Recoating a wastewater treatment tank
May 10, 2021 •Corrosion CONTROLLED, Infrastructure, Water
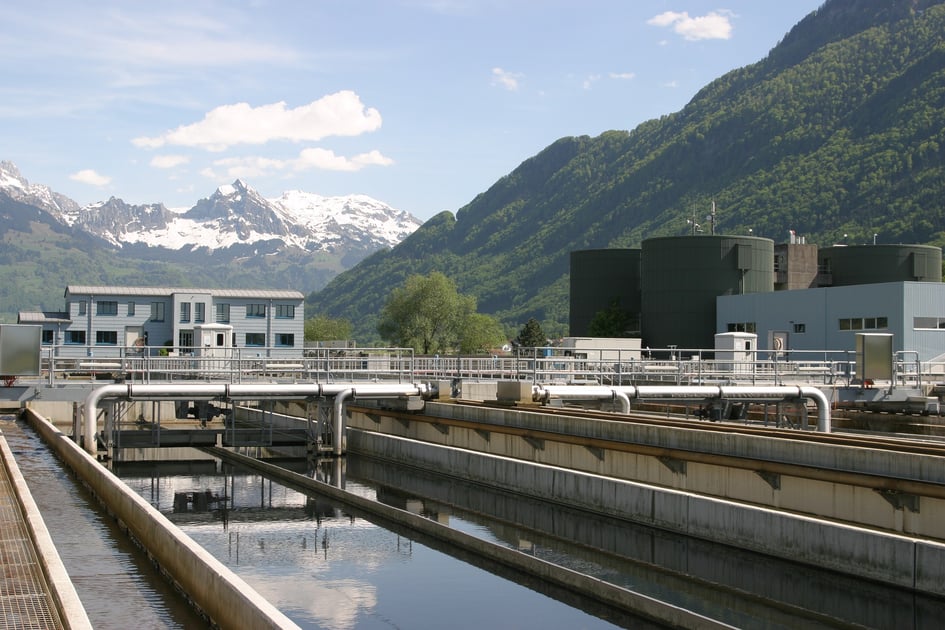
As part of a larger project at a New Hampshire based facility, John W. Egan Company was hired by the general contractor to prepare and coat the wastewater treatment plant’s four grit tanks, including the interior walls and floors of the tanks, all appurtenant channels, boxes, and other structures. Each tank is 70-feet-long by 10-feet-wide by 10-feet-deep (21.3 m x 3.1 m x 3.1 m) and has a tapered bottom and roof.
Grit tanks are important components in wastewater treatment plants that rid the influent wastewater of solids, such as road sand and other debris. “At this plant, wastewater is dropped into large tanks with air diffusers that work to decrease the density of the influent. The solids fall to the bottom of the tank and then a conveyor system moves all solids out from the influent before it enters the facility,” explained Robert “Junior” Belisle of the John W. Egan Company.
“The grit tanks are what I like to call an awkward diamond shape,” observed Belisle, who added that the tapered design would actually pose a bit of a logistical challenge as the project began. “We had to strategically place the scaffolding in the very center of each tank where there is a flat channel that is about 2-feet [0.6 m] wide. Our crew set up pivoted staging jacks and a constructed system scaffolding with safety rails by Safway,” said Belisle.
Arriving on the scene to begin the first phase, the John W. Egan crew found that the tanks had already been drained and washed down by the general contractor. The concrete tanks had existing coal tar epoxy coating that was worn down. “The condition of the concrete underneath the coating varied depending on the location in the tank. The head space where there was the most exposure to hydrogen sulfide was in pretty bad shape. The concrete in the middle of the tank was in decent shape, but the bottom where the grit collects definitely had abrasion damage,” stated Belisle.
Recoating wastewater tanks with limited downtime and space
Another challenge that the crew had to contend with was the job's tight timeframe. “The wastewater facility was in use the entire time, so only two tanks could be down at one time. The job was divided into two phases over the course of eight months. Each phase was approximately four weeks in length. We needed to get the tanks back in service as soon as we could,” said Belisle. He and his crew of three to four men worked diligently to meet milestones and keep the job on schedule.
In addition to racing the clock, space was at a premium for this job. The laydown area was very limited, and according to Belisle, all equipment had to be stacked in a single file line, making logistics a bit challenging at times.
One piece of good news for the crew, though, was that containment was relatively easy. “The very nature of the tank made it almost entirely self-contained. There is only a 4-foot [1.2 m] gap in the ceiling of the tank. We used tarps for the containment and hooked up a 40,000 cfm [1,133.0 m³/min.] Entech dust collector when we abrasive blasted the concrete,” explained Belisle.
Cleaning and preparing the concrete tank for recoating
The first step in preparing the concrete tanks to receive the new Sherwin-Williams coating system was for the team to power wash the entire area. Using a 5,000 psi (34.5 MPa) Mi-T-M power washer and an alkaline-based detergent manufactured by Great Lakes Laboratories and distributed by Sherwin-Williams, the crew removed all loose coating. It was then time for the team to abrasive blast the substrate to remove all remaining coating material and loose concrete.
