Understanding Corrosion Under Insulation (CUI): Causes, Detection, and Prevention
June 30, 2025 •AMPP
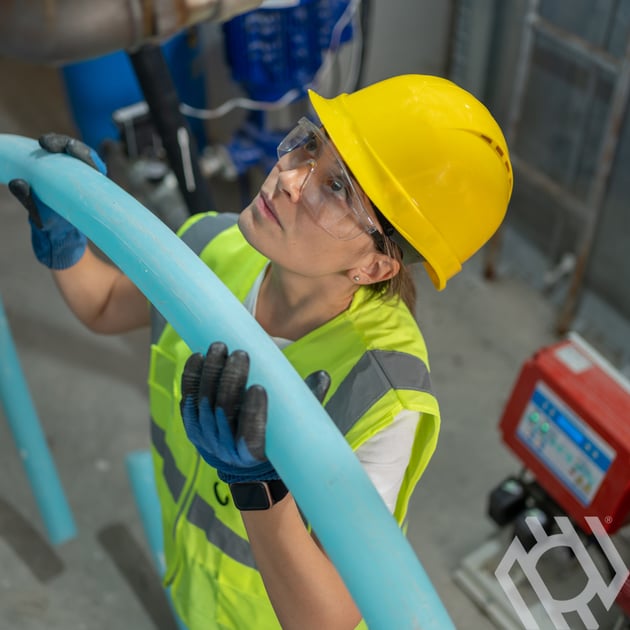
Sometimes, a routine maintenance check turns into a major unplanned shutdown. It may seem insignificant, but even a faint stain on a pipe’s insulation jacket could be hiding an expensive problem: corrosion under insulation (CUI). Insulation stains should be investigated as soon as they’re discovered. CUI is insidious and costly because it often isn’t caught until the damage is done. Deep pitting and corrosion could compromise the pipe’s integrity, and if left unchecked, it could lead to system failures and safety risks.
What is corrosion under insulation?
CUI refers to localized corrosion of piping, vessels, and other equipment beneath thermal insulation. It most often affects carbon steel and stainless steel systems that operate between -12°C (10°F) and 175°C (350°F). Keep an eye on other systems, though, because it can occur outside these temperature ranges.
Because the insulation conceals any degradation or corroded areas, CUI is often only discovered after a significant issue develops. Regular visual inspections and maintenance checks are critically crucial to catching CUI before it compromises safety.
What causes CUI?
There are three main factors to CUI:
- Moisture Intrusion – Water ingress is the number one cause of CUI. Rainwater, process leaks, and condensation all find a way into damaged or poorly sealed insulation systems. Once trapped, that moisture initiates corrosion, especially when contaminants such as chlorides or sulfides are present.
- Temperature Fluctuations – Insulated systems typically undergo thermal cycling, and temperature changes create pressure differences that pull in moisture and trap it under the insulation. These cycles accelerate corrosion, especially in coastal or humid climates.
- Material Selection and Design – Certain insulation materials retain more water or break down faster over time. Jacketing systems can crack, degrade, or fail if they aren’t correctly installed and sealed. Choosing the wrong insulation or failing to seal it can hasten CUI.
How to detect CUI
If you can’t see corrosion under the insulation, how will you know it’s there? Fortunately, there are several methods of detection. Use a combination of techniques and regularly check insulation to catch signs of CUI early.
- Visual Inspection – Look for signs of moisture, staining, or bulging on the outer jacket. These clues point to underlying damage.
- Insulation Removal – Physically remove sections of insulation to inspect high-risk areas. Although it may be costly, it’s better than experiencing an unexpected critical failure.
- Ultrasonic Testing (UT) – This go-to method for measuring wall thickness can also be used to detect corrosion once insulation is removed.
- Radiographic Testing (RT) – Can detect metal loss without removing insulation, but results vary.
- Infrared Thermography – Identifies wet insulation by spotting areas of heat loss or temperature anomalies.
A risk-based inspection will be the most efficient way to focus resources on high-priority areas. Check high-risk areas more thoroughly and frequently.
