How to ensure long-term protective coating success
August 26, 2020 •Corrosion CONTROLLED, Corrosion Essentials, Coatings
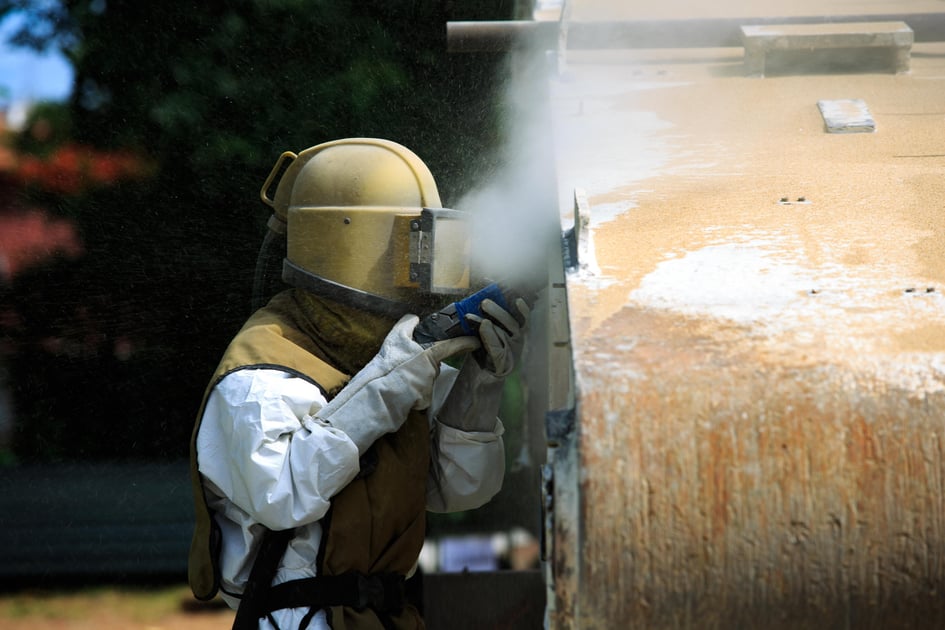
Extending asset life, reducing maintenance with corrosion control
Corrosion poses a threat to all infrastructure through the degradation of structures such as buildings, roads, bridges, pipelines, and towers, and the economic impact of corrosion represents an annual cost of billions of dollars to the economy. It is important that owners and operators of high-value assets understand the cost implications of ignoring the effects of corrosion. There are many advantages of planning for corrosion control and mitigation. Two of the main ones are that the life of an asset is extended, making it more profitable; and the asset’s maintenance time and costs are reduced, which enables its increased utilization.
Ways to protect assets
According to Justin Rigby, coatings consultant at Remedy Asset Protection (Melbourne, Victoria, Australia) and a NACE International level 3 coatings inspector, there are two main ways to protect an asset from corrosion. One is to alter the physical properties of a metal by using a technology such as cathodic protection to impress a current into a structure to minimize corrosion. The other, is to physically isolate a structure from the environment by applying a protective coating. It is important that a protective coating project is carefully planned, he says. Avoid underestimating the technical complexity of a project, especially if the coating is to be applied to an existing structure and more so if the site is in a remote location.
Protecting assets through coatings
A protective coating is not just paint, rather, it is an engineered product that undergoes rigorous product development to provide specific properties that will protect a structure from its service environment,” says Rigby. “The most important considerations are assessment of the service environment and selection of the required coatings.”
There is a wide selection of coatings products available to the market, so it is essential that the appropriate coatings system is chosen. There is no single product that meets every coating situation, so a compromise may need to be made during the planning stages of a project.
According to Rigby, a good specification will reference AS/NZ 2312,1 categorize the service environment according to its corrosivity, and then nominate a coating system based on the desired design life of the coating. He recommends seeking advice from a competent colleague or external consultant when building a specification and selecting the most appropriate coating system. The major coatings manufacturers, including AkzoNobel, Altex, Dulux, Jotun, PPG, Sherwin-Williams, and Valspar, are also good sources for reputable advice.
Traditionally, coatings protect a structure by creating a physical barrier to the environment. Modern technology has developed active pigments that are being incorporated into primers to provide additional protection. Active anticorrosive pigments are added to primers that can give further protection for areas with coating damage in addition to their barrier effect. These pigments prevent corrosion of a metal substrate by building up permanently passive conditions at the metal surface and/or by a build-up of solid compounds that fill in the damaged area of the coating.
Key aspects to managing a coatings project
It is important to be flexible and adaptable when developing protective coating projects. “A protective coatings project, managed well, provides owners with great outcomes,” Rigby states. He recommends spending time with a consultant at the prestart stages of a project to help identify areas of risk or looking to such organizations as NACE International or the Australasian Corrosion Association (ACA) for corrosion management best practices.
