Recoating an amusement park ride for corrosion protection & aesthetics
November 13, 2020 •Corrosion CONTROLLED, Corrosion Essentials, Coatings
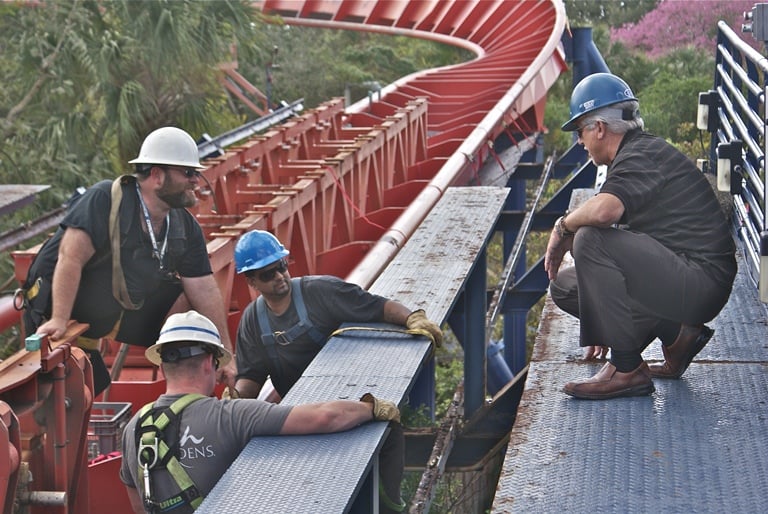
Painting an amusement park roller coaster is a painstaking work of art. The owner of the roller coaster wants the complex metal structure to look colorful and awe-inspiring, leaving patrons with breathless anticipation and excitement. However, the painting of this masterpiece is a major undertaking that involves many hours of preparation and hands-on attention to ensure the coatings work helps to combat the potentially costly effects of corrosion.
Corrosion, coating, & amusement park ride review
Such a coatings project typically starts with the maintenance department and/or engineering department identifying any existing corrosion and/or repairs that are needed and then determining a timeline for rehabilitation and repainting of the roller coaster.
A third-party paint consultant and/or a paint manufacturer rep are often asked to review the existing condition of the coaster and make recommendations to the owner and his or her team. Often, a rep from the original coating manufacturer is asked to be involved as well.
The adhesion of the existing coating and the film thickness should both be checked and evaluated in accordance with the coating standards set forth by the International Organization for Standardization (ISO) and NACE International and the Society for Protective Coatings (SSPC), which work concurrently. Many times, these two tests will set the stage for the coating recommendation and selection. If the adhesion is good and the film thickness is not too great, typically the existing coating system is deemed acceptable and an overcoat system is recommended. Conversely, if the adhesion is poor and/or the film is too thick, the existing coating system is usually removed, and a new paint system is installed. Once the testing is completed, all contributing parties should meet to discuss the findings and create a specification based on criteria and recommendations.
The criteria should include such questions as:
• What is the timeframe for painting the roller coaster?
• What are the budget requirements, so that a life cycle cost can be developed?
• What coatings system will be recommended based on the results of the tests?
Also included in the discussion should be any concerns about long-term corrosion protection, color requirements, and gloss retention of the finish, which are generally very important to a theme park owner. Color palettes of various finishes, such as urethanes with a clear coat, polysiloxanes, and in some cases fluoropolymer finishes, will all be reviewed as potential coatings options. Quite often, the issue of who will provide the coating inspection will also come into play. For example, should the painting contractor have his or her own inspector on staff, or is it better for the specific project to hire a third-party inspector? (This is a decision usually driven by cost and the experience of the contractor.)
After all the criteria for rehabilitation and repainting of the roller coaster are established, the specification can be prepared by the consultant and/or paint manufacturer. When the documents are ready, the owner will determine when the project will be put out for bid. This timing decision can be challenging for the owner because he or she must consider things such as potential lost revenue during installation, crowd control, safety of park patrons, and even the best time of year to paint due to weather variables.
The pre-bid coatings meeting
Following the completion of the project scope and specification, the owner will usually call for a pre-bid meeting. In most cases, they will invite specific contractors to bid on the project.
Contractors who specialize in painting roller coasters are true artists in their field. They understand the intricacies of performing this work and the importance of completing a project within a specific time frame. Their portfolio of past work will demonstrate the ability to manage projects of all sizes, provide the supervisors and personnel necessary to meet the timeline, and identify the budget, safety requirements, quality control /quality assurance, and special equipment needed to complete the project.
