attain that same level of visibility into that asset without having to leave and, you get a much better data set on how those assets are operating.
The CorTalk RMU1 with INT1 interruption peripheral, represents the cathodic protection’s industry’s first permanently installed, battery-powered remote monitoring device that enables GPS-synchronized interruption for critical bonds and sacrificial anodes. The RMU1, which is the controller for the whole system, adds 2-way communications, enabling it to receive commands and to control that new INT1 peripheral device for the synchronization of the interruption waveform.
Having received a 2021 Materials Performance Corrosion Innovation Awards, the monitoring device eliminates the need for technicians to install portable interrupters to break bonds or interrupt sacrificial anodes during annual or indirect survey activities. The product can be installed within minutes inside a standard 3-inch test station. That allows fuel technicians to greatly expand the remote monitoring and interruption programs to improve operating efficiency, accuracy of measurements, achieve compliance, and ultimately improve the safety of fuel personnel in the public.
Necessity – The Mother of Cathodic Protection Innovation
Two of our customers approached us for a solution to the problem of being able to interrupt bonds and galvanic anodes using a permanently installed remote monitoring unit. They were seeing inefficiencies in their surveyed jobs as well as data that wasn’t always reflective of protection levels throughout the year. Our experience with designing low-power, battery-operated remote monitoring units gave us the ability to turn those requests into the RMU1 with the INT1. With that product, customers are now able to interrupt their bonds and galvanic anodes right from the comfort of their office while getting rich data throughout the year on their asset protection levels.
Normally, pipelines are protected against electrochemical corrosion by coatings applied to the outside of pipes. However, inevitable defects in the coating allow contact between the metal and the pipe and the surrounding environment, which leads to rusting of the pipe at the coating defect location. This rusting eventually leads to perforation of the pipe and, along with that, leaks of the product carried by the pipeline. Instead of fixing coatings, which would be difficult to accomplish on buried pipe, impressed current rectifiers and sacrificial galvanic anodes are installed to polarize that pipeline, which prevents the normal chemical reaction that causes rust at the defect locations. The two systems collectively are known as cathodic protection. There are test stations at locations, typically space in increments of 1 mile or less, where then a variety of readings can be taken on that pipe.
To validate the operation of the rectifiers and sacrificial anodes and their effectiveness in preventing corrosion, measurements are made of critical parameters along the pipeline at test stations during annual surveys and close-interval surveys. These measurements are compared against standard protection criteria values to gage proper operation of the rectifier and galvanic anode systems. Some of those measurements require that all sources of protection current be removed while the measurements are made. These measurements are known as instant-off potentials. Those protection current sources must be reconnected after the measurement is made so as to maintain that protection level. This removal and restoration of protection current sources is known as “interruption.”
The availability of AC line power at rectifiers made it simple to create remote monitoring units that have become ubiquitous for gathering measurements but also enabling the interruption of those rectifiers. Unfortunately, rectifiers aren’t the only sources of instant-off potential errors on the pipeline. Bonds and sacrificial anodes are a different matter in terms of remote monitoring and control. Fortunately, at bonds and galvanic anode installation sites, AC line power is not usually available. With that, bonds and galvanic anodes rarely had remote monitoring with interruption capability, as this would typically require a remote monitoring unit that was battery powered with solar panels that are expensive and always a target for theft and vandalism.
This dictated that either portable interrupters were deployed to bond and galvanic anodes during surveys, or they were simply disconnected. Disconnecting completely creates time periods where protection is not being applied to the pipeline segments at those locations. Also, survey crews need to remember to go back and reconnect all the disconnected equipment after survey completion.
Interface, Platform, Access and What’s Next for Remote CP Monitoring
The backbone of a strong IoT (Internet of Things) system is always how the device transmits out data and how that data is stored, accessed, and visualized. Our remote monitoring units leverage cellular and satellite networks to provide connectivity from the field device to the cloud. With access to RMU and CP asset data, our CorView software platform allows operators to use those communications technologies in a flexible manner, choosing whichever technology is best suited for that location. The transmitted measurement data, whether it be potentials, currents, pressures, or any other parameter being samples by the remote monitors, is stored and organized in CorView. That’s our data repository and web portal, which allows users to access the data and enables users to schedule those survey interruption events I described before.
It’s an intuitive platform that tailors well to the unique needs of various user profiles -- from fuel technicians, CP supervisors, and engineers, to integrity managers even. The platform is also available in app form, which complements well with our line of configuration apps used for each of our products. Essentially, anywhere that an internet connection is present, access to the data and control functionality is available to the users. With the next release of CorView, we aim to give our users the ability to interface with the data on the platform in a flexible manner by offering new application programming interfaces.
Also, as part of that release, we will start introducing analytics capabilities directly into the platform. The area of analytics has been traditionally an area where data has been kept in disparate databases, filed away, and not really put to its full potential. Now, the ability to take all those disparate sets and come up with meaningful predictions.
The NACE Institute administers 23 certifications on a variety of disciplines including the most specified and recognized NACE Institute Cathodic Protection (CP) Certification.
Source: Materials Performance Podcast, part of the AMPP Interview Series, transcript excerpts.
