Case Studies Show Galvanic CP Effective on Corroded Reinforced Concrete Structures
February 10, 2022 •Corrosion CONTROLLED, Corrosion Essentials, CP
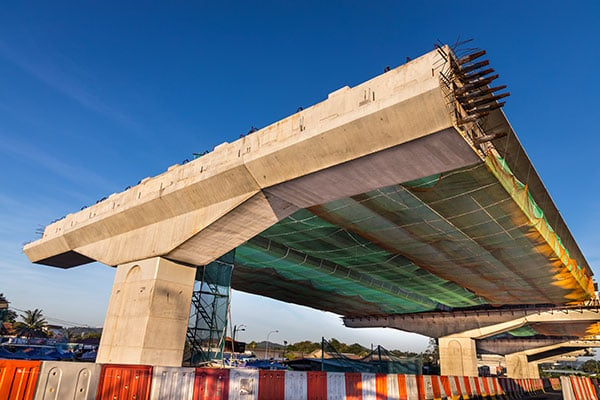
Chloride-induced corrosion of reinforcing steel in concrete is a major problem worldwide. Chlorides can be introduced into concrete through deicing chemicals, seawater, soil, or as contaminants in the concrete mix. This can lead to pitting corrosion and concrete deterioration.
Localized repairs are often performed to address concrete corrosion damage. When a repair is completed, new corrosion sites can form just outside the repaired area and are driven by the residual chloride contamination and the difference in potential between the steel in the chloride- contaminated and chloride-free sections. When incipient anodes form, further repairs will be required. The patch repair process may be repeated several times over the remaining life of the structure.
Galvanic Cathodic Prevention (CP)
Localized corrosion can be addressed by the installation of Type 1 discrete galvanic anodes around the perimeter of repairs (see figure). One of the oldest monitored projects (1999) in which alkali activated, Type 1 anodes were installed was monitored for 20 years. The project’s anodes had a high-purity zinc core cast around steel tie wires to provide a durable zinc-to-steel connection and to prevent dissimilar metal corrosion in the electrical connection between the wires and the reinforcing steel. The zinc cores were cast in high alkalinity mortar with a pH >14 to ensure the anode remains electrochemically active and does not passivate over time. After 20 years, the alkali-activated anodes remained active and continued to produce sufficient galvanic current to meet ISO 126964 cathodic prevention requirements and avoid corrosion initiation in the vicinity of the repairs.
Figure: Alkali-activated galvanic anodes during installation on a bridge pier cap.
Case Studies Help to Verify Galvanic CP's Long-term Performance
Historically, many practitioners believed CP of reinforced concrete structures required an impressed current power supply to provide enough current to protect the reinforcing steel. This is no longer the case as properly designed galvanic encasements using high output, long life, distributed alkali-activated galvanic anodes can provide sufficient CD to polarize the reinforcing steel and meet NACE CP criteria for many years.
Long-term CP requires the galvanic anodes to remain electrochemically active and the electrical connections between the zinc and the steel to remain intact over the desired service life. Laboratory tests are good for verifying short-term performance. Long-term performance of galvanic CP systems, however, is best verified by monitoring systems installed on real structures over time.
Long-term galvanic CP was provided to and then studied on a bridge substructure of the Ohio Department of Transportation (DOT), a bridge deck of the Ontario Ministry of Transportation (MTO), and a tidal/splash zone of the New York State DOT marine columns.
Performance Conclusions
1. Alkali-activated Type 1A discrete galvanic anodes can significantly extend the service life of concrete repairs.
• Anodes installed in the 1990s remained active and provided corrosion prevention (cathodic prevention) CD to reinforcing steel for 20 years. CP current resulted in passivation of the steel over time.
• Examination of anodes removed from the structure verified that there was enough zinc remaining to last 25 to 30 years.