Material specifications and applicator competence
Once a coatings project is underway, there are several aspects that need to be carefully managed. It is important to understand the competence of the applicator and ensure the main contractor does not accept lower-quality materials that do not meet specifications. “Asset owners must understand that their 'whole of life' costs are not necessarily a priority for the main contractor when a new asset is built, and could be diametrically opposed,” says Graham Matthews, technical director of TBS in Auckland, New Zealand. “The contractor may see an opportunity to save a few dollars by amending a specification and the structure may survive the guarantee period, but the resultant future maintenance costs are far higher.”
Additionally, the technicians chosen to apply a coating must have the appropriate skills. Obvious selection criteria are experience with the protective material and the equipment used to apply it to a structure. A less obvious criterion, especially for any sort of tower structure, is abseiling (rappelling) skills; technicians might have to be in a harness and suspended in mid-air, which requires a mix of physical and psychological attributes.
Certification of compliance
One vital aspect of coatings projects is to have compliance certification that the job complies with all the appropriate legislation, regulations, and standards. There are two ways to achieve this—either to pay for third-party inspection or engage a contracting firm that has staff members who are certified coatings Inspectors. This will provide peace of mind to customers that quality is “built in” throughout project planning and execution.
Shop vs onsite application
The cost to coat a structure with an appropriate and effective protective material varies depending on whether it is applied in a workshop or on site. “The average cost to apply a three-coat system in a workshop may be around $80 per square meter,” says Matthews. “On site, this might increase to $300 per square meter or higher.
There are, however, variations. For example, repainting the complex latticework of a viaduct in Australia using lead paint cost ~NZD $1,000/m2. The NZD $12 million refurbishment of the heritage-listed structure required scaffolds up to 80-m high, an on-site team of 30 people, as well as deployment of more than NZD $4 million worth of specialized plant and equipment.
In comparison, touch-up repairs to the country’s iconic Auckland Harbour Bridge using lead-free paint cost only NZD $150/m2 since the bridge was designed with good access systems.
Geographic considerations
While there are many standards relating to the application of protective surface coatings, compromises may sometimes need to be made. When planning a protective coating project, it is important to take factors such as the geography, access to the structure, and climate into account, all of which impact the cost of the project.
If a structure to be protected is in a remote location, it will be necessary to select the most cost-effective means of transporting materials and personnel to the site. Additionally, remote sites may be exposed to climatic extremes that impact coating application. For example, monsoon rains in tropical regions would make it difficult to spray a coating onto any type of structure.
Environmental considerations
The health and safety analysis of a project must look at how to effectively protect a structure and address any environmental considerations. It must also consider how to properly apply the coating to minimize its effects on the surrounding areas as well as protect the technician who might be working in a harness tethered meters above the ground. “When you get to site, there may be odd arrangements of pylons and bracing, making it difficult for a technician to access all parts of a structure to apply a coating,” adds Rigby.
Where coatings projects go wrong
There are relatively few reasons why protective coatings projects are unsuccessful; however, planners often do not fully comprehend the complexity of many coatings projects and, as a consequence, fail to invest the time and resources to manage them effectively, which results in substantial cost implications when things go wrong. A lack of detailed design information for a structure sometimes means there is poor selection of structural materials, such as dissimilar metals, which means the coating options are restricted (i.e., a coating for one metal is most likely inappropriate for the other).
For coatings technologies, techniques, and tips, sign up for NACE’s CoatingsPro Magazine – free monthly subscriptions to industry professionals.
Source: Originally appeared on materialsperformance.com by P. Morrosion, Australasian Corrosion Association.
FREE DOWNLOADS
White Paper: An Action Plan for Reducing Pipeline Failures, Costs with Corrosion in the Water Sector
Special Report: The Future of Corrosion Control, Insights from the Experts
Get Updates
Featured Articles
Categories
- 2024 Olympics (1)
- 2024 Water Resource Development Act (1)
- Abrasive Blasting (1)
