Technology offers solution to monitoring MIC damage on jetty pipelines
August 31, 2020 •Corrosion CONTROLLED, Corrosion Essentials, MIC
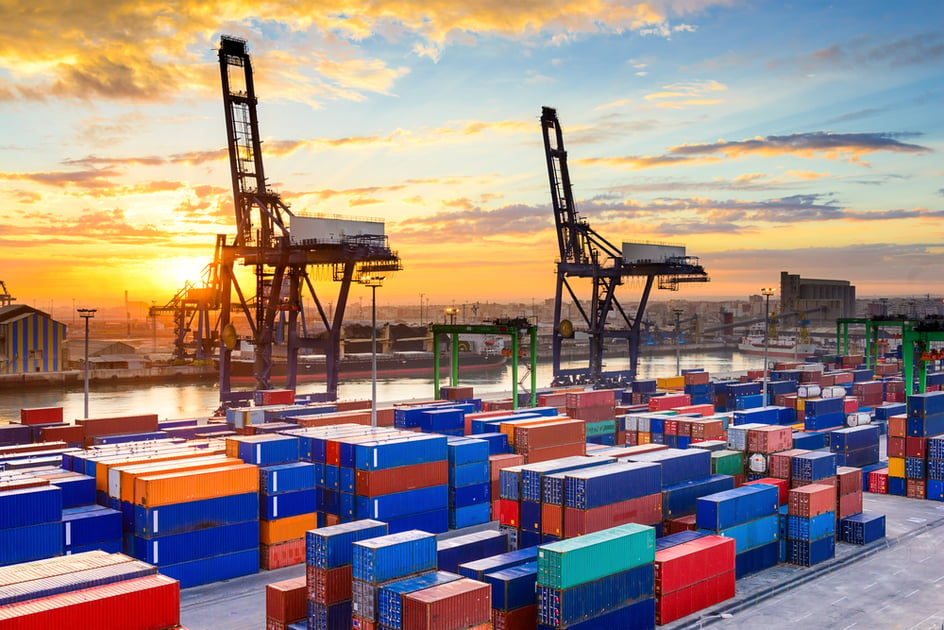
Microbiologically influenced corrosion (MIC) is especially likely in jetty pipelines. Many refineries and oil terminals are located beside major stretches of water—either a sea or river—to provide an easy and cost-effective transportation route for crude oil and feedstock imports and finished product exports. Ships and barges need a certain amount of water depth to be able to safely load and unload product without danger of running aground, so most facilities use jetties to enable the vessel to moor in deeper water. Jetties can often be several hundred meters long with multiple berths, and capable of handling many different products simultaneously. Typically, multiple oil product pipelines running to the ship from the shore are suspended below the jetty deck to allow vehicle access on top.
In most instances it is not cost effective to construct these jetty pipelines from stainless or alloy steel, so carbon steel (CS) is used. The use of CS, however, creates a risk of internal corrosion, particularly when higher sulfur content oils (e.g., fuel oils) are present, fuels contain potentially corrosive additives, and/or the presence and build-up of water allows the accumulation of bacteria that cause microbiologically influenced corrosion (MIC). Since they have intermittent or slow flow rates that allow water to settle in low points, MIC is a cause for concern. If undetected, a leak resulting from corrosion in a jetty pipeline will send hydrocarbons straight into the water course, as well as interrupt jetty operations while the leak is sealed, and necessitate complex oil spill response procedures for clean-up.
To reduce this risk, and to avoid the associated costs and regulatory investigations, most jetty owners regularly inspect the suspended pipelines from a boat or by suspended scaffolding, and often use manual methods such as ultrasound testing to determine wall thickness. In many jurisdictions, this regular inspection activity is mandated by the local environmental regulator. Access to the pipelines by boat is not always possible—during bad weather, for example—which can incur additional costs that operators would rather avoid.
The installation of a permanently mounted ultrasonic wall-thickness monitoring system provides a continuous, effective check of pipeline integrity. Elevated corrosion rates and wall loss are detected without intervention by personnel. As the corrosion mechanisms inside jetty pipelines are normally uniform in nature or restricted to specific, well-known areas, such as MIC in low points on the pipe’s circumference (i.e., the 6 o’clock position), the sensors can be spread uniformly along the line to enable continuous sampling, and target specific high-risk locations.
