Cost-effective cathodic protection for water infrastructure
June 3, 2020 •Corrosion CONTROLLED, Corrosion Essentials, CP
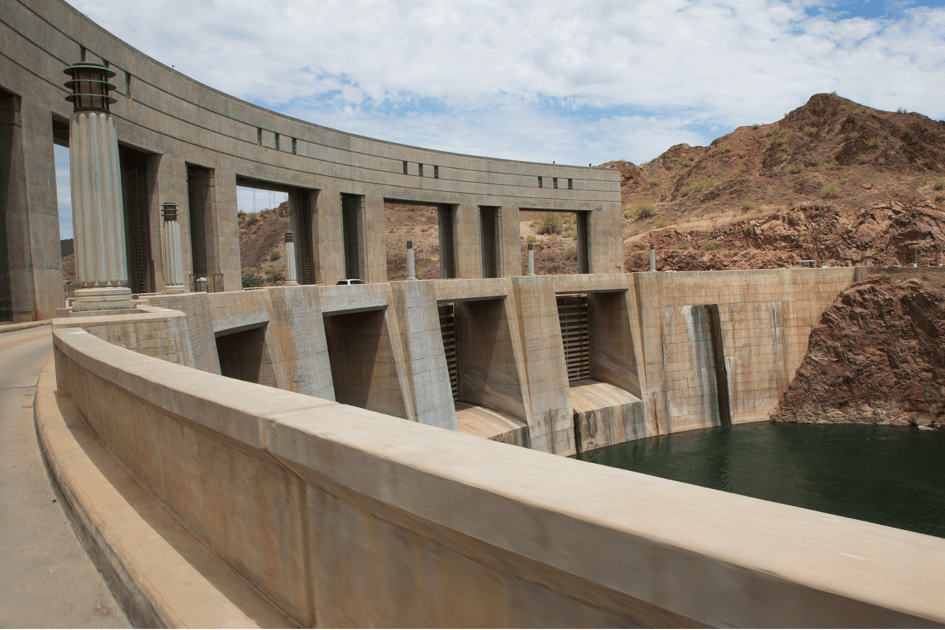
The U.S. Bureau of Reclamation (Denver, Colorado, USA) is best known for constructing U.S. dams, power plants, and canals in 17 western states. These structures have steel equipment, such as hydraulic gates, that are vital for the manipulation of water sources.
Corrosion protection of these gates helps to ensure the equipment provides a long, reliable service life, according to the Reclamation’s Technical Service Center. The service environment for these gates often includes alternating immersion and atmospheric exposure, considered moderate to severe for most structures. For this equipment, coatings are the primary method of corrosion protection; however, cathodic protection (CP) provides a secondary method of protection to areas with coating damage or poor coverage. Reclamation notes that some estimates suggest the addition of CP can delay recoating until as much as 20% of the coating is deteriorated, which potentially doubles the coating’s service life.
Parker Dam, owned and operated by Reclamation, is located on the Colorado River at Lake Havasu, which is the reservoir behind the dam and the water source for the Colorado River Aqueduct and the Central Arizona Project Aqueduct. The dam has four penstock gates that allow the intake structures to the power plant to be closed during unit outages. The fixed wheel gates, 35-ft (11-m) high by 22-ft (7-m) wide with riveted construction, are exposed to a freshwater environment. The upstream side is a watertight skin plate, and the downstream side reveals the gate’s structural members. The gates are stored in pockets in the forebay at the entrance to the penstocks. The water surface elevation is relatively consistent, with the lower three quarters of the gates continuously immersed during storage. When the intake is closed for maintenance, the gates are fully immersed.
NACE members at the Reclamation’s Technical Service Center conducted a case study on these gates to determine the cost effectiveness of using CP in conjunction with a protective epoxy coating. It compared the service life of the coating when paired with either a galvanic anode CP (GACP) system or an impressed current CP (ICCP) system, or when it is not paired with any CP system. The approach was to determine the point when cost savings due to a longer recoating interval surpassed the cost of the CP system. The findings were published in a paper presented at CORROSION 2018.*
It is generally accepted that a properly designed and implemented CP system extends the service life of a coating, as well as the underlying steel structure. For the penstock gates, however, variations in the coating quality on individual gates, service environment, maintenance, and other factors make it hard to quantify and generalize any observations of service life extension. As a result, data-based corrosion management has become important for budget planning as the cost of corrosion control for water infrastructure continues to climb.