- Advanced coating materials (9)
- advanced coatings (1)
- Advanced Corrosion Control in Oil and Gas Industry (2)
- Advocacy (3)
- AI (2)
- Aircraft (1)
- Alkanization (1)
- AMPP (4)
- AMPP Annual Conference + Expo (4)
- ampp awards (1)
- ampp certification (2)
- Ampp Chapters (1)
- AMPP conference (1)
- AMPP logo (1)
- Ampp Membership (2)
- Ampp Standards (1)
- ampp training (1)
- Amusement parks (4)
- Architectural (1)
- Architectural Coatings (2)
- argonne national laboratory (1)
- Artificial Intelligence (1)
- Asset integrity (11)
- Asset maintenance (3)
- Asset Protection (1)
- awards (3)
- Bim Software (1)
- Biodeterioration of materials (5)
- Biofouling (4)
- Blasting (1)
- Bridges (4)
- career advancement (3)
- career development (2)
- cathodic protection (2)
- Cathodic Protection-CP (16)
- Ceramic epoxies (1)
- Certification (3)
- certification study guide (1)
- Chemical Injection (1)
- CIP (1)
- Civil Engineering (1)
- clean energy (1)
- Coating inspector (2)
- coating inspector job roles (1)
- Coating inspector jobs (2)
- Coating inspector program (2)
- Coatings (17)
- Coatings Application (3)
- coatings certification (1)
- Coatings failures (2)
- Coatings Industry (2)
- coatings inspection (1)
- Coatings inspector (2)
- Coatings measurement and inspection (9)
- coatings project management (1)
- Coatings Systems (1)
- Cold stress (1)
- Concrete (13)
- Concrete corrosion (1)
- concrete cracking (1)
- Conference and Events (2)
- Corrosion (23)
- Corrosion Basics (5)
- corrosion certification (1)
- Corrosion Control (16)
- Corrosion Control and Management (23)
- corrosion engineering (1)
- Corrosion Essentials (20)
- corrosion mitigation (1)
- corrosion of steel (1)
- corrosion policy (1)
- Corrosion Prevention (11)
- corrosion resistance (1)
- corrosion resources (1)
- Corrosion Under Insulation (1)
- cost of corrosion (1)
- Crevice Corrosion (1)
- Cui (1)
- Data Monitoring (1)
- decarbonization (1)
- defense infrastructure (1)
- Department of Defense (4)
- Deposition corrosion (1)
- Dissimilar Metal Corrosion (1)
- Dissolved gases (1)
- DoD (3)
- Education (2)
- EMERG (1)
- Energy industry (9)
- entertainment industry (1)
- Epoxy (3)
- exam preparation (1)
- Fireproofing (1)
- Flexible coatings (2)
- Flint, Michigan (1)
- Fluoropolymer coating (3)
- Forms of Corrosion (4)
- Freshwater salinization (1)
- Galvanic (1)
- Galvanic Corrosion (4)
- General Corrosion (4)
- General Tips (1)
- glossary (1)
- Hand tools (1)
- honoree night (1)
- Industrial Application (3)
- Industrial Safety (2)
- Industry Best Practices (1)
- Industry Standards (1)
- infrastructure (3)
- Infrastructure Durability (1)
- Inspection (1)
- integrity management (1)
- Intergranular Corrosion (1)
- Intumescent Coatings (1)
- key note speaker (1)
- leader (1)
- Machine Learning (2)
- Maintenance (2)
- Maritime Coatings (11)
- Maritime industry (11)
- Master Painters Institute (2)
- material protection (1)
- materials performance (1)
- materials science (1)
- Membership (2)
- Membership Benefits (2)
- Michio Kaku (1)
- Microbiological forms (1)
- Microbiologically influenced corrosion-MIC (11)
- Military (2)
- Mineral constituents (1)
- MnDOT (1)
- MPI (3)
- mpi awards (1)
- mpi champion awards (1)
- mpi training (1)
- MPI Update (1)
- National Defense Authorization Act (1)
- national security (1)
- Navy (1)
- nickel-based alloys (1)
- Non-Destructive Testing (1)
- nuclear (1)
- nuclear Materials (1)
- nuclear reactor technology (1)
- Oil and Gas (2)
- Oil Fields (1)
- Organic matter (1)
- Oxgen (1)
- Paint and Protective coatings (32)
- Paint specification (1)
- pcs certification (1)
- Personal Protective Equipment (3)
- Petrochemical Plant Fireproofing Methods (1)
- Petrochemical Plants (1)
- Pipeline (2)
- Pitting Corrosion (2)
- Pitting Detection (1)
- Polymer-Based Coatings (1)
- Power plant (1)
- Power tools (1)
- PPE (3)
- professional certification (2)
- professional development (1)
- Protective Coatings (6)
- protective coatings industry (1)
- protective coatings specialist (1)
- quality assurance (1)
- radiation-resistant materials (1)
- Real-Time Corrosion Monitoring in Oil Fields (1)
- Rebar Corrosion (2)
- rectifier (1)
- Reliability (1)
- Remote monitoring and drones (4)
- Repaint (1)
- Restoration (1)
- ride maintenance (1)
- Road deicers (1)
- Roads and bridges (1)
- Roller coaster (1)
- Rust (1)
- sacrificial anodes (1)
- Safety (5)
- Safety Standards (2)
- Salt pollution (1)
- Sensors (1)
- service awards (2)
- Ship Coatings (9)
- Shiptanks (1)
- Standards (9)
- Standards Committees (1)
- Steel (8)
- Steel Reinforcement (2)
- Stress Corrosion Cracking (1)
- Structural Steel (1)
- study tips (1)
- Surface Preparation (13)
- Sustainability (1)
- Sustainability and corrosion (7)
- terminology (1)
- Tools (1)
- Turbine (1)
- Types of Corrosion (1)
- Uniform Corrosion (1)
- us army core of engineers (1)
- Wastewater Systems (1)
- Water crisis (1)
- Water pipe corrosion (1)
- Water quality (1)
- Water tank coatings (5)
- Water/treatment infrastructure (20)
- Waterway salinity (1)
- Workforce development (1)
- WRDA (1)