A permanently mounted, wireless, battery-operated corrosion monitoring system, such as the one developed by Permasense (Horsham, United Kingdom), can be used to transmit ultrasonic wall thickness measurements from multiple sensors mounted on the jetty pipelines to a gateway that can be located in the jetty control room or at a location up to several kilometers away. The permanently mounted wireless sensor is fixed to the pipe surface by integral magnets, and a restraining strap prevents dislocation. Because cables for power supply or data communication are not required, installation, commissioning, and initial data transmission can be achieved within a day. The gateway feeds the sensor data in real time to a computer or server, where they are stored in a database that is accessible from anywhere on an organization’s network. Associated data visualization and analytics software provides corrosion rate calculations and indicates any variations to set parameters as they arise, enabling the end users to focus on issues and locations by exception. The technology makes it feasible for integrity data across multiple locations to be monitored by corrosion management experts at a central location, such as at the company’s headquarters or technical center. Corrosion rate data can be used to forecast, with a high degree of accuracy, when pipelines will need to be repaired or replaced.
Summary
Jetty pipelines at refineries and oil terminals can suffer from internal corrosion, which may cause a leak that would send hydrocarbons directly into the water course. The cost of a leak includes ceasing jetty operations while the leak is repaired and the cost of spill response and clean-up, as well as closer scrutiny from environmental regulators and potential reputational damage. Most jetty owners carry out routine inspections from boat or suspended scaffolding using simple methods such as manual ultrasound inspection. In many jurisdictions, environmental regulations require an enhanced inspection and reporting regime to ensure the probability of a leak is minimized.
Permanently mounted ultrasonic wall thickness monitoring systems provide a means to continuously measure and report corrosion rates without the need to access the location. Data from sensors on the jetty lines (and other facility pipelines or processing units) can be centralized to enable monitoring of all production facilities by a small group of integrity experts, which increases the efficient use of these skilled and increasingly scarce personnel. Visualization and analytics software highlights corrosion events by location with a very high degree of sensitivity so that maintenance activities can be timed and work scope planned accurately and the risk of a hydrocarbon leak is reduced.
Expand your MIC reference library with the title Microbiologically Influenced Corrosion in the Upstream Oil and Gas Industry, authored by Skovhus, Enning, and Lee.
Source: Originally appeared on materialsperformance.com by Jake Davies, Pemasense, Ltd.
FREE DOWNLOADS
White Paper: An Action Plan for Reducing Pipeline Failures, Costs with Corrosion in the Water Sector
Special Report: The Future of Corrosion Control, Insights from the Experts
Get Updates
Featured Articles
Categories
- 2024 Olympics (1)
- 2024 Water Resource Development Act (1)
- Abrasive Blasting (1)
- Advanced coating materials (9)
- advanced coatings (1)
- Advanced Corrosion Control in Oil and Gas Industry (2)
- Advocacy (3)
- AI (2)
- Aircraft (1)
- Alkanization (1)
- AMPP (4)
- AMPP Annual Conference + Expo (4)
- ampp awards (1)
- ampp certification (2)
- Ampp Chapters (1)
- AMPP conference (1)
- AMPP logo (1)
- Ampp Membership (2)
- Ampp Standards (1)
- ampp training (2)
- Amusement parks (4)
- Architectural (1)
- Architectural Coatings (2)
- argonne national laboratory (1)
- Artificial Intelligence (1)
- Asset integrity (12)
- Asset maintenance (3)
- Asset Protection (1)
- awards (3)
- Bim Software (1)
- Biodeterioration of materials (5)
- Biofouling (4)
- Blasting (1)
- Bridges (4)
- career advancement (3)
- career development (2)
- cathodic protection (2)
- Cathodic Protection-CP (16)
- Ceramic epoxies (1)
- Certification (3)
- certification study guide (1)
- Chemical Injection (1)
- CIP (1)
- Civil Engineering (1)
- clean energy (1)
- Coating inspector (2)