CUI prevention strategies
Prevention starts long before damage is visible. Here are some best practices for minimizing risk:
- Choose the right coating system. Start with a protective coating rated for immersion or CUI-prone environments. Want to know how to get the best performance from a coating? The Fundamentals of Protective Coatings (C1) course provides you with the knowledge.
- Use an appropriate insulation. Closed-cell or hydrophobic insulation materials resist water absorption. Look for materials that won’t degrade quickly or absorb moisture over time.
- Seal the jacketing effectively. Pay special attention to seams, terminations, and penetrations. Mechanical jacketing should be robust, properly installed, and maintained regularly.
- Plan for inspections. Design systems with removable insulation sections, where possible, and include access points that allow for routine monitoring. Accessibility makes inspections easier and more effective.
- Be proactive with maintenance. Create a CUI inspection plan based on risk zones. Address any jacket damage, reseal problem areas, and regularly test coating integrity.
Boost confidence with CUI training
Combating CUI requires specialized knowledge, vigilance, and the right tools. AMPP has training programs designed to help professionals at every level learn the science behind corrosion and the practical prevention strategies that work in the field. Explore AMPP courses and certification programs to learn more.
Get Updates
Featured Articles
Categories
- 2024 Olympics (1)
- 2024 Water Resource Development Act (1)
- Abrasive Blasting (1)
- Advanced coating materials (9)
- advanced coatings (1)
- Advanced Corrosion Control in Oil and Gas Industry (2)
- Advocacy (3)
- AI (2)
- Aircraft (1)
- Alkanization (1)
- AMPP (4)
- AMPP Annual Conference + Expo (5)
- ampp awards (1)
- ampp certification (2)
- Ampp Chapters (1)
- AMPP conference (1)
- AMPP logo (1)
- Ampp Membership (2)
- Ampp Standards (2)
- ampp training (2)
- Amusement parks (4)
- Architectural (1)
- Architectural Coatings (2)
- argonne national laboratory (1)
- Artificial Intelligence (1)
- Asset integrity (12)
- Asset maintenance (3)
- Asset Protection (1)
- awards (3)
- B2B Marketing (1)
- Bim Software (1)
- Biodeterioration of materials (5)
- Biofouling (4)
- Blasting (1)
- Bridges (4)
- career advancement (3)
- career development (2)
- cathodic protection (2)
- Cathodic Protection-CP (16)
- Ceramic epoxies (1)
- Certification (3)
- certification study guide (1)
- Chemical Injection (1)
- CIP (1)
- Civil Engineering (1)
- clean energy (1)
- Coating inspector (2)
- coating inspector job roles (1)
- Coating inspector jobs (2)
- Coating inspector program (2)
- Coatings (18)
- Coatings Application (3)
- coatings certification (1)
- Coatings failures (2)
- Coatings Industry (2)
- coatings inspection (1)
- Coatings inspector (2)
- Coatings measurement and inspection (9)
- coatings project management (1)
- Coatings Systems (1)
- Cold stress (1)
- Concrete (13)
- Concrete corrosion (1)
- concrete cracking (1)
- Conference and Events (2)
- Corrosion (26)
- Corrosion Basics (5)
- corrosion certification (1)
- Corrosion Control (17)
- Corrosion Control and Management (23)
- Corrosion detection (1)
- corrosion engineering (1)
- Corrosion Essentials (20)
- Corrosion Inspection (1)
- Corrosion Management (1)
- corrosion mitigation (1)
- corrosion of steel (1)
- corrosion policy (1)
- Corrosion Prevention (12)
- corrosion resistance (1)
- corrosion resources (1)
