Building blocks of a successful corrosion management plan
December 14, 2020 •Corrosion CONTROLLED, Corrosion Management
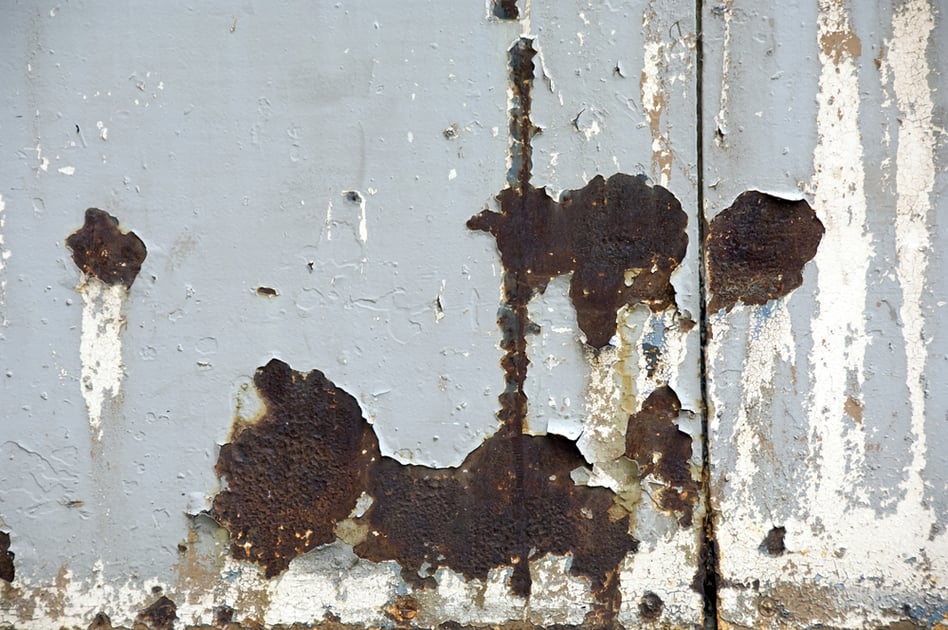
Lowering corrosion-related costs in a company takes more than technology; it requires a change in how corrosion decisions are made within an organization.
Corrosion decisions and practices need to be integrated within an organization’s management system and then be translated into the language of the broader organization with buy-in from all employee levels.
Purpose for Buy-in per Employee Level
Senior Management
• To gain approval to make the change
• To garner sponsorship and resources
Middle Management
• To speed up adoption
• To identify change agents to lead by example
Front-line Employees
• To develop a common understanding of the change
• To ensure widespread adoption and compliance
In other words, success requires a commitment to putting a Corrosion Management System (CMS) or plan into a management context — which means justifying corrosion control actions by business impact.
Corrosion professionals – corrosion, integrity, risk, and maintenance managers – those most likely to be the change agents for how corrosion decisions are made, must be fluent in the language of management systems to facilitate business case communications between all employee levels.
Specifically, to create the foundation required for change to take root and the benefits of a successful corrosion management plan to be realized, the following three steps are critical:
1. Broaden business tool competence
Financial decision-making, risk assessment, and management system knowledge should be in the corrosion professional’s tool kit. Use of financial and risk assessment tools should be a normal and expected activity for evaluating corrosion control expenditures. Whenever relevant and possible, life cycle costing should be considered.
2. Stay away from corrosion technical speak
Communication between those inside and outside of the corrosion profession should be in the language of the external decision-maker (e.g., operations or business manager; regulatory or policy stakeholder) with the goal of business improvement.
3. Include CMS in your overall management system
To institutionalize a CMS, organizations should develop, integrate, and implement corrosion management elements into their overall management systems. This includes, adopting a framework (guidelines) for facilitating its inclusion and defining expectations of standard practice for corrosion management (benchmark).
The preceding is from a global NACE International® IMPACT Study (International Measures of Prevention, Application, & Economics of Corrosion Technologies), published in 2016, that was initiated to examine the current role of corrosion management in industry and government and to establish best practices.
Get assistance with changing how corrosion control decisions are made in your organization. Learn about IMPACT PLUS®, an innovative product developed in response to the NACE IMPACT Study and the challenges faced by industry in putting a CMS into a management context.
