Building Envelope Corrosion Management for Asset Integrity
November 30, 2021 •Corrosion CONTROLLED, Corrosion Management
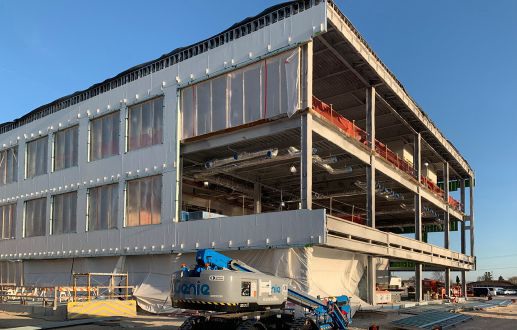
Monitoring the impact of corrosion serves as a critical aspect of ensuring asset integrity. A key method of minimizing corrosion is to employ appropriate corrosion protection technologies. Proactively testing and inspecting building structures can provide a clearer understanding of where to spend limited resources on the maintenance of assets.
Concrete is usually the foundation of a good building, and efficient management regarding the effects of concrete corrosion can extend its life. However, concrete is not the only part of a building that can be threatened by corrosion.
On any building, both the cladding and fasteners holding it in place are exposed to varying degrees of corrosion. Less obvious parts that corrode are the polymers used as sealants, as well as the protective coatings applied to other materials.
When plastics eventually become brittle due to UV exposure, they no longer afford the protection for which they were designed. Some cases have been observed where objects fall through PC canopies and injure people below.
While the most visible degradation effect on polymers is an aesthetic one—a grey-white powdery substance can form on the surface—there can be many other less obvious effects, such as polyvinyl chloride (PVC) guttering and downpipes developing cracks and leaks that could allow water to get inside the building envelope.
Leaky Building Syndrome
A leaky building is one that, as a result of defective design, materials, or construction—usually a combination of all three—allows water to enter through the external building envelope. In turn, this causes decay and damage to the internal structure of the building.
The situation arose from a combination of factors in the late 1990s and early 2000s, when a large number of buildings were constructed using substandard materials. Those problems were compounded with design flaws and insufficient maintenance, leaving the buildings vulnerable to moisture ingress.
There can be many contributing factors to the problem of leaky buildings, including poor-quality metal flashings. These allow water to get behind the façade of a building and corrode materials, including the building framework and cladding fastenings.
Impact on Construction Polymers
Polymers are used extensively in the construction industry, including seals around windows and doors, guttering and downpipes, and corrugated polycarbonate (PC) panels. These are all affected by moisture, heat, and the sun’s ultraviolet (UV) radiation. In addition to structural use, polymers are also often used as sealants over other materials, including concrete.
UV radiation interacts with polymers at the molecular level, where the radiation has enough energy to modify chemical bonds.
Even if stored in a dark cupboard, polymers still interact with their environment. When used as an additive to materials such as concrete and exposed to conditions such as thermal and wet/dry cycles, polymers can leach out chemical binding agents, according to the ACA.
Geography Matters
The geography and climate of a country exacerbate the problem. In the past decade, corrosion on fixings of aluminum composite panels has caused a range of failures in commercial buildings clad with this material, resulting in panels becoming loose and allowing water to enter the building envelope.
However, because it is not seen, building owners are often slow to recognize the problem. Asset owners need to be proactive about checking their buildings and cladding to ensure there is no water ingress.
Inspection reports have shown that leaky buildings are often built with monolithic cladding systems, which provide little or no margin for error if moisture penetrates behind the cladding and into the building envelope. Usually, the untreated, kiln-dried framing timber—once approved by many regulators for use in construction—is particularly susceptible to any moisture ingress.
By the time an asset owner realizes that there is a problem, it is already too late to fix it without rebuilding significant parts of the building’s structure.
Another contributing factor for many years was that developers had no incentive to pay for the best design of their buildings, or the appropriate level of supervision of construction to ensure the buildings were constructed properly. Requiring durability appraisals of building products before a new product is deemed fit for installation in a new building can help.
This requires, however, an independent assessment of the building product, system design, material corrosion resistance, and installation practices. It is also important that testing reflects the geographic environment where the building materials will be used. Thorough appraisals give the construction industry and asset owners confidence that new products have been subjected to a robust technical examination by experts before the product is released into the market. Some failures in the ongoing leaky building crisis have been caused by water ingress behind inadequately designed or installed cladding systems, which resulted in corrosion of hidden metal fixings.
Need a roadmap to corrosion management? Learn about AMPP's IMPACT PLUS.