“We used an Axxiom Schmidt trailer-mounted blast pot with Black Beauty abrasives to achieve a NACE 6/SSPC-SP-13/ICRI CSP 3–6 surface profile,” said Belisle. That’s Society for Protective Coatings (SSPC) Surface Preparation (SP) and International Concrete Repair Institute (ICRI) Concrete Surface Profile (CSP).
The crew was outfitted with Bullard blast helmets and Tyvek protective suits during the blasting process. Once the blasting was complete, the crew cleaned up all waste blast media using a 2,300 cfm (65.1 m³/min.) industrial vacuum manufactured by Vector Vacuums.
With the concrete prepped and ready to go, the crew repaired all areas of deterioration or where bugholes existed in the concrete. Sherwin-Williams’ Patching Compound for Concrete and Steel Seam FT 910 were trowel applied where necessary.
Little time for important primer recoat step
According to Belisle, one of the most important components of the Sherwin-Williams coating system is the Corobond 100 primer. This 100 percent solids epoxy primer helps prevent off-gassing. It was applied using a Titan 30:1 airless, gas-powered sprayer at a dry film thickness of 4–6 mils (101.6–152.4 microns). “It wasn’t as simple as spray applying the coating, however. This primer has a very short recoat window, so to counteract that, we blew clean silica sand over the uncured coating to re-establish the surface profile. Doing this provided an unlimited recoat window,” explained Belisle. The silica sand was sprayed on with a pneumatic broadcast gun by Kraft Tool.
With the recoat window issue addressed, the John W. Egan team applied Sherwin-Williams Cor Cote SC Mortar epoxy coat at an average dry film thickness of 125 mils (3,175.0 microns). This epoxy mortar coat was spray applied on both vertical and horizontal surfaces using a WIWA 12:1 airless pump and then troweled.
Some areas of the grit tanks received an additional coating system layer. In the headspace, where hydrogen sulfide exposure is greatest, and on the walls and floors of the sump pits where more abrasion resistance is needed, another coat of Sherwin-Williams Cor Cote SC Resin was applied at an average dry film thickness of 20 mils (508.0 microns).
Belisle pointed out that safety protocols were followed at all times on the job. “Gloves, safety glasses, and boots were worn at all times during the application process. Tyvek suits were also worn, especially when applying the patching material and mortar coat. When we spray applied any of the coatings, the guys wore 3M half-face respirators,” said Belisle.
Colder temperatures challenge coating application
Since the work was done in a tank environment, the New Hampshire weather patterns were less of an issue than they would have been in a more open area. However, with the last two tanks, colder temperatures did prove to be a bit of a challenge. “The temperatures were dropping — although there was no snow quite yet — and applying the coating could have become very difficult. Luckily, the air diffusers for the grit tanks were already installed. Because of this, we were able to blow warm air from the facility into the tanks. This kept the ambient temperature in the tanks where it needed to be for the coating system application,” stated Belisle.
After the work on each tank was complete, but before it was put back in service, Belisle and his superintendent used a DE Stearns high-voltage holiday detector to ensure that there were no bugholes or holidays in the Sherwin-Williams system. Any areas that required repair were addressed immediately, and the John W. Egan team then turned the tank over to the Manchester Wastewater Treatment Plant. “Although there were definitely some challenges on this job, all in all, everything went really well. The right coating system was chosen, and our crew was able to meet all deadlines and turn the tanks over on schedule,” said Belisle.
For more coatings tips as well as the latest techniques and technologies in the industry, sign up for CoatingsPro Magazine, free to industry professionals.
Source: Originally appeared online at coatingspromag.com; authored by Jennifer Frakes; image courtesy of the John W. Egan Company.