FREE DOWNLOADS
White Paper: An Action Plan for Reducing Pipeline Failures, Costs with Corrosion in the Water Sector
Special Report: The Future of Corrosion Control, Insights from the Experts
Get Updates
Featured Articles
Categories
- 2024 Olympics (1)
- 2024 Water Resource Development Act (1)
- Abrasive Blasting (1)
- Advanced coating materials (9)
- advanced coatings (1)
- Advanced Corrosion Control in Oil and Gas Industry (2)
- Advocacy (3)
- AI (2)
- Aircraft (1)
- Alkanization (1)
- AMPP (4)
- AMPP Annual Conference + Expo (4)
- ampp awards (1)
- ampp certification (2)
- Ampp Chapters (1)
- AMPP conference (1)
- AMPP logo (1)
- Ampp Membership (2)
- Ampp Standards (1)
- ampp training (2)
- Amusement parks (4)
- Architectural (1)
- Architectural Coatings (2)
- argonne national laboratory (1)
- Artificial Intelligence (1)
- Asset integrity (12)
- Asset maintenance (3)
- Asset Protection (1)
- awards (3)
- Bim Software (1)
- Biodeterioration of materials (5)
- Biofouling (4)
- Blasting (1)
- Bridges (4)
- career advancement (3)
- career development (2)
- cathodic protection (2)
- Cathodic Protection-CP (16)
- Ceramic epoxies (1)
- Certification (3)
- certification study guide (1)
- Chemical Injection (1)
- CIP (1)
- Civil Engineering (1)
- clean energy (1)
- Coating inspector (2)
- coating inspector job roles (1)
- Coating inspector jobs (2)
- Coating inspector program (2)
- Coatings (17)
- Coatings Application (3)
- coatings certification (1)
- Coatings failures (2)
- Coatings Industry (2)
- coatings inspection (1)
- Coatings inspector (2)
- Coatings measurement and inspection (9)
- coatings project management (1)
- Coatings Systems (1)
- Cold stress (1)
- Concrete (13)
- Concrete corrosion (1)
- concrete cracking (1)
- Conference and Events (2)
- Corrosion (24)
- Corrosion Basics (5)
- corrosion certification (1)
- Corrosion Control (16)
- Corrosion Control and Management (23)
- Corrosion detection (1)
- corrosion engineering (1)
- Corrosion Essentials (20)
- Corrosion Inspection (1)
- Corrosion Management (1)
- corrosion mitigation (1)
- corrosion of steel (1)
- corrosion policy (1)
- Corrosion Prevention (12)
- corrosion resistance (1)
- corrosion resources (1)
- Corrosion Under Insulation (2)
- cost of corrosion (1)
- Crevice Corrosion (1)
- Cui (2)
- Data Monitoring (1)
- decarbonization (1)
- defense infrastructure (1)
- Department of Defense (4)
- Deposition corrosion (1)
- Dissimilar Metal Corrosion (1)
- Dissolved gases (1)
- DoD (3)
- Education (2)
- EMERG (1)
- Energy industry (9)
- entertainment industry (1)
- Epoxy (3)
- exam preparation (1)
- Fireproofing (1)
- Flexible coatings (2)
- Flint, Michigan (1)
- Fluoropolymer coating (3)
- Forms of Corrosion (4)
- Freshwater salinization (1)
- Galvanic (1)
- Galvanic Corrosion (4)
- General Corrosion (4)
- General Tips (1)
- glossary (1)
- Hand tools (1)
- honoree night (1)
- Industrial Application (3)
- Industrial Safety (3)
- Industry Best Practices (1)
- Industry Standards (1)
- Infrared Thermography (1)
- infrastructure (3)
- Infrastructure Durability (1)
- Inspection (1)
- integrity management (1)
- Intergranular Corrosion (1)
- Intumescent Coatings (1)
- key note speaker (1)
- leader (1)
- Machine Learning (2)
- Maintenance (2)
- Maintenance Best Practices (1)
- Maritime Coatings (11)
- Maritime industry (11)
- Master Painters Institute (2)
- material protection (1)
- materials performance (1)
- materials science (1)
- Membership (2)
- Membership Benefits (2)
- Michio Kaku (1)
- Microbiological forms (1)
- Microbiologically influenced corrosion-MIC (11)
- Military (2)
- Mineral constituents (1)
- MnDOT (1)
- MPI (3)
- mpi awards (1)
- mpi champion awards (1)
- mpi training (1)
- MPI Update (1)
- National Defense Authorization Act (1)
- national security (1)
- Navy (1)
- nickel-based alloys (1)
- Non-Destructive Testing (1)
- nuclear (1)
- nuclear Materials (1)
- nuclear reactor technology (1)
- Oil and Gas (2)
- Oil Fields (1)
- Organic matter (1)
- Oxgen (1)
- Paint and Protective coatings (32)
- Paint specification (1)
- pcs certification (1)
- Personal Protective Equipment (3)
- Petrochemical Plant Fireproofing Methods (1)
- Petrochemical Plants (1)
- Pipeline (2)
- Pitting Corrosion (2)
- Pitting Detection (1)
- Polymer-Based Coatings (1)
- Power plant (1)
- Power tools (1)
- PPE (3)
- professional certification (2)
- professional development (1)
- Protective Coatings (7)
- protective coatings industry (1)
- protective coatings specialist (1)
- quality assurance (1)
- radiation-resistant materials (1)
- Real-Time Corrosion Monitoring in Oil Fields (1)
- Rebar Corrosion (2)
- rectifier (1)
- Reliability (1)
- Remote monitoring and drones (4)
- Repaint (1)
- Restoration (1)
- ride maintenance (1)
- Risk-Based Inspection (1)
- Road deicers (1)
- Roads and bridges (1)
- Roller coaster (1)
- Rust (1)
- sacrificial anodes (1)
- Safety (5)
- Safety Standards (2)
- Salt pollution (1)
- Sensors (1)
- service awards (2)
- Ship Coatings (9)
- Shiptanks (1)
- Standards (9)
- Standards Committees (1)
- Steel (8)
- Steel Reinforcement (2)
- Stress Corrosion Cracking (1)
- Structural Steel (1)
- study tips (1)
- Surface Preparation (13)
- Sustainability (1)
- Sustainability and corrosion (7)
- terminology (1)
- Tools (1)
- Turbine (1)
- Types of Corrosion (1)
- Ultrasonic Testing (1)
- Uniform Corrosion (1)
- us army core of engineers (1)
- Wastewater Systems (1)
- Water crisis (1)
- Water pipe corrosion (1)
- Water quality (1)
- Water tank coatings (5)
- Water/treatment infrastructure (20)
- Waterway salinity (1)
- Workforce development (1)
- WRDA (1)