Both GACP and ICCP are used on hydraulic steel structures. To determine the feasibility of CP for a particular hydraulic gate, several factors must be considered. First, the structure must be in water for the CP system to work. In addition, the effectiveness of CP can be greatly reduced in areas of fast-flowing water. Also, the geometry, load-bearing capabilities, and clearance of the gate and surrounding structure must be able to accommodate the CP equipment.
A typical GACP system for gates in freshwater immersion service consists of direct hull-mounted magnesium hull-style anodes, with a thick dielectric coating on the sides closest to the gate to prevent over-polarization and cathodic disbondment of the coating. These are attached via welding or a weld stud mechanical connection, and a small area of the gate coating is removed before installation and repaired after installation. Anodes are attached only in areas of the gate that are submerged.
Designs for ICCP systems for gates in freshwater immersion service often fall into three categories—hull-mounted anodes, through-mounted anodes, and remotely located anodes—and many configurations are possible. Although this case study utilized an appropriate anode style, it did not evaluate the cost effectiveness between various design configurations. As with GACP systems, only the submerged portions of the gate are protected. ICCP requires connection to a rectifier from the electric grid or other power source. For the study, a life-cycle cost analysis spreadsheet tool (LCCAST), previously used for comparing life-cycle costs of protective coatings, was modified to calculate the cost of incorporating a CP system. The tool utilizes a cost-effectiveness framework, but instead of determining if an alternative is cost effective, it determines when the alternative becomes cost effective (i.e., the payback period). The variables for the experiments in this study combined experience with actual structures, as well as published estimated service life values.
IMAGE: Penstock gates at Parker Dam located on the Colorado River at Lake Havasu.
Three alternatives were evaluated for this case study:
Alternative 1 (A1) an epoxy recoating of the four gates without CP;
Alternative 2 (A2) the same epoxy recoating specified in A1 paired with a GACP system; and
Alternative 3 (A3) the same epoxy recoating specified in A1 paired with an ICCP system.
Each CP system design considered actual gate conditions, including existing corrosion pits, rivets, and other coating defects that require protection.
The baseline alternative, A1, assumed that epoxy coatings applied to penstock gates in a freshwater environment with no supplemental CP have an estimated service life of 25 years before a full recoating is required. The recoating cost incurred for existing structures included all costs associated with removing an existing coating system and applying a new system. It also included all maintenance activities to inspect or repair the coating system from the date the new system is applied until the day it is removed in full.
For A2, a GACP system with a 20-year service life using standard potential magnesium anodes with a plastisol coating was designed for the gates. Installation would include removal of a small area of existing coating for each anode, surface preparation, welding of the anodes to the structure, additional surface preparation, and recoating of the exposed metal.
An ICCP system designed for A3 featured a 40-year service life using high-silicon, cast-iron anodes on a sled that could be lowered into the forebay and a rectifier located on the deck near the gates. The anodes and sled would be replaced every 20 years. Installation would require placement of the anode sled and running of cable through conduit from the anodes and gates to the power source. The anodes and gates would be connected to the rectifier through a junction box with shunts and variable resistors, and the rectifier connected to grid power.
For the LCCAST evaluation, the inputs required to accurately estimate life-cycle costs included all costs associated with each alternative, as well as the occurrence, duration, and priority of each cost. All cost items were distributed into three major categories: initial capital costs, periodic maintenance costs, and annual maintenance costs. The base year of analysis in LCCAST can be selected by the user. For this study, all cost items were indexed to 2016.
The results showed that each CP system reached its payback period after a relatively short duration of the coating’s extended service life.
• The ICCP system in this case study becomes cost effective after five years of additional coating service life (i.e., once it extends the coating service life from 25 to 30 years).
• The GACP system becomes cost effective after seven years of additional coating service life.
Therefore, the CP system investment cost is recouped quickly by the additional service life achieved by the coating system.
