Robots! New Tech Drives Progress in the Coatings & Corrosion Industry
April 7, 2022 •Corrosion CONTROLLED, Corrosion Essentials, MIC
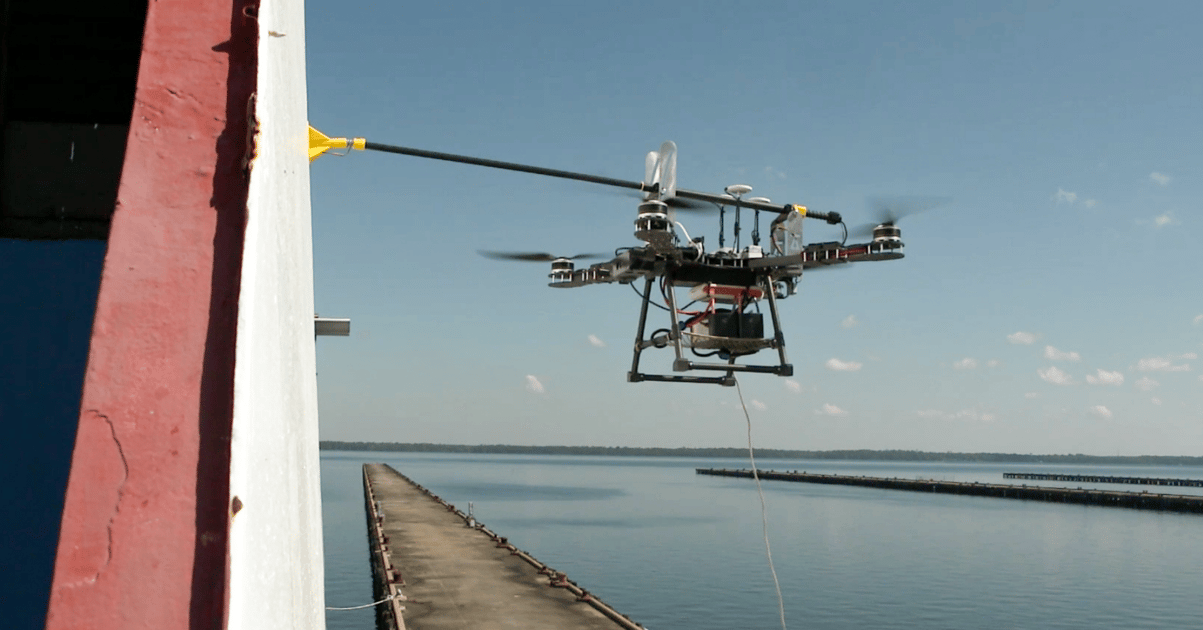
Robots are changing the way we protect assets and infrastructure from the effects of corrosion. Drones, bots, and crawlers can access hazardous or hard-to-reach areas for corrosion inspection, surface preparation, or protective coating application — preventing disastrous failures and keeping people and the environment safe.
New advancements in digitalization, automation, and machine learning are paving the way for further progress at the intersection of robotics and corrosion prevention, while increasing efficiency and safety, and even creating new jobs. A variety of robotic technologies are employed to access remote or hazardous areas, conduct precise and repeatable inspections, or perform tasks that are dull, dirty, or physically demanding.Safety and accuracy are key drivers for the adoption of robotics in the war on corrosion. “Robots don't get cancer and don't breathe oxygen. They are tools capable of precision exceeding that of humans while gathering a plethora of data heretofore unavailable,” says Bob Dahlstrom, CEO of Apellix, an aerial robotics company headquartered in Florida. “We are at an unparalleled time in history where machines and robots are able to do more than ever before and it's only just beginning.”
“The sandblasting industry is dusty, dangerous, and dirty, and involves holding a high-pressure hose for a long period of time,” says Gavin Gooden, Marketing Manager for BlastOne International in Columbus, Ohio. “Using robotics in this industry gets the blaster out of the dust, and doing the work safely from a distance. You use a robot to hold multiple hoses, you can increase the size of the blast hose, and get more work done faster, safer and cleaner.”
What kind of work can robots perform? Here are a few examples:
- Equipped with eight cameras, a custom climbing robot designed by Eddyfi Technologies is used to inspect the Port Mann Bridge, a cable-stayed bridge in British Columbia. This robot’s circular design allows bridge maintenance personnel to perform routine inspections of the bridge’s 288 supporting cables.
