Are Corrosion and Rust the Same Thing?
August 12, 2024 •AMPP
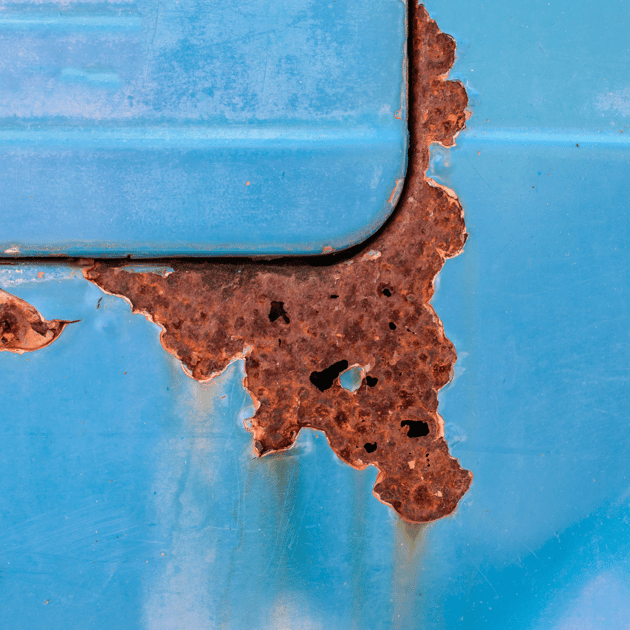
When it comes to metal degradation, the terms "corrosion" and "rust" are often used interchangeably. However, this common misconception can lead to misunderstandings about the nature of these processes and the best ways to combat them. While rust is a familiar sight, especially in everyday items like cars and tools, corrosion encompasses a broader range of material degradation phenomena.
Understanding the distinction between corrosion and rust is crucial for various industries such as construction, automotive, and materials science. Misinterpreting these terms can result in inadequate prevention and maintenance strategies, leading to costly damages and potential safety hazards.
Let’s clarify the differences and similarities between corrosion and rust. While rust is a type of corrosion, not all corrosion is rust. By the end of this discussion, you will have a clearer understanding of these processes and how they impact different materials and industries.
Defining Corrosion
What is Corrosion?
Corrosion is a natural process that results in the gradual destruction of materials, typically metals, through chemical and/or electrochemical reactions with their environment. This process can significantly affect the integrity and functionality of structures and components, leading to failures if not properly managed.
Scientific Definition: Corrosion is the deterioration of a material, usually a metal, as a result of chemical reactions with its surroundings. This often involves oxidation reactions, where the material reacts with oxygen, but can also include other reactions with various environmental substances.
Examples of Corrosion in Different Materials:
- Metals: Iron rusting, aluminum forming an oxide layer, copper developing a green patina.
- Ceramics: Degradation under high-temperature environments, leading to surface wear and weakening.
- Polymers: Environmental stress cracking, UV degradation, and chemical breakdown.
Types of Corrosion
Corrosion manifests in several forms, each with distinct characteristics and mechanisms. Understanding these types helps in identifying and mitigating the specific threats to materials.
- Uniform Corrosion: This type of corrosion occurs evenly across the surface of a material, leading to a uniform thinning of the affected area.
- Example: The even rusting of steel exposed to the atmosphere.
- Galvanic Corrosion: Occurs when two different metals are in electrical contact in the presence of an electrolyte, leading to the more anodic metal corroding faster.
- Example: Corrosion of aluminum when it is in contact with stainless steel in a salty environment.
- Crevice Corrosion: This type of corrosion occurs in confined spaces where the access of the working fluid is limited, such as under gaskets, washers, or deposits.
- Example: Corrosion found under marine hardware where seawater gets trapped.
- Pitting Corrosion: Characterized by the formation of small, localized pits on the surface of a metal, which can penetrate deeply, causing significant damage.
- Example: Pitting on the surface of stainless steel in a chloride-rich environment.
- Intergranular Corrosion: Occurs along the grain boundaries of a metal, often as a result of impurities or precipitates at the boundaries.
- Example: Sensitization of stainless steel, where chromium carbides form at grain boundaries and cause corrosion.
- Stress Corrosion Cracking: Results from the combined effects of tensile stress and a corrosive environment, leading to the formation of cracks.
- Example: Cracking of pipelines or pressure vessels subjected to a corrosive environment and high stress.
Understanding these various forms of corrosion is essential for selecting appropriate materials and protective measures to ensure the longevity and safety of structures and components across industries.