This analysis demonstrated the utility of the approach and provided a basis for subsequent experiments. In a second experiment, LCCAST results were determined for protecting a single gate vs. all four gates, and the impact of cost differences for the two CP system types were demonstrated. It showed that:
• ICCP has notable economies of scale (i.e., the payback period decreases as the surface area being protected increases), and
• the low initial cost of GACP makes it economically appealing for smaller surface areas.
A third experiment did runs of the LCCAST with coating baseline life cycles of 15 and 35 years. Results showed that:
• the CP system payback period decreases with a shorter coating system life cycle; and
• for coating systems with longer life cycles, the CP system must achieve a significantly greater extension in service life to become cost effective.
These studies concluded that a CP system was cost effective for all experiments conducted, with results demonstrating cost effectiveness after extending the coating service life by 15 to 30%.
*Additional details of referenced study can be found in paper titled CORROSION 2018 paper no.11230 - “Evaluating Cost-Effectiveness of Water Infrastructure Corrosion Control Methods” by D. Torrey, T. Gaston, and B.J.E. Merten.
To find and/or validate certified Cathodic Protection professionals for your next project use NACE International Institute’s Certificate Registry.
Source: Article originally appeared in NACE’s Infrastructure Insights, Summer 2019.
FREE DOWNLOADS
White Paper: An Action Plan for Reducing Pipeline Failures, Costs with Corrosion in the Water Sector
Special Report: The Future of Corrosion Control, Insights from the Experts
Get Updates
Featured Articles
Categories
- 2024 Olympics (1)
- 2024 Water Resource Development Act (1)
- Abrasive Blasting (1)
- Advanced coating materials (9)
- advanced coatings (1)
- Advanced Corrosion Control in Oil and Gas Industry (2)
- Advocacy (3)
- AI (2)
- Aircraft (1)
- Alkanization (1)
- AMPP (4)
- AMPP Annual Conference + Expo (5)
- ampp awards (1)
- ampp certification (2)
- Ampp Chapters (1)
- AMPP conference (1)
- AMPP logo (1)
- Ampp Membership (2)
- Ampp Standards (2)
- ampp training (2)
- Amusement parks (4)
- Architectural (1)
- Architectural Coatings (2)
- argonne national laboratory (1)
- Artificial Intelligence (1)
- Asset integrity (12)
- Asset maintenance (3)
- Asset Protection (1)
- awards (3)
- B2B Marketing (1)
- Bim Software (1)
- Biodeterioration of materials (5)
- Biofouling (4)
- Blasting (1)
- Bridges (4)
- career advancement (3)
- career development (2)
- cathodic protection (2)
- Cathodic Protection-CP (16)
- Ceramic epoxies (1)
- Certification (3)
- certification study guide (1)
- Chemical Injection (1)
- CIP (1)
- Civil Engineering (1)
- clean energy (1)
- Coating inspector (2)
- coating inspector job roles (1)
- Coating inspector jobs (2)
- Coating inspector program (2)
- Coatings (18)
- Coatings Application (3)
- coatings certification (1)
- Coatings failures (2)
- Coatings Industry (2)
- coatings inspection (1)
- Coatings inspector (2)
- Coatings measurement and inspection (9)
- coatings project management (1)
- Coatings Systems (1)
- Cold stress (1)
- Concrete (13)
- Concrete corrosion (1)
- concrete cracking (1)
- Conference and Events (2)
- Corrosion (26)
- Corrosion Basics (5)
- corrosion certification (1)
- Corrosion Control (17)
- Corrosion Control and Management (23)
- Corrosion detection (1)
- corrosion engineering (1)
- Corrosion Essentials (20)
- Corrosion Inspection (1)
- Corrosion Management (1)
- corrosion mitigation (1)
- corrosion of steel (1)