FREE DOWNLOADS
White Paper: An Action Plan for Reducing Pipeline Failures, Costs with Corrosion in the Water Sector
Special Report: The Future of Corrosion Control, Insights from the Experts
Get Updates
Featured Articles
Categories
- 2024 Olympics (1)
- 2024 Water Resource Development Act (1)
- Abrasive Blasting (1)
- Advanced coating materials (9)
- advanced coatings (1)
- Advanced Corrosion Control in Oil and Gas Industry (2)
- Advocacy (3)
- AI (2)
- Aircraft (1)
- Alkanization (1)
- AMPP (4)
- AMPP Annual Conference + Expo (4)
- ampp awards (1)
- ampp certification (2)
- Ampp Chapters (1)
- AMPP conference (1)
- AMPP logo (1)
- Ampp Membership (1)
- Ampp Standards (1)
- ampp training (1)
- Amusement parks (4)
- Architectural (1)
- Architectural Coatings (2)
- argonne national laboratory (1)
- Artificial Intelligence (1)
- Asset integrity (11)
- Asset maintenance (3)
- Asset Protection (1)
- awards (2)
- Bim Software (1)
- Biodeterioration of materials (5)
- Biofouling (4)
- Blasting (1)
- Bridges (4)
- career advancement (2)
- career development (2)
- cathodic protection (2)
- Cathodic Protection-CP (16)
- Ceramic epoxies (1)
- Certification (3)
- certification study guide (1)
- Chemical Injection (1)
- CIP (1)
- Civil Engineering (1)
- clean energy (1)
- Coating inspector (2)
- coating inspector job roles (1)
- Coating inspector jobs (2)
- Coating inspector program (2)
- Coatings (16)
- Coatings Application (3)
- coatings certification (1)
- Coatings failures (2)
- Coatings Industry (2)
- coatings inspection (1)
- Coatings inspector (2)
- Coatings measurement and inspection (9)
- coatings project management (1)
- Coatings Systems (1)
- Cold stress (1)
- Concrete (13)
- Concrete corrosion (1)
- concrete cracking (1)
- Conference and Events (2)
- Corrosion (21)
- Corrosion Basics (5)
- corrosion certification (1)
- Corrosion Control (16)
- Corrosion Control and Management (23)
- corrosion engineering (1)
- Corrosion Essentials (20)
- corrosion mitigation (1)
- corrosion of steel (1)
- corrosion policy (1)
- Corrosion Prevention (10)
- corrosion resistance (1)
- corrosion resources (1)
- Corrosion Under Insulation (1)
- cost of corrosion (1)
- Crevice Corrosion (1)
- Cui (1)
- Data Monitoring (1)
- decarbonization (1)
- defense infrastructure (1)
- Department of Defense (4)
- Deposition corrosion (1)
- Dissimilar Metal Corrosion (1)
- Dissolved gases (1)
- DoD (3)
- Education (2)
- Energy industry (9)
- entertainment industry (1)
- Epoxy (2)
- exam preparation (1)
- Fireproofing (1)
- Flexible coatings (2)
- Flint, Michigan (1)
- Fluoropolymer coating (3)
- Forms of Corrosion (4)
- Freshwater salinization (1)
- Galvanic (1)
- Galvanic Corrosion (4)
- General Corrosion (4)
- General Tips (1)
- glossary (1)
- Hand tools (1)
- honoree night (1)
- Industrial Application (3)
- Industrial Safety (2)
- Industry Best Practices (1)
- Industry Standards (1)
- infrastructure (3)
- Inspection (1)
- integrity management (1)
- Intergranular Corrosion (1)
- Intumescent Coatings (1)
- key note speaker (1)
- Machine Learning (1)
- Maintenance (2)
- Maritime Coatings (11)
- Maritime industry (11)
- Master Painters Institute (2)
- material protection (1)
- materials performance (1)
- materials science (1)
- Membership (2)
- Membership Benefits (2)
- Michio Kaku (1)
- Microbiological forms (1)
- Microbiologically influenced corrosion-MIC (11)
- Military (2)
- Mineral constituents (1)
- MnDOT (1)
- MPI (3)
- mpi awards (1)
- mpi champion awards (1)
- mpi training (1)
- MPI Update (1)
- National Defense Authorization Act (1)
- national security (1)
- Navy (1)
- nickel-based alloys (1)
- Non-Destructive Testing (1)
- nuclear (1)
- nuclear Materials (1)
- nuclear reactor technology (1)
- Oil and Gas (2)
- Oil Fields (1)
- Organic matter (1)
- Oxgen (1)
- Paint and Protective coatings (32)
- Paint specification (1)
- pcs certification (1)
- Personal Protective Equipment (3)
- Petrochemical Plant Fireproofing Methods (1)
- Petrochemical Plants (1)
- Pipeline (2)
- Pitting Corrosion (2)
- Pitting Detection (1)
- Power plant (1)
- Power tools (1)
- PPE (3)
- professional certification (2)
- professional development (1)
- Protective Coatings (6)
- protective coatings industry (1)
- protective coatings specialist (1)
- quality assurance (1)
- radiation-resistant materials (1)
- Real-Time Corrosion Monitoring in Oil Fields (1)
- Rebar Corrosion (2)
- rectifier (1)
- Reliability (1)
- Remote monitoring and drones (4)
- Repaint (1)
- Restoration (1)
- ride maintenance (1)
- Road deicers (1)
- Roads and bridges (1)
- Roller coaster (1)
- Rust (1)
- sacrificial anodes (1)
- Safety (5)
- Safety Standards (2)
- Salt pollution (1)
- Sensors (1)
- service awards (2)
- Ship Coatings (9)
- Shiptanks (1)
- Standards (9)
- Standards Committees (1)
- Steel (8)
- Steel Reinforcement (2)
- Stress Corrosion Cracking (1)
- Structural Steel (1)
- study tips (1)
- Surface Preparation (13)
- Sustainability (1)
- Sustainability and corrosion (7)
- terminology (1)
- Tools (1)
- Turbine (1)
- Types of Corrosion (1)
- Uniform Corrosion (1)
- us army core of engineers (1)
- Water crisis (1)
- Water pipe corrosion (1)
- Water quality (1)
- Water tank coatings (5)
- Water/treatment infrastructure (20)
- Waterway salinity (1)
- Workforce development (1)
- WRDA (1)