Tips for the QA/QC protective coatings inspection
October 1, 2020 •Corrosion CONTROLLED, Corrosion Essentials, M&I
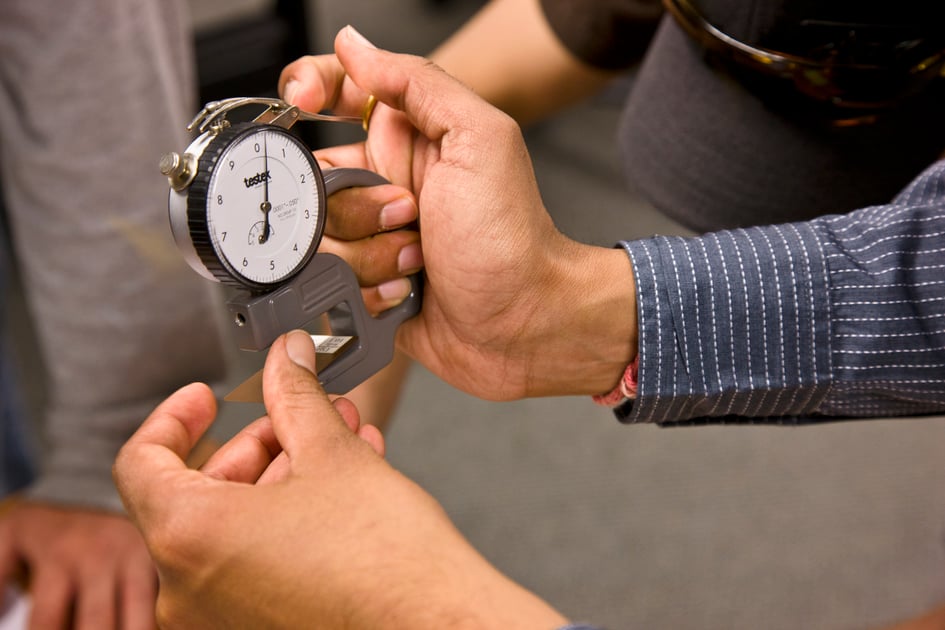
Here are some essential tools and important tips that can help with completing quality assurance (QA) of the protective coatings inspection quality control (QC) process -- from inspector training, pre-construction meetings, data sharing and coordination, to final inspection.
Whether providing QA in person or remotely as can often be the case during the novel coronavirus disease 2019 (COVID-19) pandemic, establishing good communication and relationships is key to success.
Training
QC inspectors used should be professionally trained. At a minimum, QC inspectors should be required to attend a 24-hour course based on ASTM International’s D3276, “Standard Guide for Painting Inspectors (Metal Substrates). The NACE Coating Inspector Program (CIP) Level 1 or SSPC’s Protective Coatings Inspector Program (PCI) Level 1 would provide a solid educational foundation to inspection.
Equipment
QC inspectors should have the proper equipment for the job and know how to use it; equipment shouldn’t be buried deep in a filing cabinet or still in the manufacturer’s box – sure signs it has not seen daily use. Additionally, check that the available equipment is in working order. Depending on the project, calibration records may be required.
Site-specific inspection plan
Before the pre-construction meeting, see that the contractor has developed a site-specific QC plan that reflects an understanding of the specification and the products to be used. The “canned” plan on the contractor’s server is a start, but the actual plan must identify each specification requirement, the testing frequency and method, the equipment to be used, and the acceptance criteria. Very often, this exercise identifies deficiencies in the specification and conflicts with the manufacturer’s written recommendations. If the contractor has a quality, site-specific QC plan, development of the QA plan is made easier.
Pre-construction meeting
Even on small projects, a pre-construction meeting is a must. If doing a remote QA, virtual attendance is more than acceptable. If discrepancies between the specification, the manufacturer’s recommendations, and the contractor’s standard operations have not been resolved, this is the time and place to do it — before the work begins. While others may attend, it is critical that those involved in the day-to-day operations attend the meeting, including the owner’s on-site representative, the coatings contractor’s superintendent or foreman, the QC inspector(s), and the QA inspector(s). While typically not involved daily, a representative from the paint manufacturer should also be invited.
In addition to resolving differences, the pre-construction meeting should first and foremost address safety and then crew size, work hours, application methods, chloride testing, inspection duties and timing, documentation, and distribution. Document the pre-construction meeting and distribute the minutes to all those involved.
Daily Painting Inspection Reports (DPIRs)
As implied by the name, these QC reports should be generated daily and made available to QA no later than the next morning. If reports are only showing up weekly, it is suspect whether QC activities are happening when they should. It is acceptable and often desirable to tailor the DPIR for a project, but if readings such as ambient conditions are consistent and acceptable all day or follow the same pattern every day, questions should be asked. If QA is being handled remotely, check the weather history at the nearest airport; however, this is not an acceptable method for the QC inspector.