- Corrosion Under Insulation (2)
- cost of corrosion (1)
- Crevice Corrosion (1)
- Cui (2)
- Data Monitoring (1)
- decarbonization (1)
- defense infrastructure (1)
- Department of Defense (4)
- Deposition corrosion (1)
- Dissimilar Metal Corrosion (1)
- Dissolved gases (1)
- DoD (3)
- Education (2)
- EMERG (1)
- Energy industry (9)
- entertainment industry (1)
- Epoxy (3)
- exam preparation (1)
- FBE Application (1)
- FBE Inspection (1)
- Fireproofing (1)
- Flexible coatings (2)
- Flint, Michigan (1)
- Fluoropolymer coating (3)
- Forms of Corrosion (4)
- Freshwater salinization (1)
- Fusion-bonded epoxy (1)
- Galvanic (1)
- Galvanic Corrosion (4)
- General Corrosion (4)
- General Tips (1)
- glossary (1)
- Hand tools (1)
- honoree night (1)
- Industrial Application (3)
- Industrial Safety (3)
- Industry Best Practices (1)
- Industry Standards (2)
- Infrared Thermography (1)
- infrastructure (4)
- Infrastructure Durability (1)
- Inspection (1)
- integrity management (1)
- Intergranular Corrosion (1)
- Intumescent Coatings (1)
- key note speaker (1)
- leader (1)
- Machine Learning (2)
- Maintenance (2)
- Maintenance Best Practices (1)
- Maritime Coatings (11)
- Maritime industry (11)
- Master Painters Institute (2)
- material protection (1)
- materials performance (1)
- materials science (1)
- Membership (2)
- Membership Benefits (2)
- Michio Kaku (1)
- Microbiological forms (1)
- Microbiologically influenced corrosion-MIC (11)
- Military (2)
- Mineral constituents (1)
- MnDOT (1)
- MPI (3)
- mpi awards (1)
- mpi champion awards (1)
- mpi training (1)
- MPI Update (1)
- National Defense Authorization Act (1)
- national security (1)
- Navy (1)
- nickel-based alloys (1)
- Non-Destructive Testing (1)
- nuclear (1)
- nuclear Materials (1)
- nuclear reactor technology (1)
- Oil and Gas (2)
- Oil Fields (1)
- Organic matter (1)
- Oxgen (1)
- Paint and Protective coatings (32)
- Paint specification (1)
- pcs certification (1)
- Personal Protective Equipment (3)
- Petrochemical Plant Fireproofing Methods (1)
- Petrochemical Plants (1)
- Pipeline (2)
- Pitting Corrosion (2)
- Pitting Detection (1)
- Polymer-Based Coatings (1)
- Power plant (1)
- Power tools (1)
- PPE (3)
- Print Advertising (1)
- Print Marketing Strategy (1)
- professional certification (2)
- professional development (1)
- Protective Coatings (7)
- protective coatings industry (1)
- protective coatings specialist (1)
- quality assurance (1)
- radiation-resistant materials (1)
- Real-Time Corrosion Monitoring in Oil Fields (1)
- Rebar Corrosion (2)
- rectifier (1)
- Reliability (1)
- Remote monitoring and drones (4)
- Repaint (1)
- Restoration (1)
- ride maintenance (1)
- Risk-Based Inspection (1)
- Road deicers (1)
- Roads and bridges (1)
- Roller coaster (1)
- Rust (1)
- sacrificial anodes (1)
- Safety (5)
- Safety Standards (3)
- Salt pollution (1)
- Sensors (1)
- service awards (2)
- Ship Coatings (9)
- Shiptanks (1)
- Standards (10)
- Standards Committees (2)
- Steel (8)
- Steel Reinforcement (2)
- Stress Corrosion Cracking (1)
- Structural Steel (1)
- study tips (1)
- Surface Preparation (13)
- Sustainability (1)
- Sustainability and corrosion (7)
- terminology (1)
- Tools (1)
- Turbine (1)
- Types of Corrosion (1)
- Ultrasonic Testing (1)
- Uniform Corrosion (1)
- us army core of engineers (1)
- Wastewater Systems (1)
- Water crisis (1)
- Water pipe corrosion (1)
- Water quality (1)
- Water tank coatings (5)
- Water/treatment infrastructure (20)
- Waterway salinity (1)
- Workforce development (1)
- WRDA (1)