- The US Army Corps of Engineers is field-testing a new robotic technology to inspect dams. The Dambot includes a variety of sensors such as high-resolution cameras and Light Detection and Ranging (LiDAR), which can create an extremely detailed model of the entire outlet works system. Typically, an inspection involves a human physically entering the tunnel to take photographs of concerning spots and document anomalies by hand. In contrast, the Dambot allows for precise and repeatable inspections that can be viewed remotely, so that inspectors can do their jobs from a safe distance.
- In the military and aerospace industry, a new robotic technique is being deployed to apply high-temperature coatings to hypersonic flight hardware and missiles. In an enclosed automated spray booth, Aerobotix's robotic assembly line scans, sands, paints, and measures complex components in order to achieve the precision results required in the extreme environment of hypersonic flight.
- At 50 centimeters long, the ecoSUB — a tiny autonomous submarine — allows it to be used in a number of applications, according to the National Oceanography Centre. Paired with other technologies, such as autonomous surface vehicles and satellites, the ecoSUB can monitor infrastructure for issues such as corrosion or potential leaks in pipelines.
Robotics is a fast-growing sector. According to the International Federation of Robotics, global robot density — the number of robots per human worker — is about 126 robots per 10,000 employees, a figure that doubled between 2015 and 2020. Many European and Asian countries are outpacing the adoption of robotics in the United States, says Quinn Holub, Gecko Robotics business development manager. “The U.S. needs to scale rapidly, which will create high demand for people to not only design and build robots, but to maintain and operate them.”
Will robots take our jobs? It’s a concern of many skilled corrosion experts and protective coatings craftworkers. As the field adapts to new tools and technologies available, it may change the desired skill sets and the day-to-day job functions of corrosion/protective coatings professionals.
“Robots don’t take away jobs, they make them more upskilled and better for the operators. We are in a market where manual labor isn’t desired and we have fewer laborers, so using robotics to do 90% of the job means you can get more work done, and pay the operators more, as they are worth it,” says BlastOne International’s Gooden.
Gecko Robotics’ Quinn Holub says there is growing demand for high-quality technical talent: “There are so many excellent and high-paying jobs in the development of robotics and automation that it would be difficult to find a better career option.”“The prediction I want to highlight is that there’s still an enormous amount of work that can only be performed by humans. With state-of-the-art tools, the operator of tomorrow will create unparalleled value to companies across industries,” adds Holub.
To those wishing to work with robotics within the corrosion and protective coatings industry, Gooden says, “Our industry needs people that have experience in this industry with a passion for robotics. Go to college and learn the high-tech stuff about robotics, but do a really dirty summer job of being a blaster and painter to understand real-life Jobsite issues.”
Adds Apellix’s Bob Dahlstrom: “Absolutely go for it. Robots and corrosion are here now and in the future. Learn software programming and learn more about the fascinating world of corrosion. This is important work we are doing and we literally are changing the world.”
Get Updates
Featured Articles
Categories
- 2024 Olympics (1)
- 2024 Water Resource Development Act (1)
- Abrasive Blasting (1)
- Advanced coating materials (9)
- advanced coatings (1)
- Advanced Corrosion Control in Oil and Gas Industry (2)
- Advocacy (3)
- AI (2)
- Aircraft (1)
- Alkanization (1)
- AMPP (4)
- AMPP Annual Conference + Expo (4)
- ampp awards (1)
- ampp certification (2)
- Ampp Chapters (1)
- AMPP conference (1)
- AMPP logo (1)
- Ampp Membership (2)
- Ampp Standards (1)
- ampp training (2)
- Amusement parks (4)
- Architectural (1)
- Architectural Coatings (2)
- argonne national laboratory (1)
- Artificial Intelligence (1)
- Asset integrity (12)
- Asset maintenance (3)
- Asset Protection (1)
- awards (3)
- Bim Software (1)
- Biodeterioration of materials (5)
- Biofouling (4)
- Blasting (1)
- Bridges (4)
- career advancement (3)
- career development (2)
- cathodic protection (2)