When dry film thickness (DFT) readings are always in the specified range, the red flag goes up again. Applying paint by brush, roller, or spray — especially on complex surfaces — typically yields a range of thicknesses. In most cases, thickness issues can be corrected. For example, if the epoxy intermediate coat is too thin, another coat can be added before applying the polyurethane topcoat. Making up total DFT deficiencies with the polyurethane topcoat is more expensive and may have recoat window issues.
Based on the criteria in the inspection plan, the DPIR should include the specified value, the actual measured value, whether or not it is acceptable, and, if unacceptable, the details of the repair or disposition (wherein the owner might decide to accept the deficiency and/or a deduction). The QC report cannot simply state that the surface temperature is “acceptable.” It must report an actual temperature.
Nomenclature
Depending on the complexity of the structure, a naming and abbreviation scheme can be developed for precise communication between the QC and QA personnel regarding locations in the inspection reports and pictures. If possible, use nomenclature that is already in use at the facility instead of creating arbitrary divisions or zones. For example, below is a facility’s nomenclature for a long conveyor running between a river and a tower:
LC = Long Conveyor
CL (1–8) = Conveyor Leg Support (1–8)
T (1–7) = Truss (1–7)
TC = Top Cord
BC = Bottom Cord
WC = West Cord
EC = East Cord
CB = Cross Brace (corresponding to support leg — from ground up)
AB = Angle Brace
Pictures
Take pictures daily and share them with QA along with the DPIR. In today’s digital world with cloud servers, it is easy to take and share numerous pictures. Clearly label and date all pictures; include long-range as well as close-up photos. Magnetic rulers are available to provide scale for close-up pictures. Fingers, pens, and coins will also work to provide scale in photos.
Partial Kits
While most specifications and good coating practices do not allow for the mixing of partial kits of multi-component materials, in reality, it does occur. If a contractor knows ahead of time that partial kits will be mixed, the measuring procedure provided by the paint manufacturer should be included in the work plan and explicit permission should be requested from the owner to deviate from the specification. QC documentation of each mix is necessary so that partial kit mixes can be easily identified, especially if there is a mixing issue.
As part of the on-site QA visit, look for measuring cups and/or scales. If not there, consider this an indication that the procedure is not being followed. If possible and most desirable, the contractor can purchase and mix both large and small kits to comply with the no-partial-kit requirement.
Steel Repairs
Coating projects requiring steel repairs ideally should be done well before coating contractor work begins. If only paint is being assessed for quality, ask whether other contractor activities are taking place at the site or structure. These other activities can adversely affect the painting.
Final recommendations
Consider adding language to the engineers’ and architects’ specifications to explicitly require contractor QC. Many projects are not large enough or complex enough to justify retaining a full-time, third-party QA inspector, and the coatings contractor is then overseen by an untrained, resident observer. By specifying and enforcing QC inspection, even if performed by the contractor’s superintendent or foreman, it is possible for QA project to be done both remotely and safely.
For more coatings tips as well as the latest techniques and technologies in the industry, sign up for NACE’s CoatingsPro Magazine. It's FREE!
Source: September 2020 issue of CoatingsPro Magazine, authored by Troy Fraebel, Vice President of Protective Coating Services for AB Kaelin, LLC.
FREE DOWNLOADS
White Paper: An Action Plan for Reducing Pipeline Failures, Costs with Corrosion in the Water Sector
Special Report: The Future of Corrosion Control, Insights from the Experts
Get Updates
Featured Articles
Categories
- 2024 Olympics (1)
- 2024 Water Resource Development Act (1)
- Abrasive Blasting (1)
- Advanced coating materials (9)
- advanced coatings (1)
- Advanced Corrosion Control in Oil and Gas Industry (2)
- Advocacy (3)
- AI (2)
- Aircraft (1)
- Alkanization (1)
- AMPP (4)
- AMPP Annual Conference + Expo (4)
- ampp awards (1)
- ampp certification (2)
- Ampp Chapters (1)
- AMPP conference (1)
- AMPP logo (1)
- Ampp Membership (1)
- Ampp Standards (1)