- coating inspector job roles (1)
- Coating inspector jobs (2)
- Coating inspector program (2)
- Coatings (17)
- Coatings Application (3)
- coatings certification (1)
- Coatings failures (2)
- Coatings Industry (2)
- coatings inspection (1)
- Coatings inspector (2)
- Coatings measurement and inspection (9)
- coatings project management (1)
- Coatings Systems (1)
- Cold stress (1)
- Concrete (13)
- Concrete corrosion (1)
- concrete cracking (1)
- Conference and Events (2)
- Corrosion (24)
- Corrosion Basics (5)
- corrosion certification (1)
- Corrosion Control (16)
- Corrosion Control and Management (23)
- Corrosion detection (1)
- corrosion engineering (1)
- Corrosion Essentials (20)
- Corrosion Inspection (1)
- Corrosion Management (1)
- corrosion mitigation (1)
- corrosion of steel (1)
- corrosion policy (1)
- Corrosion Prevention (12)
- corrosion resistance (1)
- corrosion resources (1)
- Corrosion Under Insulation (2)
- cost of corrosion (1)
- Crevice Corrosion (1)
- Cui (2)
- Data Monitoring (1)
- decarbonization (1)
- defense infrastructure (1)
- Department of Defense (4)
- Deposition corrosion (1)
- Dissimilar Metal Corrosion (1)
- Dissolved gases (1)
- DoD (3)
- Education (2)
- EMERG (1)
- Energy industry (9)
- entertainment industry (1)
- Epoxy (3)
- exam preparation (1)
- Fireproofing (1)
- Flexible coatings (2)
- Flint, Michigan (1)
- Fluoropolymer coating (3)
- Forms of Corrosion (4)
- Freshwater salinization (1)
- Galvanic (1)
- Galvanic Corrosion (4)
- General Corrosion (4)
- General Tips (1)
- glossary (1)
- Hand tools (1)
- honoree night (1)
- Industrial Application (3)
- Industrial Safety (3)
- Industry Best Practices (1)
- Industry Standards (1)
- Infrared Thermography (1)
- infrastructure (3)
- Infrastructure Durability (1)
- Inspection (1)
- integrity management (1)
- Intergranular Corrosion (1)
- Intumescent Coatings (1)
- key note speaker (1)
- leader (1)
- Machine Learning (2)
- Maintenance (2)
- Maintenance Best Practices (1)
- Maritime Coatings (11)
- Maritime industry (11)
- Master Painters Institute (2)
- material protection (1)
- materials performance (1)
- materials science (1)
- Membership (2)
- Membership Benefits (2)
- Michio Kaku (1)
- Microbiological forms (1)
- Microbiologically influenced corrosion-MIC (11)
- Military (2)
- Mineral constituents (1)
- MnDOT (1)
- MPI (3)
- mpi awards (1)
- mpi champion awards (1)
- mpi training (1)
- MPI Update (1)
- National Defense Authorization Act (1)
- national security (1)
- Navy (1)
- nickel-based alloys (1)
- Non-Destructive Testing (1)
- nuclear (1)
- nuclear Materials (1)
- nuclear reactor technology (1)
- Oil and Gas (2)
- Oil Fields (1)
- Organic matter (1)
- Oxgen (1)
- Paint and Protective coatings (32)
- Paint specification (1)
- pcs certification (1)
- Personal Protective Equipment (3)
- Petrochemical Plant Fireproofing Methods (1)
- Petrochemical Plants (1)
- Pipeline (2)
- Pitting Corrosion (2)
- Pitting Detection (1)
- Polymer-Based Coatings (1)
- Power plant (1)
- Power tools (1)
- PPE (3)
- professional certification (2)
- professional development (1)
- Protective Coatings (7)
- protective coatings industry (1)
- protective coatings specialist (1)
- quality assurance (1)
- radiation-resistant materials (1)
- Real-Time Corrosion Monitoring in Oil Fields (1)
- Rebar Corrosion (2)
- rectifier (1)
- Reliability (1)
- Remote monitoring and drones (4)
- Repaint (1)
- Restoration (1)
- ride maintenance (1)
- Risk-Based Inspection (1)
- Road deicers (1)
- Roads and bridges (1)
- Roller coaster (1)
- Rust (1)
- sacrificial anodes (1)
- Safety (5)
- Safety Standards (2)
- Salt pollution (1)
- Sensors (1)
- service awards (2)
- Ship Coatings (9)
- Shiptanks (1)
- Standards (9)
- Standards Committees (1)
- Steel (8)
- Steel Reinforcement (2)
- Stress Corrosion Cracking (1)
- Structural Steel (1)
- study tips (1)
- Surface Preparation (13)
- Sustainability (1)
- Sustainability and corrosion (7)
- terminology (1)
- Tools (1)
- Turbine (1)
- Types of Corrosion (1)
- Ultrasonic Testing (1)
- Uniform Corrosion (1)
- us army core of engineers (1)
- Wastewater Systems (1)
- Water crisis (1)
- Water pipe corrosion (1)
- Water quality (1)
- Water tank coatings (5)
- Water/treatment infrastructure (20)
- Waterway salinity (1)
- Workforce development (1)
- WRDA (1)