Corrosion vs. Rust
Key Differences
Materials Affected:
Corrosion |
Rust |
This process can affect a wide range of materials, including metals, ceramics, and polymers. Each material reacts differently with environmental factors, leading to various types of degradation. |
Rust is a specific type of corrosion that exclusively affects iron and its alloys, such as steel. This specificity is due to the unique chemical reactions iron undergoes when exposed to moisture and oxygen. |
Chemical Reactions:
Corrosion |
Rust |
Different metals corrode through different chemical reactions. For example, aluminum forms a protective oxide layer when exposed to oxygen, while concrete can crack and disintegrate when exposed to high concentrations of sulfate. These reactions vary based on the material and the environmental conditions. |
Rusting is the specific chemical reaction of iron oxidizing. When iron reacts with oxygen and water, it forms iron oxide (rust), which is typically red-brown in color. This process not only degrades the material but also creates a flaky, brittle surface that can accelerate further corrosion.
|
Appearance and Products:
Corrosion |
Rust |
The appearance of corrosion varies widely depending on the material and type of corrosion. Aluminum corrosion appears as a white, powdery substance; copper corrosion can form a green patina; other metals may show different colors and textures. |
Rust is characterized by its distinctive red-brown color and flaky texture. It forms on the surface of iron and steel, often spreading and deepening as the corrosion process continues. This visual cue is a clear indication of iron oxidation.
|
Similarities
Chemical Reactions with the Environment:
- Both corrosion and rust involve chemical reactions between the material and its environment. These reactions are typically driven by factors such as moisture, oxygen, salts, and other environmental factors. Understanding these reactions helps in developing strategies to prevent or mitigate the effects.
Material Degradation and Structural Failure:
- Both processes lead to the degradation of materials, compromising their strength, appearance, and functionality. If left unchecked, corrosion and rust can cause significant structural failures, resulting in safety hazards, financial losses, and environmental damage. Effective prevention and maintenance strategies are essential to managing these risks.
By recognizing these key differences and similarities, we can better understand how to protect materials from degradation. Whether dealing with the broad phenomenon of corrosion or the specific challenge of rust, implementing appropriate measures is crucial for maintaining the integrity and longevity of structures and components.
Prevention and Control
Preventing Corrosion
Coatings:
Paint |
Galvanization |
Applying protective paint layers creates a barrier between the material and the environment, preventing exposure to corrosive elements such as moisture and oxygen. Specialized anti-corrosion paints are formulated to withstand harsh conditions and extend the lifespan of the material. |
This process involves coating iron or steel with a layer of zinc. The zinc acts as a sacrificial anode, corroding in place of the underlying metal. This method is widely used for outdoor structures like light poles, guardrails, and fences, providing long-lasting protection against corrosion. |
Cathodic Protection:
Impressed Current |
Sacrificial Anodes |
An external power source applies a small electrical current to the metal, counteracting the electrochemical reactions that cause corrosion. This technique is commonly used in pipelines, underground storage tanks, and marine structures. |
More reactive metals, such as magnesium or aluminum, are attached to the protected metal. These anodes corrode instead of the protected metal, extending its life. This method is effective for ships, offshore platforms, and water heaters. |
Material Selection and Design Considerations:
Corrosion-Resistant Materials: |
Design Considerations: |
Selecting materials inherently resistant to corrosion, such as stainless steel, aluminum alloys, and certain plastics, reduces the risk of degradation. These materials are chosen based on their suitability for the specific environmental conditions they will face. |
Thoughtful design can minimize corrosion by avoiding features that trap moisture and by allowing for adequate drainage and ventilation. Reducing the number of crevices and using smooth surfaces can also help prevent localized corrosion. |
Environmental Control:
Humidity Control |
Temperature Control |
Maintaining low humidity levels in storage and operational environments reduces the moisture available for corrosion reactions. Dehumidifiers and climate-controlled storage are effective methods. |
High temperatures can accelerate corrosion rates. Managing temperature through insulation, cooling systems, and environmental control can mitigate this risk.
|
Preventing Rust
Specific Coatings for Iron and Steel:
Rust Inhibitors |
Specialized Paints |
These are chemicals applied to metal surfaces or the surrounding solution to prevent rust formation. They work by forming a protective film that prevents moisture and oxygen from reaching the metal surface. Common rust inhibitors include oil-based products, phosphates, and chromates. |
Paints formulated with rust-inhibiting properties provide an additional layer of protection. These paints often contain rust-preventive additives that enhance their effectiveness.
