Fun Ride: Coating an Amusement Park
November 10, 2022 •Corrosion CONTROLLED, Corrosion Essentials, Coatings
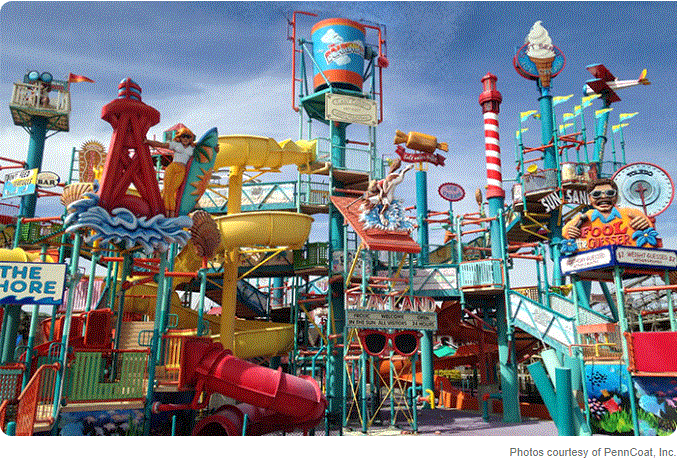
When you think of amusement parks, you may think of a variety of images: roller coasters, Ferris wheels, popcorn, cotton candy, long lines, hot summers, the list probably goes on. But for a coatings contractor, that list may expand to the many, many different substrates with different kinds of coatings.
That is now true for Jeff Neal, the project manager at PennCoat, Inc., a Landisville, Pa.-based coatings contractor.
It started with a cold call. Neal was looking for new clients and was calling local businesses that might be in need of coatings services. He called one of the largest amusement parks in the United States, which wishes to remain unnamed, and Neal was thrilled to land the job.
In fact, he was familiar with the location. “I have been before; it’s a fun place to go,” Neal said. “It’s one of the better amusement parks in the country.” With new coatings, Neal and his crew just might help it be even better!
On a Ride
The job started in March 2015. When Neal and his crew of four arrived on site, they saw what they would be in for. The entire park was more than 100 acres (404,685.6 m²), and the team would be working on rides throughout the park.
“That was one of the biggest issues because what we didn’t account for in the initial bid was how much time it would take to go from one ride to another to another,” Neal said. “Usually when we’re working everything is in walking distance from one another.” But if you think of your own visits to amusement parks and how much time it takes to get from ride to ride, you will understand how that could be a problem.
“Three, four guys walking, carrying all this equipment and paint can become taxing,” Neal said. “We had our company vans inside the park, so that made it a lot better.” The vans decreased the travel time from 20 to 5 minutes, which saved a lot of lost time from the budget.
But distance was not the only big thing about this job. Neal and his crew were not just coating one ride or one substrate. They were applying coating to several different rides, which meant different substrates, different coatings, and different procedures for each ride.
One of the jobs was the waiting deck for one of the roller coasters, which is the overhang that the line of riders winds underneath to stay out of the sun. The job also involved the hand railings that keep the line orderly. The deck was made out of 1,500 square feet (139.4 m²) of T1-11 siding and wood trim. Neal’s crew assessed the job and got to work.
“Because it was a wood substrate, we gently rinsed it with a pressure washer,” Neal said. “We didn’t want to go too strong to prevent splintering.” Then they put down two coats of light gray Sherwin-Williams Duration for a total average thickness of 8 mils (203.2 microns). They rolled the coating onto the siding. “It’s really absorbent, so we would really have to roll it on and work it into the material,” Neal said. “Otherwise you’ll get picture framing where some of the substrate is more absorbent than others, so it would soak in more and look like an uneven finish.”
All of this extra coating meant the job was “eating up more materials than anticipated,” Neal said. “We kept rolling on more until we had a nice even finish.”
For the trim work, they put down a safety red Sherwin-Williams Sher-Cryl coating in two coats for a total average thickness of eight mils (203.2 microns). They covered 700 feet (213.4 m) of trim.
“The trim was more time consuming because it was more detailed work,” Neal said. “We did that work with a brush, and we would have to cut it in and make sure we don’t get any on the T1-11. That was more finesse, so it required couple more hours to complete.”
The total roller coaster deck job took about nine hours. Because the building was about 30-feet (9.1 m) tall, the crew used a boom lift to reach the top.
Then they moved on to a railroad track that was 110-feet (33.5 m) long. The crew had to coat the safety rails and hand rails, which were made of metal.
“It was difficult to get access because the part of track with safety rails was in an area that was on the side of a hill,” Neal said. For that section of the job, the crew wore harnesses and tied off to those safety rails.
To recoat them, first they pressure washed the substrate using a turbo tip pressure washer and took a hand tool wire wheel to “any place that looked like it had excessive rust,” Neal said. “Once it was prepped we painted it.”
They used Carboline Carboguard 690 as a primer and put down one coat in approximately two mils (50.8 microns), then they topped that off with two coats of Carboline Carboguard 134 HG for an average total thickness of eight mils (203.2 microns).