2. Galvanic CP systems utilizing alkali-activated anodes can be designed to remain active and produce sufficient current to meet NACE CP criteria for 20 to 40 years in a range of environments including:
• Bridge substructures in temperate, deicing salt environments
• Bridge decks in temperate, deicing salt environments
• Bridge piles in marine tidal/splash zones
• Bridge columns in tropical, marine environments above the tidal zone
• Florida DOT Marine Substructures (Above Tidal Zone)
See findings specific to each referenced case study.
See AMPP’s Cathodic Protection Program -- courses and certifications for success in the field.
Source: materialperformance.com; article based on a paper by David Whitmore, Vector Corrosion Technologies, Ltd., and Matthew Miltenberger, Vector Corrosion Services, Inc. titled “Galvanic Cathodic Protection of Corroded Reinforced Concrete Structures” presented at CORROSION 2019.
FREE DOWNLOADS
White Paper: An Action Plan for Reducing Pipeline Failures, Costs with Corrosion in the Water Sector
Special Report: The Future of Corrosion Control, Insights from the Experts
Get Updates
Featured Articles
Categories
- 2024 Olympics (1)
- 2024 Water Resource Development Act (1)
- Abrasive Blasting (1)
- Advanced coating materials (9)
- advanced coatings (1)
- Advanced Corrosion Control in Oil and Gas Industry (2)
- Advocacy (3)
- AI (2)
- Aircraft (1)
- Alkanization (1)
- AMPP (4)
- AMPP Annual Conference + Expo (5)
- ampp awards (1)
- ampp certification (2)
- Ampp Chapters (1)
- AMPP conference (1)
- AMPP logo (1)
- Ampp Membership (2)
- Ampp Standards (2)
- ampp training (2)
- Amusement parks (4)
- Architectural (1)
- Architectural Coatings (2)
- argonne national laboratory (1)
- Artificial Intelligence (1)
- Asset integrity (12)
- Asset maintenance (3)
- Asset Protection (1)
- awards (3)
- B2B Marketing (1)
- Bim Software (1)
- Biodeterioration of materials (5)
- Biofouling (4)
- Blasting (1)
- Bridges (4)
- career advancement (3)
- career development (2)
- cathodic protection (2)
- Cathodic Protection-CP (16)
- Ceramic epoxies (1)
- Certification (3)
- certification study guide (1)
- Chemical Injection (1)
- CIP (1)
- Civil Engineering (1)
- clean energy (1)
- Coating inspector (2)
- coating inspector job roles (1)
- Coating inspector jobs (2)
- Coating inspector program (2)
- Coatings (18)
- Coatings Application (3)
- coatings certification (1)
- Coatings failures (2)
- Coatings Industry (2)
- coatings inspection (1)
- Coatings inspector (2)
- Coatings measurement and inspection (9)
- coatings project management (1)
- Coatings Systems (1)
- Cold stress (1)
- Concrete (13)
- Concrete corrosion (1)
- concrete cracking (1)
- Conference and Events (2)
- Corrosion (26)
- Corrosion Basics (5)
- corrosion certification (1)
- Corrosion Control (17)
- Corrosion Control and Management (23)
- Corrosion detection (1)
- corrosion engineering (1)
- Corrosion Essentials (20)
- Corrosion Inspection (1)
- Corrosion Management (1)
- corrosion mitigation (1)
- corrosion of steel (1)
- corrosion policy (1)
- Corrosion Prevention (12)
- corrosion resistance (1)
- corrosion resources (1)
- Corrosion Under Insulation (2)
- cost of corrosion (1)
- Crevice Corrosion (1)
- Cui (2)
- Data Monitoring (1)
- decarbonization (1)
- defense infrastructure (1)
- Department of Defense (4)