- corrosion policy (1)
- Corrosion Prevention (12)
- corrosion resistance (1)
- corrosion resources (1)
- Corrosion Under Insulation (2)
- cost of corrosion (1)
- Crevice Corrosion (1)
- Cui (2)
- Data Monitoring (1)
- decarbonization (1)
- defense infrastructure (1)
- Department of Defense (4)
- Deposition corrosion (1)
- Dissimilar Metal Corrosion (1)
- Dissolved gases (1)
- DoD (3)
- Education (2)
- EMERG (1)
- Energy industry (9)
- entertainment industry (1)
- Epoxy (3)
- exam preparation (1)
- FBE Application (1)
- FBE Inspection (1)
- Fireproofing (1)
- Flexible coatings (2)
- Flint, Michigan (1)
- Fluoropolymer coating (3)
- Forms of Corrosion (4)
- Freshwater salinization (1)
- Fusion-bonded epoxy (1)
- Galvanic (1)
- Galvanic Corrosion (4)
- General Corrosion (4)
- General Tips (1)
- glossary (1)
- Hand tools (1)
- honoree night (1)
- Industrial Application (3)
- Industrial Safety (3)
- Industry Best Practices (1)
- Industry Standards (2)
- Infrared Thermography (1)
- infrastructure (4)
- Infrastructure Durability (1)
- Inspection (1)
- integrity management (1)
- Intergranular Corrosion (1)
- Intumescent Coatings (1)
- key note speaker (1)
- leader (1)
- Machine Learning (2)
- Maintenance (2)
- Maintenance Best Practices (1)
- Maritime Coatings (11)
- Maritime industry (11)
- Master Painters Institute (2)
- material protection (1)
- materials performance (1)
- materials science (1)
- Membership (2)
- Membership Benefits (2)
- Michio Kaku (1)
- Microbiological forms (1)
- Microbiologically influenced corrosion-MIC (11)
- Military (2)
- Mineral constituents (1)
- MnDOT (1)
- MPI (3)
- mpi awards (1)
- mpi champion awards (1)
- mpi training (1)
- MPI Update (1)
- National Defense Authorization Act (1)
- national security (1)
- Navy (1)
- nickel-based alloys (1)
- Non-Destructive Testing (1)
- nuclear (1)
- nuclear Materials (1)
- nuclear reactor technology (1)
- Oil and Gas (2)
- Oil Fields (1)
- Organic matter (1)
- Oxgen (1)
- Paint and Protective coatings (32)
- Paint specification (1)
- pcs certification (1)
- Personal Protective Equipment (3)
- Petrochemical Plant Fireproofing Methods (1)
- Petrochemical Plants (1)
- Pipeline (2)
- Pitting Corrosion (2)
- Pitting Detection (1)
- Polymer-Based Coatings (1)
- Power plant (1)
- Power tools (1)
- PPE (3)
- Print Advertising (1)
- Print Marketing Strategy (1)
- professional certification (2)
- professional development (1)
- Protective Coatings (7)
- protective coatings industry (1)
- protective coatings specialist (1)
- quality assurance (1)
- radiation-resistant materials (1)
- Real-Time Corrosion Monitoring in Oil Fields (1)
- Rebar Corrosion (2)
- rectifier (1)
- Reliability (1)
- Remote monitoring and drones (4)
- Repaint (1)
- Restoration (1)
- ride maintenance (1)
- Risk-Based Inspection (1)
- Road deicers (1)
- Roads and bridges (1)
- Roller coaster (1)
- Rust (1)
- sacrificial anodes (1)
- Safety (5)
- Safety Standards (3)
- Salt pollution (1)
- Sensors (1)
- service awards (2)
- Ship Coatings (9)
- Shiptanks (1)
- Standards (10)
- Standards Committees (2)
- Steel (8)
- Steel Reinforcement (2)
- Stress Corrosion Cracking (1)
- Structural Steel (1)
- study tips (1)
- Surface Preparation (13)
- Sustainability (1)
- Sustainability and corrosion (7)
- terminology (1)
- Tools (1)
- Turbine (1)
- Types of Corrosion (1)
- Ultrasonic Testing (1)
- Uniform Corrosion (1)
- us army core of engineers (1)
- Wastewater Systems (1)
- Water crisis (1)
- Water pipe corrosion (1)
- Water quality (1)
- Water tank coatings (5)
- Water/treatment infrastructure (20)
- Waterway salinity (1)
- Workforce development (1)
- WRDA (1)