Waterpark Nightmare
Just when Neal and his crew were getting the hang of being inside the park, they saw their next task. It was a giant funhouse waterpark, but it looked anything but fun for a coatings applicator.
“It was made of fiberglass and had wood in it, steel in it. There were so many different substrates and colors involved, there was no efficient way to estimate how many hours we would need to complete the entire project,” Neal said. “It involved a lot of close discussion with the maintenance manager on site — what he wanted us to focus on and what we could turn the other way on.”
The manager understood Neal’s pain. “He referred to the funhouse as a maintenance nightmare because all the water going through it caused peeling paint,” Neal said.
The owner provided all the paint for that job, which involved about 50 different colors and products to use. “It was really challenging to know what his expectations were,” Neal said. “We walked through it and excluded all of the fiberglass. There was a lot of wood paneling on there that needed coating and corrugated steel decking that was starting to show rust.”
The crew used a hand tool on the steel decking, then put down orange and blue Sherwin-Williams Corothane in two coats for a total approximate thickness of eight mils (203.2 microns).
Fun House
Five weeks later all of the work was done, and, despite the challenges, Neal was glad he took the job. “It was really neat to get behind the scenes,” he said. “And it was fun to be able to say you were working at the amusement park.” Neal said his crew did such a great job working with the client that they’re now pricing out projects for next year as well. That means more time spent at the amusement park.
This article was originally published online for CoatingsPro Magazine. Republished with permission.
Want to learn more about Controlling Corrosion in the Amusement Industry? Keep reading to find out more about eCourses, podcasts, webinars, and all the great things happening at AMPP!
See You At IAAPA!
The Global Association of the Attractions Industry (IAAPA)
Interested in learning more about protecting everything from roller coasters and rides to water slides and walkways, from the adverse effects of corrosion? Stop by the AMPP Booth (#3236) at the IAAPA Expo on November 15 - 18, 2022 in Orlando, Florida to explore best practices and some new considerations for the amusements industry. Discover how corrosion must be a consideration at every phase of an amusement ride's lifecycle from design to fabrication to installation to inspections all the way through ongoing maintenance. Read more about the amusement industry at AMPP.
AMPP Salutes Our Veterans!
AMPP’s Workforce Development (WFD) Military Veterans Mentoring Program has been established to assist veterans in achieving a smooth transition into the workforce through proper guidance with AMPP training courses. The mentoring program relies on volunteers who will commit to counseling, supporting, and following the career path of our selected veterans. If you would like to volunteer for this program or for more information, click here.
More Amusement Park Resources
Podcast: NACE at IAAPA Episode 1 with NACE President, Terry Greenfield
In the first episode, NACE International President and Principal Consultant for Consulex, Terry Greenfield, is interviewed from the loud and lively floor of the global attractions industry’s premier event. Greenfield shares insights into how attractions owners can assess and minimize risk, benefits of corrosion management planning, and his thoughts on the outlook for the future of the amusements industry in the area of corrosion prevention and control.
Webinar: Corrosion and the Amusement Park Industry
The introduction of NACE International to the amusement park industry will bring awareness of NACE’s extensive corrosion resources and knowledge, which other industries have relied on for 75 years. NACE will provide information on the basics of corrosion and corrosion control methods and provide case studies that show various infrastructure failures due to corrosion.
Controlling Corrosion in the Amusement Park Industry eCourse
This 90-minute eCourse uses videos to present a range of topics that include the reasons why coatings are applied in the amusement park industry, the basics of corrosion, coating fundamentals, coating selection, conducting coating surveys, and maintenance painting best practices. Save 20% when you purchase 2 or more eCourses. Purchase Now!
NACE and SSPC are now AMPP, The Association for Materials Protection and Performance. Join AMPP Today!