|
Regular Maintenance and Inspections:
Routine Inspections: |
Maintenance Practices: |
Regularly inspecting metal structures and components for signs of rust and corrosion allows for early detection and intervention. Addressing small areas of rust promptly can prevent more extensive damage. |
Cleaning metal surfaces to remove dirt, salt, and other contaminants reduces the risk of rust formation. Applying protective coatings and rust inhibitors as part of routine maintenance also extends the lifespan of metal assets. |
Use of Stainless Steel and Other Rust-Resistant Materials:
Stainless Steel |
Rust-Resistant Alloys: |
This alloy contains chromium, which forms a passive oxide layer that protects the steel from rusting. Stainless steel is ideal for environments where exposure to moisture and corrosive elements is unavoidable. |
Other alloys, such as weathering steel, are designed to develop a stable rust-like appearance that protects the underlying metal from further corrosion. These materials are used in construction, sculpture, and outdoor applications. |
Implementing these preventive measures helps mitigate the risks of corrosion and rust, ensuring the longevity and safety of metal structures and components. By understanding the specific requirements of each application and choosing appropriate strategies, industries can protect their assets and reduce maintenance costs.
Conclusion
In summary, understanding the distinction between corrosion and rust is crucial for effectively managing material degradation. Corrosion is a broad term encompassing the chemical and electrochemical reactions that degrade various materials, including metals, ceramics, and polymers. Rust, on the other hand, is a specific type of corrosion that exclusively affects iron and its alloys, resulting in the familiar red-brown oxide.
Recognizing and addressing both corrosion and rust is vital across numerous industries, such as construction, automotive, and materials science. Misunderstanding these processes can lead to inadequate protection strategies, resulting in significant financial losses, safety hazards, and environmental damage. Properly identifying the environment, the type of degradation, and implementing targeted preventive measures is essential for maintaining the integrity and longevity of structures and components.
We encourage you to take proactive steps in protecting their assets from corrosion and rust. Implementing preventive measures such as applying protective coatings, using cathodic protection, selecting corrosion-resistant materials, and maintaining environmental control can significantly extend the lifespan of your materials. Regular maintenance and inspections are also critical in identifying and addressing early signs of degradation, preventing minor issues from becoming major problems.
By prioritizing these strategies, you can safeguard your investments, enhance safety, and reduce maintenance costs. Start today by evaluating your current practices and integrating these preventive measures to ensure the durability and reliability of your assets in the face of corrosion and rust.
Get Updates
Featured Articles
Categories
- 2024 Olympics (1)
- 2024 Water Resource Development Act (1)
- Abrasive Blasting (1)
- Advanced coating materials (9)
- advanced coatings (1)
- Advanced Corrosion Control in Oil and Gas Industry (2)
- Advocacy (3)
- AI (2)
- Aircraft (1)
- Alkanization (1)
- AMPP (4)
- AMPP Annual Conference + Expo (5)
- ampp awards (1)
- ampp certification (2)
- Ampp Chapters (1)
- AMPP conference (1)
- AMPP logo (1)
- Ampp Membership (2)
- Ampp Standards (2)
- ampp training (2)
- Amusement parks (4)
- Architectural (1)
- Architectural Coatings (2)
- argonne national laboratory (1)
- Artificial Intelligence (1)
- Asset integrity (12)
- Asset maintenance (3)
- Asset Protection (1)
- awards (3)
- Bim Software (1)
- Biodeterioration of materials (5)
- Biofouling (4)
- Blasting (1)
- Bridges (4)
- career advancement (3)
- career development (2)
- cathodic protection (2)
- Cathodic Protection-CP (16)
- Ceramic epoxies (1)
- Certification (3)
- certification study guide (1)
- Chemical Injection (1)
- CIP (1)
- Civil Engineering (1)
- clean energy (1)
- Coating inspector (2)
- coating inspector job roles (1)
- Coating inspector jobs (2)