Most theme park owners have a proven list of three or four qualified contractors with roller coaster repainting experience on their roster. These contractors may hail from all areas of the country, and depending on their specialized skill and location, can greatly affect the overall cost of the project.
The pre-bid meeting should include the owner’s representative, the identified contractors, paint consultants, and/or the paint manufacturer. The purpose of the meeting is to communicate and clarify the requirements of the project before it starts. If there are any questions about the specification, the consultant and/or paint manufacturer should be present to provide answers. If the owner elected to hire an inspector for the project, that company should be represented at the meeting as well.
The post-bid coatings meeting
After the award of the contract, the painting contractor will need to mobilize and prepare to meet the strict guidelines outlined in the specification, which serves as the backbone of the project.
Some of the challenges the contractor must consider and factor in the bid beforehand include:
• working through unpredictable weather conditions,
• potential night work,
• logistics of moving large equipment in small work areas, and
•painting while the theme park is in operation.
Additionally, if the owner has hired a third-party inspection company, the painting contractor and inspector must work together. In most cases the job of the inspector is to inspect the contractor’s work, then record and document his or her findings. Sometimes the owner gives the inspector the authority to stop the project if there is a conflict in the job requirements. These levels of authority are usually established at the pre-bid meeting.
When the project is completed the owner will call for a final inspection. This final walk-through could include the owner representative, inspector, contractor, paint consultant, and/or the paint manufacturer. If the project meets the owner’s satisfaction, he or she should issue a final release. Some projects call for an extended warranty by the paint manufacturer to ensure the coating system’s performance. In that case, a copy of the work release and inspection report should be submitted to the paint manufacturer, who should then issue the warranty. Many times, a labor warranty is issued to the owner by the painting contractor as well.
Once all of the documents are properly issued, the triangle of success — owner, paint manufacturer, and contractor — is complete, and the gleaming roller coaster work of art is put back in operation for thousands of park guests to enjoy for years to come.
See the results of the preparations outlined here. Read, “Roller Coaster Re-Coating Reaches New Heights at Busch Gardens,” at Coatingspromag.com.
For more coatings tips as well as the latest techniques and technologies in the industry, sign up for NACE’s CoatingsPro Magazine. Subscriptions are FREE.
Source: Originally published in CoatingsPro Magazine, authored by Bob Wolf, NACE Level 3 Coating Inspector and SSPC Protective Coating Specialist, International Paint LLC. Photo courtesy of Service Painting Corp.
FREE DOWNLOADS
White Paper: An Action Plan for Reducing Pipeline Failures, Costs with Corrosion in the Water Sector
Special Report: The Future of Corrosion Control, Insights from the Experts
Get Updates
Featured Articles
Categories
- 2024 Olympics (1)
- 2024 Water Resource Development Act (1)
- Abrasive Blasting (1)
- Advanced coating materials (9)
- advanced coatings (1)
- Advanced Corrosion Control in Oil and Gas Industry (2)
- Advocacy (3)
- AI (2)
- Aircraft (1)
- Alkanization (1)
- AMPP (4)
- AMPP Annual Conference + Expo (4)
- ampp awards (1)
- ampp certification (2)
- Ampp Chapters (1)
- AMPP conference (1)
- AMPP logo (1)
- Ampp Membership (1)
- Ampp Standards (1)
- ampp training (1)
- Amusement parks (4)
- Architectural (1)
- Architectural Coatings (2)
- argonne national laboratory (1)
- Artificial Intelligence (1)
- Asset integrity (11)
- Asset maintenance (3)
- Asset Protection (1)
- awards (2)
- Bim Software (1)
- Biodeterioration of materials (5)
- Biofouling (4)
- Blasting (1)
- Bridges (4)
- career advancement (2)
- career development (2)