Source: By the Australasian Corrosion Association; originally appeared on materialsperformance.com
FREE DOWNLOADS
White Paper: An Action Plan for Reducing Pipeline Failures, Costs with Corrosion in the Water Sector
Special Report: The Future of Corrosion Control, Insights from the Experts
Get Updates
Featured Articles
Categories
- 2024 Olympics (1)
- 2024 Water Resource Development Act (1)
- Abrasive Blasting (1)
- Advanced coating materials (9)
- advanced coatings (1)
- Advanced Corrosion Control in Oil and Gas Industry (2)
- Advocacy (3)
- AI (2)
- Aircraft (1)
- Alkanization (1)
- AMPP (4)
- AMPP Annual Conference + Expo (5)
- ampp awards (1)
- ampp certification (2)
- Ampp Chapters (1)
- AMPP conference (1)
- AMPP logo (1)
- Ampp Membership (2)
- Ampp Standards (2)
- ampp training (2)
- Amusement parks (4)
- Architectural (1)
- Architectural Coatings (2)
- argonne national laboratory (1)
- Artificial Intelligence (1)
- Asset integrity (12)
- Asset maintenance (3)
- Asset Protection (1)
- awards (3)
- B2B Marketing (1)
- Bim Software (1)
- Biodeterioration of materials (5)
- Biofouling (4)
- Blasting (1)
- Bridges (4)
- career advancement (3)
- career development (2)
- cathodic protection (2)
- Cathodic Protection-CP (16)
- Ceramic epoxies (1)
- Certification (3)
- certification study guide (1)
- Chemical Injection (1)
- CIP (1)
- Civil Engineering (1)
- clean energy (1)
- Coating inspector (2)
- coating inspector job roles (1)
- Coating inspector jobs (2)
- Coating inspector program (2)
- Coatings (18)
- Coatings Application (3)
- coatings certification (1)
- Coatings failures (2)
- Coatings Industry (2)
- coatings inspection (1)
- Coatings inspector (2)
- Coatings measurement and inspection (9)
- coatings project management (1)
- Coatings Systems (1)
- Cold stress (1)
- Concrete (13)
- Concrete corrosion (1)
- concrete cracking (1)
- Conference and Events (2)
- Corrosion (26)
- Corrosion Basics (5)
- corrosion certification (1)
- Corrosion Control (17)
- Corrosion Control and Management (23)
- Corrosion detection (1)
- corrosion engineering (1)
- Corrosion Essentials (20)
- Corrosion Inspection (1)
- Corrosion Management (1)
- corrosion mitigation (1)
- corrosion of steel (1)
- corrosion policy (1)
- Corrosion Prevention (12)
- corrosion resistance (1)
- corrosion resources (1)
- Corrosion Under Insulation (2)
- cost of corrosion (1)
- Crevice Corrosion (1)
- Cui (2)
- Data Monitoring (1)
- decarbonization (1)
- defense infrastructure (1)
- Department of Defense (4)
- Deposition corrosion (1)
- Dissimilar Metal Corrosion (1)
- Dissolved gases (1)
- DoD (3)
- Education (2)
- EMERG (1)
- Energy industry (9)
- entertainment industry (1)
- Epoxy (3)
- exam preparation (1)
- FBE Application (1)
- FBE Inspection (1)
- Fireproofing (1)
- Flexible coatings (2)
- Flint, Michigan (1)
- Fluoropolymer coating (3)
- Forms of Corrosion (4)
- Freshwater salinization (1)
- Fusion-bonded epoxy (1)
- Galvanic (1)
- Galvanic Corrosion (4)
- General Corrosion (4)
- General Tips (1)
- glossary (1)
- Hand tools (1)
- honoree night (1)
- Industrial Application (3)
- Industrial Safety (3)
- Industry Best Practices (1)
- Industry Standards (2)
- Infrared Thermography (1)
- infrastructure (4)
- Infrastructure Durability (1)
- Inspection (1)
- integrity management (1)
- Intergranular Corrosion (1)
- Intumescent Coatings (1)
- key note speaker (1)
- leader (1)
- Machine Learning (2)
- Maintenance (2)
- Maintenance Best Practices (1)
- Maritime Coatings (11)
- Maritime industry (11)
- Master Painters Institute (2)
- material protection (1)
- materials performance (1)
- materials science (1)
- Membership (2)
- Membership Benefits (2)
- Michio Kaku (1)
- Microbiological forms (1)
- Microbiologically influenced corrosion-MIC (11)
- Military (2)
- Mineral constituents (1)
- MnDOT (1)
- MPI (3)
- mpi awards (1)
- mpi champion awards (1)
- mpi training (1)
- MPI Update (1)
- National Defense Authorization Act (1)
- national security (1)
- Navy (1)
- nickel-based alloys (1)
- Non-Destructive Testing (1)
- nuclear (1)
- nuclear Materials (1)
- nuclear reactor technology (1)
- Oil and Gas (2)
- Oil Fields (1)
- Organic matter (1)
- Oxgen (1)
- Paint and Protective coatings (32)
- Paint specification (1)
- pcs certification (1)
- Personal Protective Equipment (3)
- Petrochemical Plant Fireproofing Methods (1)
- Petrochemical Plants (1)
- Pipeline (2)
- Pitting Corrosion (2)
- Pitting Detection (1)
- Polymer-Based Coatings (1)
- Power plant (1)
- Power tools (1)
- PPE (3)
- Print Advertising (1)
- Print Marketing Strategy (1)
- professional certification (2)
- professional development (1)
- Protective Coatings (7)
- protective coatings industry (1)
- protective coatings specialist (1)
- quality assurance (1)
- radiation-resistant materials (1)
- Real-Time Corrosion Monitoring in Oil Fields (1)
- Rebar Corrosion (2)
- rectifier (1)
- Reliability (1)
- Remote monitoring and drones (4)
- Repaint (1)
- Restoration (1)
- ride maintenance (1)
- Risk-Based Inspection (1)
- Road deicers (1)
- Roads and bridges (1)
- Roller coaster (1)
- Rust (1)
- sacrificial anodes (1)
- Safety (5)
- Safety Standards (3)
- Salt pollution (1)
- Sensors (1)
- service awards (2)
- Ship Coatings (9)
- Shiptanks (1)
- Standards (10)
- Standards Committees (2)
- Steel (8)
- Steel Reinforcement (2)
- Stress Corrosion Cracking (1)
- Structural Steel (1)
- study tips (1)
- Surface Preparation (13)
- Sustainability (1)
- Sustainability and corrosion (7)
- terminology (1)
- Tools (1)
- Turbine (1)
- Types of Corrosion (1)
- Ultrasonic Testing (1)
- Uniform Corrosion (1)
- us army core of engineers (1)
- Wastewater Systems (1)
- Water crisis (1)
- Water pipe corrosion (1)
- Water quality (1)
- Water tank coatings (5)
- Water/treatment infrastructure (20)
- Waterway salinity (1)
- Workforce development (1)
- WRDA (1)