- Deposition corrosion (1)
- Dissimilar Metal Corrosion (1)
- Dissolved gases (1)
- DoD (3)
- Education (2)
- EMERG (1)
- Energy industry (9)
- entertainment industry (1)
- Epoxy (3)
- exam preparation (1)
- FBE Application (1)
- FBE Inspection (1)
- Fireproofing (1)
- Flexible coatings (2)
- Flint, Michigan (1)
- Fluoropolymer coating (3)
- Forms of Corrosion (4)
- Freshwater salinization (1)
- Fusion-bonded epoxy (1)
- Galvanic (1)
- Galvanic Corrosion (4)
- General Corrosion (4)
- General Tips (1)
- glossary (1)
- Hand tools (1)
- honoree night (1)
- Industrial Application (3)
- Industrial Safety (3)
- Industry Best Practices (1)
- Industry Standards (2)
- Infrared Thermography (1)
- infrastructure (4)
- Infrastructure Durability (1)
- Inspection (1)
- integrity management (1)
- Intergranular Corrosion (1)
- Intumescent Coatings (1)
- key note speaker (1)
- leader (1)
- Machine Learning (2)
- Maintenance (2)
- Maintenance Best Practices (1)
- Maritime Coatings (11)
- Maritime industry (11)
- Master Painters Institute (2)
- material protection (1)
- materials performance (1)
- materials science (1)
- Membership (2)
- Membership Benefits (2)
- Michio Kaku (1)
- Microbiological forms (1)
- Microbiologically influenced corrosion-MIC (11)
- Military (2)
- Mineral constituents (1)
- MnDOT (1)
- MPI (3)
- mpi awards (1)
- mpi champion awards (1)
- mpi training (1)
- MPI Update (1)
- National Defense Authorization Act (1)
- national security (1)
- Navy (1)
- nickel-based alloys (1)
- Non-Destructive Testing (1)
- nuclear (1)
- nuclear Materials (1)
- nuclear reactor technology (1)
- Oil and Gas (2)
- Oil Fields (1)
- Organic matter (1)
- Oxgen (1)
- Paint and Protective coatings (32)
- Paint specification (1)
- pcs certification (1)
- Personal Protective Equipment (3)
- Petrochemical Plant Fireproofing Methods (1)
- Petrochemical Plants (1)
- Pipeline (2)
- Pitting Corrosion (2)
- Pitting Detection (1)
- Polymer-Based Coatings (1)
- Power plant (1)
- Power tools (1)
- PPE (3)
- Print Advertising (1)
- Print Marketing Strategy (1)
- professional certification (2)
- professional development (1)
- Protective Coatings (7)
- protective coatings industry (1)
- protective coatings specialist (1)
- quality assurance (1)
- radiation-resistant materials (1)
- Real-Time Corrosion Monitoring in Oil Fields (1)
- Rebar Corrosion (2)
- rectifier (1)
- Reliability (1)
- Remote monitoring and drones (4)
- Repaint (1)
- Restoration (1)
- ride maintenance (1)
- Risk-Based Inspection (1)
- Road deicers (1)
- Roads and bridges (1)
- Roller coaster (1)
- Rust (1)
- sacrificial anodes (1)
- Safety (5)
- Safety Standards (3)
- Salt pollution (1)
- Sensors (1)
- service awards (2)
- Ship Coatings (9)
- Shiptanks (1)
- Standards (10)
- Standards Committees (2)
- Steel (8)
- Steel Reinforcement (2)
- Stress Corrosion Cracking (1)
- Structural Steel (1)
- study tips (1)
- Surface Preparation (13)
- Sustainability (1)
- Sustainability and corrosion (7)
- terminology (1)
- Tools (1)
- Turbine (1)
- Types of Corrosion (1)
- Ultrasonic Testing (1)
- Uniform Corrosion (1)
- us army core of engineers (1)
- Wastewater Systems (1)
- Water crisis (1)
- Water pipe corrosion (1)
- Water quality (1)
- Water tank coatings (5)
- Water/treatment infrastructure (20)
- Waterway salinity (1)
- Workforce development (1)
- WRDA (1)