- Cathodic Protection-CP (16)
- Ceramic epoxies (1)
- Certification (3)
- certification study guide (1)
- Chemical Injection (1)
- CIP (1)
- Civil Engineering (1)
- clean energy (1)
- Coating inspector (2)
- coating inspector job roles (1)
- Coating inspector jobs (2)
- Coating inspector program (2)
- Coatings (17)
- Coatings Application (3)
- coatings certification (1)
- Coatings failures (2)
- Coatings Industry (2)
- coatings inspection (1)
- Coatings inspector (2)
- Coatings measurement and inspection (9)
- coatings project management (1)
- Coatings Systems (1)
- Cold stress (1)
- Concrete (13)
- Concrete corrosion (1)
- concrete cracking (1)
- Conference and Events (2)
- Corrosion (24)
- Corrosion Basics (5)
- corrosion certification (1)
- Corrosion Control (16)
- Corrosion Control and Management (23)
- Corrosion detection (1)
- corrosion engineering (1)
- Corrosion Essentials (20)
- Corrosion Inspection (1)
- Corrosion Management (1)
- corrosion mitigation (1)
- corrosion of steel (1)
- corrosion policy (1)
- Corrosion Prevention (12)
- corrosion resistance (1)
- corrosion resources (1)
- Corrosion Under Insulation (2)
- cost of corrosion (1)
- Crevice Corrosion (1)
- Cui (2)
- Data Monitoring (1)
- decarbonization (1)
- defense infrastructure (1)
- Department of Defense (4)
- Deposition corrosion (1)
- Dissimilar Metal Corrosion (1)
- Dissolved gases (1)
- DoD (3)
- Education (2)
- EMERG (1)
- Energy industry (9)
- entertainment industry (1)
- Epoxy (3)
- exam preparation (1)
- Fireproofing (1)
- Flexible coatings (2)
- Flint, Michigan (1)
- Fluoropolymer coating (3)
- Forms of Corrosion (4)
- Freshwater salinization (1)
- Galvanic (1)
- Galvanic Corrosion (4)
- General Corrosion (4)
- General Tips (1)
- glossary (1)
- Hand tools (1)
- honoree night (1)
- Industrial Application (3)
- Industrial Safety (3)
- Industry Best Practices (1)
- Industry Standards (1)
- Infrared Thermography (1)
- infrastructure (3)
- Infrastructure Durability (1)
- Inspection (1)
- integrity management (1)
- Intergranular Corrosion (1)
- Intumescent Coatings (1)
- key note speaker (1)
- leader (1)
- Machine Learning (2)
- Maintenance (2)
- Maintenance Best Practices (1)
- Maritime Coatings (11)
- Maritime industry (11)
- Master Painters Institute (2)
- material protection (1)
- materials performance (1)
- materials science (1)
- Membership (2)
- Membership Benefits (2)
- Michio Kaku (1)
- Microbiological forms (1)
- Microbiologically influenced corrosion-MIC (11)
- Military (2)
- Mineral constituents (1)
- MnDOT (1)
- MPI (3)
- mpi awards (1)
- mpi champion awards (1)
- mpi training (1)
- MPI Update (1)
- National Defense Authorization Act (1)
- national security (1)
- Navy (1)
- nickel-based alloys (1)
- Non-Destructive Testing (1)
- nuclear (1)
- nuclear Materials (1)
- nuclear reactor technology (1)
- Oil and Gas (2)
- Oil Fields (1)
- Organic matter (1)
- Oxgen (1)
- Paint and Protective coatings (32)
- Paint specification (1)
- pcs certification (1)
- Personal Protective Equipment (3)
- Petrochemical Plant Fireproofing Methods (1)
- Petrochemical Plants (1)
- Pipeline (2)
- Pitting Corrosion (2)
- Pitting Detection (1)
- Polymer-Based Coatings (1)
- Power plant (1)
- Power tools (1)
- PPE (3)
- professional certification (2)
- professional development (1)
- Protective Coatings (7)
- protective coatings industry (1)
- protective coatings specialist (1)
- quality assurance (1)
- radiation-resistant materials (1)
- Real-Time Corrosion Monitoring in Oil Fields (1)
- Rebar Corrosion (2)
- rectifier (1)
- Reliability (1)
- Remote monitoring and drones (4)
- Repaint (1)
- Restoration (1)
- ride maintenance (1)
- Risk-Based Inspection (1)
- Road deicers (1)
- Roads and bridges (1)
- Roller coaster (1)
- Rust (1)
- sacrificial anodes (1)
- Safety (5)
- Safety Standards (2)
- Salt pollution (1)
- Sensors (1)
- service awards (2)
- Ship Coatings (9)
- Shiptanks (1)
- Standards (9)
- Standards Committees (1)
- Steel (8)
- Steel Reinforcement (2)
- Stress Corrosion Cracking (1)
- Structural Steel (1)
- study tips (1)
- Surface Preparation (13)
- Sustainability (1)
- Sustainability and corrosion (7)
- terminology (1)
- Tools (1)
- Turbine (1)
- Types of Corrosion (1)
- Ultrasonic Testing (1)
- Uniform Corrosion (1)
- us army core of engineers (1)
- Wastewater Systems (1)
- Water crisis (1)
- Water pipe corrosion (1)
- Water quality (1)
- Water tank coatings (5)
- Water/treatment infrastructure (20)
- Waterway salinity (1)
- Workforce development (1)
- WRDA (1)