- cathodic protection (2)
- Cathodic Protection-CP (16)
- Ceramic epoxies (1)
- Certification (3)
- certification study guide (1)
- Chemical Injection (1)
- CIP (1)
- Civil Engineering (1)
- clean energy (1)
- Coating inspector (2)
- coating inspector job roles (1)
- Coating inspector jobs (2)
- Coating inspector program (2)
- Coatings (16)
- Coatings Application (3)
- coatings certification (1)
- Coatings failures (2)
- Coatings Industry (2)
- coatings inspection (1)
- Coatings inspector (2)
- Coatings measurement and inspection (9)
- coatings project management (1)
- Coatings Systems (1)
- Cold stress (1)
- Concrete (13)
- Concrete corrosion (1)
- concrete cracking (1)
- Conference and Events (2)
- Corrosion (21)
- Corrosion Basics (5)
- corrosion certification (1)
- Corrosion Control (16)
- Corrosion Control and Management (23)
- corrosion engineering (1)
- Corrosion Essentials (20)
- corrosion mitigation (1)
- corrosion of steel (1)
- corrosion policy (1)
- Corrosion Prevention (10)
- corrosion resistance (1)
- corrosion resources (1)
- Corrosion Under Insulation (1)
- cost of corrosion (1)
- Crevice Corrosion (1)
- Cui (1)
- Data Monitoring (1)
- decarbonization (1)
- defense infrastructure (1)
- Department of Defense (4)
- Deposition corrosion (1)
- Dissimilar Metal Corrosion (1)
- Dissolved gases (1)
- DoD (3)
- Education (2)
- Energy industry (9)
- entertainment industry (1)
- Epoxy (2)
- exam preparation (1)
- Fireproofing (1)
- Flexible coatings (2)
- Flint, Michigan (1)
- Fluoropolymer coating (3)
- Forms of Corrosion (4)
- Freshwater salinization (1)
- Galvanic (1)
- Galvanic Corrosion (4)
- General Corrosion (4)
- General Tips (1)
- glossary (1)
- Hand tools (1)
- honoree night (1)
- Industrial Application (3)
- Industrial Safety (2)
- Industry Best Practices (1)
- Industry Standards (1)
- infrastructure (3)
- Inspection (1)
- integrity management (1)
- Intergranular Corrosion (1)
- Intumescent Coatings (1)
- key note speaker (1)
- Machine Learning (1)
- Maintenance (2)
- Maritime Coatings (11)
- Maritime industry (11)
- Master Painters Institute (2)
- material protection (1)
- materials performance (1)
- materials science (1)
- Membership (2)
- Membership Benefits (2)
- Michio Kaku (1)
- Microbiological forms (1)
- Microbiologically influenced corrosion-MIC (11)
- Military (2)
- Mineral constituents (1)
- MnDOT (1)
- MPI (3)
- mpi awards (1)
- mpi champion awards (1)
- mpi training (1)
- MPI Update (1)
- National Defense Authorization Act (1)
- national security (1)
- Navy (1)
- nickel-based alloys (1)
- Non-Destructive Testing (1)
- nuclear (1)
- nuclear Materials (1)
- nuclear reactor technology (1)
- Oil and Gas (2)
- Oil Fields (1)
- Organic matter (1)
- Oxgen (1)
- Paint and Protective coatings (32)
- Paint specification (1)
- pcs certification (1)
- Personal Protective Equipment (3)
- Petrochemical Plant Fireproofing Methods (1)
- Petrochemical Plants (1)
- Pipeline (2)
- Pitting Corrosion (2)
- Pitting Detection (1)
- Power plant (1)
- Power tools (1)
- PPE (3)
- professional certification (2)
- professional development (1)
- Protective Coatings (6)
- protective coatings industry (1)
- protective coatings specialist (1)
- quality assurance (1)
- radiation-resistant materials (1)
- Real-Time Corrosion Monitoring in Oil Fields (1)
- Rebar Corrosion (2)
- rectifier (1)
- Reliability (1)
- Remote monitoring and drones (4)
- Repaint (1)
- Restoration (1)
- ride maintenance (1)
- Road deicers (1)
- Roads and bridges (1)
- Roller coaster (1)
- Rust (1)
- sacrificial anodes (1)
- Safety (5)
- Safety Standards (2)
- Salt pollution (1)
- Sensors (1)
- service awards (2)
- Ship Coatings (9)
- Shiptanks (1)
- Standards (9)
- Standards Committees (1)
- Steel (8)
- Steel Reinforcement (2)
- Stress Corrosion Cracking (1)
- Structural Steel (1)
- study tips (1)
- Surface Preparation (13)
- Sustainability (1)
- Sustainability and corrosion (7)
- terminology (1)
- Tools (1)
- Turbine (1)
- Types of Corrosion (1)
- Uniform Corrosion (1)
- us army core of engineers (1)
- Water crisis (1)
- Water pipe corrosion (1)
- Water quality (1)
- Water tank coatings (5)
- Water/treatment infrastructure (20)
- Waterway salinity (1)
- Workforce development (1)
- WRDA (1)