Get Updates
Featured Articles
Categories
- 2024 Olympics (1)
- 2024 Water Resource Development Act (1)
- Abrasive Blasting (1)
- Advanced coating materials (9)
- advanced coatings (1)
- Advanced Corrosion Control in Oil and Gas Industry (2)
- Advocacy (3)
- AI (2)
- Aircraft (1)
- Alkanization (1)
- AMPP (4)
- AMPP Annual Conference + Expo (4)
- ampp awards (1)
- ampp certification (2)
- Ampp Chapters (1)
- AMPP conference (1)
- AMPP logo (1)
- Ampp Membership (2)
- Ampp Standards (1)
- ampp training (2)
- Amusement parks (4)
- Architectural (1)
- Architectural Coatings (2)
- argonne national laboratory (1)
- Artificial Intelligence (1)
- Asset integrity (12)
- Asset maintenance (3)
- Asset Protection (1)
- awards (3)
- Bim Software (1)
- Biodeterioration of materials (5)
- Biofouling (4)
- Blasting (1)
- Bridges (4)
- career advancement (3)
- career development (2)
- cathodic protection (2)
- Cathodic Protection-CP (16)
- Ceramic epoxies (1)
- Certification (3)
- certification study guide (1)
- Chemical Injection (1)
- CIP (1)
- Civil Engineering (1)
- clean energy (1)
- Coating inspector (2)
- coating inspector job roles (1)
- Coating inspector jobs (2)
- Coating inspector program (2)
- Coatings (17)
- Coatings Application (3)
- coatings certification (1)
- Coatings failures (2)
- Coatings Industry (2)
- coatings inspection (1)
- Coatings inspector (2)
- Coatings measurement and inspection (9)
- coatings project management (1)
- Coatings Systems (1)
- Cold stress (1)
- Concrete (13)
- Concrete corrosion (1)
- concrete cracking (1)
- Conference and Events (2)
- Corrosion (24)
- Corrosion Basics (5)
- corrosion certification (1)
- Corrosion Control (16)
- Corrosion Control and Management (23)
- Corrosion detection (1)
- corrosion engineering (1)
- Corrosion Essentials (20)
- Corrosion Inspection (1)
- Corrosion Management (1)
- corrosion mitigation (1)
- corrosion of steel (1)
- corrosion policy (1)
- Corrosion Prevention (12)
- corrosion resistance (1)
- corrosion resources (1)
- Corrosion Under Insulation (2)
- cost of corrosion (1)
- Crevice Corrosion (1)
- Cui (2)
- Data Monitoring (1)
- decarbonization (1)
- defense infrastructure (1)
- Department of Defense (4)
- Deposition corrosion (1)
- Dissimilar Metal Corrosion (1)
- Dissolved gases (1)
- DoD (3)
- Education (2)
- EMERG (1)
- Energy industry (9)
- entertainment industry (1)
- Epoxy (3)
- exam preparation (1)
- Fireproofing (1)
- Flexible coatings (2)
- Flint, Michigan (1)
- Fluoropolymer coating (3)
- Forms of Corrosion (4)
- Freshwater salinization (1)
- Galvanic (1)
- Galvanic Corrosion (4)
- General Corrosion (4)
- General Tips (1)
- glossary (1)
- Hand tools (1)
- honoree night (1)
- Industrial Application (3)
- Industrial Safety (3)
- Industry Best Practices (1)
- Industry Standards (1)
- Infrared Thermography (1)
- infrastructure (3)
- Infrastructure Durability (1)
- Inspection (1)
- integrity management (1)
- Intergranular Corrosion (1)
- Intumescent Coatings (1)
- key note speaker (1)
- leader (1)
- Machine Learning (2)
- Maintenance (2)
- Maintenance Best Practices (1)
- Maritime Coatings (11)
- Maritime industry (11)
- Master Painters Institute (2)
- material protection (1)
- materials performance (1)
- materials science (1)
- Membership (2)
- Membership Benefits (2)
- Michio Kaku (1)
- Microbiological forms (1)
- Microbiologically influenced corrosion-MIC (11)
- Military (2)
- Mineral constituents (1)
- MnDOT (1)
- MPI (3)
- mpi awards (1)
- mpi champion awards (1)
- mpi training (1)
- MPI Update (1)
- National Defense Authorization Act (1)
- national security (1)
- Navy (1)
- nickel-based alloys (1)
- Non-Destructive Testing (1)
- nuclear (1)
- nuclear Materials (1)
- nuclear reactor technology (1)
- Oil and Gas (2)
- Oil Fields (1)
- Organic matter (1)
- Oxgen (1)
- Paint and Protective coatings (32)
- Paint specification (1)
- pcs certification (1)
- Personal Protective Equipment (3)
- Petrochemical Plant Fireproofing Methods (1)
- Petrochemical Plants (1)
- Pipeline (2)
- Pitting Corrosion (2)
- Pitting Detection (1)
- Polymer-Based Coatings (1)
- Power plant (1)
- Power tools (1)
- PPE (3)
- professional certification (2)
- professional development (1)
- Protective Coatings (7)
- protective coatings industry (1)
- protective coatings specialist (1)
- quality assurance (1)
- radiation-resistant materials (1)
- Real-Time Corrosion Monitoring in Oil Fields (1)
- Rebar Corrosion (2)
- rectifier (1)
- Reliability (1)
- Remote monitoring and drones (4)
- Repaint (1)
- Restoration (1)
- ride maintenance (1)
- Risk-Based Inspection (1)
- Road deicers (1)
- Roads and bridges (1)
- Roller coaster (1)
- Rust (1)
- sacrificial anodes (1)
- Safety (5)
- Safety Standards (2)
- Salt pollution (1)
- Sensors (1)
- service awards (2)
- Ship Coatings (9)
- Shiptanks (1)
- Standards (9)
- Standards Committees (1)
- Steel (8)
- Steel Reinforcement (2)
- Stress Corrosion Cracking (1)
- Structural Steel (1)
- study tips (1)
- Surface Preparation (13)
- Sustainability (1)
- Sustainability and corrosion (7)
- terminology (1)
- Tools (1)
- Turbine (1)
- Types of Corrosion (1)
- Ultrasonic Testing (1)
- Uniform Corrosion (1)
- us army core of engineers (1)
- Wastewater Systems (1)
- Water crisis (1)
- Water pipe corrosion (1)
- Water quality (1)
- Water tank coatings (5)
- Water/treatment infrastructure (20)
- Waterway salinity (1)
- Workforce development (1)
- WRDA (1)