FREE DOWNLOADS
White Paper: An Action Plan for Reducing Pipeline Failures, Costs with Corrosion in the Water Sector
Special Report: The Future of Corrosion Control, Insights from the Experts
Get Updates
Featured Articles
Categories
- 2024 Olympics (1)
- 2024 Water Resource Development Act (1)
- Abrasive Blasting (1)
- Advanced coating materials (9)
- advanced coatings (1)
- Advanced Corrosion Control in Oil and Gas Industry (2)
- Advocacy (3)
- AI (2)
- Aircraft (1)
- Alkanization (1)
- AMPP (4)
- AMPP Annual Conference + Expo (4)
- ampp awards (1)
- ampp certification (2)
- Ampp Chapters (1)
- AMPP conference (1)
- AMPP logo (1)
- Ampp Membership (2)
- Ampp Standards (1)
- ampp training (1)
- Amusement parks (4)
- Architectural (1)
- Architectural Coatings (2)
- argonne national laboratory (1)
- Artificial Intelligence (1)
- Asset integrity (11)
- Asset maintenance (3)
- Asset Protection (1)
- awards (3)
- Bim Software (1)
- Biodeterioration of materials (5)
- Biofouling (4)
- Blasting (1)
- Bridges (4)
- career advancement (3)
- career development (2)
- cathodic protection (2)
- Cathodic Protection-CP (16)
- Ceramic epoxies (1)
- Certification (3)
- certification study guide (1)
- Chemical Injection (1)
- CIP (1)
- Civil Engineering (1)
- clean energy (1)
- Coating inspector (2)
- coating inspector job roles (1)
- Coating inspector jobs (2)
- Coating inspector program (2)
- Coatings (17)
- Coatings Application (3)
- coatings certification (1)
- Coatings failures (2)
- Coatings Industry (2)
- coatings inspection (1)
- Coatings inspector (2)
- Coatings measurement and inspection (9)
- coatings project management (1)
- Coatings Systems (1)
- Cold stress (1)
- Concrete (13)
- Concrete corrosion (1)
- concrete cracking (1)
- Conference and Events (2)
- Corrosion (23)
- Corrosion Basics (5)
- corrosion certification (1)
- Corrosion Control (16)
- Corrosion Control and Management (23)
- corrosion engineering (1)
- Corrosion Essentials (20)
- corrosion mitigation (1)
- corrosion of steel (1)
- corrosion policy (1)
- Corrosion Prevention (11)
- corrosion resistance (1)
- corrosion resources (1)
- Corrosion Under Insulation (1)
- cost of corrosion (1)
- Crevice Corrosion (1)
- Cui (1)
- Data Monitoring (1)
- decarbonization (1)
- defense infrastructure (1)
- Department of Defense (4)
- Deposition corrosion (1)
- Dissimilar Metal Corrosion (1)
- Dissolved gases (1)
- DoD (3)
- Education (2)
- EMERG (1)
- Energy industry (9)
- entertainment industry (1)
- Epoxy (3)
- exam preparation (1)
- Fireproofing (1)
- Flexible coatings (2)
- Flint, Michigan (1)
- Fluoropolymer coating (3)
- Forms of Corrosion (4)
- Freshwater salinization (1)
- Galvanic (1)
- Galvanic Corrosion (4)
- General Corrosion (4)
- General Tips (1)
- glossary (1)
- Hand tools (1)
- honoree night (1)
- Industrial Application (3)
- Industrial Safety (2)
- Industry Best Practices (1)
- Industry Standards (1)
- infrastructure (3)
- Infrastructure Durability (1)
- Inspection (1)
- integrity management (1)
- Intergranular Corrosion (1)
- Intumescent Coatings (1)
- key note speaker (1)
- leader (1)
- Machine Learning (2)
- Maintenance (2)
- Maritime Coatings (11)
- Maritime industry (11)
- Master Painters Institute (2)
- material protection (1)
- materials performance (1)
- materials science (1)
- Membership (2)
- Membership Benefits (2)
- Michio Kaku (1)
- Microbiological forms (1)
- Microbiologically influenced corrosion-MIC (11)
- Military (2)
- Mineral constituents (1)
- MnDOT (1)
- MPI (3)
- mpi awards (1)
- mpi champion awards (1)
- mpi training (1)
- MPI Update (1)
- National Defense Authorization Act (1)
- national security (1)
- Navy (1)
- nickel-based alloys (1)
- Non-Destructive Testing (1)
- nuclear (1)
- nuclear Materials (1)
- nuclear reactor technology (1)
- Oil and Gas (2)
- Oil Fields (1)
- Organic matter (1)
- Oxgen (1)
- Paint and Protective coatings (32)
- Paint specification (1)
- pcs certification (1)
- Personal Protective Equipment (3)
- Petrochemical Plant Fireproofing Methods (1)
- Petrochemical Plants (1)
- Pipeline (2)
- Pitting Corrosion (2)
- Pitting Detection (1)
- Polymer-Based Coatings (1)
- Power plant (1)
- Power tools (1)
- PPE (3)
- professional certification (2)
- professional development (1)
- Protective Coatings (6)
- protective coatings industry (1)
- protective coatings specialist (1)
- quality assurance (1)
- radiation-resistant materials (1)
- Real-Time Corrosion Monitoring in Oil Fields (1)
- Rebar Corrosion (2)
- rectifier (1)
- Reliability (1)
- Remote monitoring and drones (4)
- Repaint (1)
- Restoration (1)
- ride maintenance (1)
- Road deicers (1)
- Roads and bridges (1)
- Roller coaster (1)
- Rust (1)
- sacrificial anodes (1)
- Safety (5)
- Safety Standards (2)
- Salt pollution (1)
- Sensors (1)
- service awards (2)
- Ship Coatings (9)
- Shiptanks (1)
- Standards (9)
- Standards Committees (1)
- Steel (8)
- Steel Reinforcement (2)
- Stress Corrosion Cracking (1)
- Structural Steel (1)
- study tips (1)
- Surface Preparation (13)
- Sustainability (1)
- Sustainability and corrosion (7)
- terminology (1)
- Tools (1)
- Turbine (1)
- Types of Corrosion (1)
- Uniform Corrosion (1)
- us army core of engineers (1)
- Wastewater Systems (1)
- Water crisis (1)
- Water pipe corrosion (1)
- Water quality (1)
- Water tank coatings (5)
- Water/treatment infrastructure (20)
- Waterway salinity (1)
- Workforce development (1)
- WRDA (1)