- Coating inspector program (2)
- Coatings (18)
- Coatings Application (3)
- coatings certification (1)
- Coatings failures (2)
- Coatings Industry (2)
- coatings inspection (1)
- Coatings inspector (2)
- Coatings measurement and inspection (9)
- coatings project management (1)
- Coatings Systems (1)
- Cold stress (1)
- Concrete (13)
- Concrete corrosion (1)
- concrete cracking (1)
- Conference and Events (2)
- Corrosion (26)
- Corrosion Basics (5)
- corrosion certification (1)
- Corrosion Control (17)
- Corrosion Control and Management (23)
- Corrosion detection (1)
- corrosion engineering (1)
- Corrosion Essentials (20)
- Corrosion Inspection (1)
- Corrosion Management (1)
- corrosion mitigation (1)
- corrosion of steel (1)
- corrosion policy (1)
- Corrosion Prevention (12)
- corrosion resistance (1)
- corrosion resources (1)
- Corrosion Under Insulation (2)
- cost of corrosion (1)
- Crevice Corrosion (1)
- Cui (2)
- Data Monitoring (1)
- decarbonization (1)
- defense infrastructure (1)
- Department of Defense (4)
- Deposition corrosion (1)
- Dissimilar Metal Corrosion (1)
- Dissolved gases (1)
- DoD (3)
- Education (2)
- EMERG (1)
- Energy industry (9)
- entertainment industry (1)
- Epoxy (3)
- exam preparation (1)
- FBE Application (1)
- FBE Inspection (1)
- Fireproofing (1)
- Flexible coatings (2)
- Flint, Michigan (1)
- Fluoropolymer coating (3)
- Forms of Corrosion (4)
- Freshwater salinization (1)
- Fusion-bonded epoxy (1)
- Galvanic (1)
- Galvanic Corrosion (4)
- General Corrosion (4)
- General Tips (1)
- glossary (1)
- Hand tools (1)
- honoree night (1)
- Industrial Application (3)
- Industrial Safety (3)
- Industry Best Practices (1)
- Industry Standards (2)
- Infrared Thermography (1)
- infrastructure (4)
- Infrastructure Durability (1)
- Inspection (1)
- integrity management (1)
- Intergranular Corrosion (1)
- Intumescent Coatings (1)
- key note speaker (1)
- leader (1)
- Machine Learning (2)
- Maintenance (2)
- Maintenance Best Practices (1)
- Maritime Coatings (11)
- Maritime industry (11)
- Master Painters Institute (2)
- material protection (1)
- materials performance (1)
- materials science (1)
- Membership (2)
- Membership Benefits (2)
- Michio Kaku (1)
- Microbiological forms (1)
- Microbiologically influenced corrosion-MIC (11)
- Military (2)
- Mineral constituents (1)
- MnDOT (1)
- MPI (3)
- mpi awards (1)
- mpi champion awards (1)
- mpi training (1)
- MPI Update (1)
- National Defense Authorization Act (1)
- national security (1)
- Navy (1)
- nickel-based alloys (1)
- Non-Destructive Testing (1)
- nuclear (1)
- nuclear Materials (1)
- nuclear reactor technology (1)
- Oil and Gas (2)
- Oil Fields (1)
- Organic matter (1)
- Oxgen (1)
- Paint and Protective coatings (32)
- Paint specification (1)
- pcs certification (1)
- Personal Protective Equipment (3)
- Petrochemical Plant Fireproofing Methods (1)
- Petrochemical Plants (1)
- Pipeline (2)
- Pitting Corrosion (2)
- Pitting Detection (1)
- Polymer-Based Coatings (1)
- Power plant (1)
- Power tools (1)
- PPE (3)
- professional certification (2)
- professional development (1)
- Protective Coatings (7)
- protective coatings industry (1)
- protective coatings specialist (1)
- quality assurance (1)
- radiation-resistant materials (1)
- Real-Time Corrosion Monitoring in Oil Fields (1)
- Rebar Corrosion (2)
- rectifier (1)
- Reliability (1)
- Remote monitoring and drones (4)
- Repaint (1)
- Restoration (1)
- ride maintenance (1)
- Risk-Based Inspection (1)
- Road deicers (1)
- Roads and bridges (1)
- Roller coaster (1)
- Rust (1)
- sacrificial anodes (1)
- Safety (5)
- Safety Standards (3)
- Salt pollution (1)
- Sensors (1)
- service awards (2)
- Ship Coatings (9)
- Shiptanks (1)
- Standards (10)
- Standards Committees (2)
- Steel (8)
- Steel Reinforcement (2)
- Stress Corrosion Cracking (1)
- Structural Steel (1)
- study tips (1)
- Surface Preparation (13)
- Sustainability (1)
- Sustainability and corrosion (7)
- terminology (1)
- Tools (1)
- Turbine (1)
- Types of Corrosion (1)
- Ultrasonic Testing (1)
- Uniform Corrosion (1)
- us army core of engineers (1)
- Wastewater Systems (1)
- Water crisis (1)
- Water pipe corrosion (1)
- Water quality (1)
- Water tank coatings (5)
- Water/treatment infrastructure (20)
- Waterway salinity (1)
- Workforce development (1)
- WRDA (1)