- ampp training (1)
- Amusement parks (4)
- Architectural (1)
- Architectural Coatings (2)
- argonne national laboratory (1)
- Artificial Intelligence (1)
- Asset integrity (11)
- Asset maintenance (3)
- Asset Protection (1)
- awards (2)
- Bim Software (1)
- Biodeterioration of materials (5)
- Biofouling (4)
- Blasting (1)
- Bridges (4)
- career advancement (2)
- career development (2)
- cathodic protection (2)
- Cathodic Protection-CP (16)
- Ceramic epoxies (1)
- Certification (3)
- certification study guide (1)
- Chemical Injection (1)
- CIP (1)
- Civil Engineering (1)
- clean energy (1)
- Coating inspector (2)
- coating inspector job roles (1)
- Coating inspector jobs (2)
- Coating inspector program (2)
- Coatings (16)
- Coatings Application (3)
- coatings certification (1)
- Coatings failures (2)
- Coatings Industry (2)
- coatings inspection (1)
- Coatings inspector (2)
- Coatings measurement and inspection (9)
- coatings project management (1)
- Coatings Systems (1)
- Cold stress (1)
- Concrete (13)
- Concrete corrosion (1)
- concrete cracking (1)
- Conference and Events (2)
- Corrosion (21)
- Corrosion Basics (5)
- corrosion certification (1)
- Corrosion Control (16)
- Corrosion Control and Management (23)
- corrosion engineering (1)
- Corrosion Essentials (20)
- corrosion mitigation (1)
- corrosion of steel (1)
- corrosion policy (1)
- Corrosion Prevention (10)
- corrosion resistance (1)
- corrosion resources (1)
- Corrosion Under Insulation (1)
- cost of corrosion (1)
- Crevice Corrosion (1)
- Cui (1)
- Data Monitoring (1)
- decarbonization (1)
- defense infrastructure (1)
- Department of Defense (4)
- Deposition corrosion (1)
- Dissimilar Metal Corrosion (1)
- Dissolved gases (1)
- DoD (3)
- Education (2)
- Energy industry (9)
- entertainment industry (1)
- Epoxy (2)
- exam preparation (1)
- Fireproofing (1)
- Flexible coatings (2)
- Flint, Michigan (1)
- Fluoropolymer coating (3)
- Forms of Corrosion (4)
- Freshwater salinization (1)
- Galvanic (1)
- Galvanic Corrosion (4)
- General Corrosion (4)
- General Tips (1)
- glossary (1)
- Hand tools (1)
- honoree night (1)
- Industrial Application (3)
- Industrial Safety (2)
- Industry Best Practices (1)
- Industry Standards (1)
- infrastructure (3)
- Inspection (1)
- integrity management (1)
- Intergranular Corrosion (1)
- Intumescent Coatings (1)
- key note speaker (1)
- Machine Learning (1)
- Maintenance (2)
- Maritime Coatings (11)
- Maritime industry (11)
- Master Painters Institute (2)
- material protection (1)
- materials performance (1)
- materials science (1)
- Membership (2)
- Membership Benefits (2)
- Michio Kaku (1)
- Microbiological forms (1)
- Microbiologically influenced corrosion-MIC (11)
- Military (2)
- Mineral constituents (1)
- MnDOT (1)
- MPI (3)
- mpi awards (1)
- mpi champion awards (1)
- mpi training (1)
- MPI Update (1)
- National Defense Authorization Act (1)
- national security (1)
- Navy (1)
- nickel-based alloys (1)
- Non-Destructive Testing (1)
- nuclear (1)
- nuclear Materials (1)
- nuclear reactor technology (1)
- Oil and Gas (2)
- Oil Fields (1)
- Organic matter (1)
- Oxgen (1)
- Paint and Protective coatings (32)
- Paint specification (1)
- pcs certification (1)
- Personal Protective Equipment (3)
- Petrochemical Plant Fireproofing Methods (1)
- Petrochemical Plants (1)
- Pipeline (2)
- Pitting Corrosion (2)
- Pitting Detection (1)
- Power plant (1)
- Power tools (1)
- PPE (3)
- professional certification (2)
- professional development (1)
- Protective Coatings (6)
- protective coatings industry (1)
- protective coatings specialist (1)
- quality assurance (1)
- radiation-resistant materials (1)
- Real-Time Corrosion Monitoring in Oil Fields (1)
- Rebar Corrosion (2)
- rectifier (1)
- Reliability (1)
- Remote monitoring and drones (4)
- Repaint (1)
- Restoration (1)
- ride maintenance (1)
- Road deicers (1)
- Roads and bridges (1)
- Roller coaster (1)
- Rust (1)
- sacrificial anodes (1)
- Safety (5)
- Safety Standards (2)
- Salt pollution (1)
- Sensors (1)
- service awards (2)
- Ship Coatings (9)
- Shiptanks (1)
- Standards (9)
- Standards Committees (1)
- Steel (8)
- Steel Reinforcement (2)
- Stress Corrosion Cracking (1)
- Structural Steel (1)
- study tips (1)
- Surface Preparation (13)
- Sustainability (1)
- Sustainability and corrosion (7)
- terminology (1)
- Tools (1)
- Turbine (1)
- Types of Corrosion (1)
- Uniform Corrosion (1)
- us army core of engineers (1)
- Water crisis (1)
- Water pipe corrosion (1)
- Water quality (1)
- Water tank coatings (5)
- Water/treatment infrastructure (20)
- Waterway salinity (1)
- Workforce development (1)
- WRDA (1)