How Hybrid Nanocoating System Extends Coating Life
June 7, 2021 •Corrosion CONTROLLED, Advanced Materials
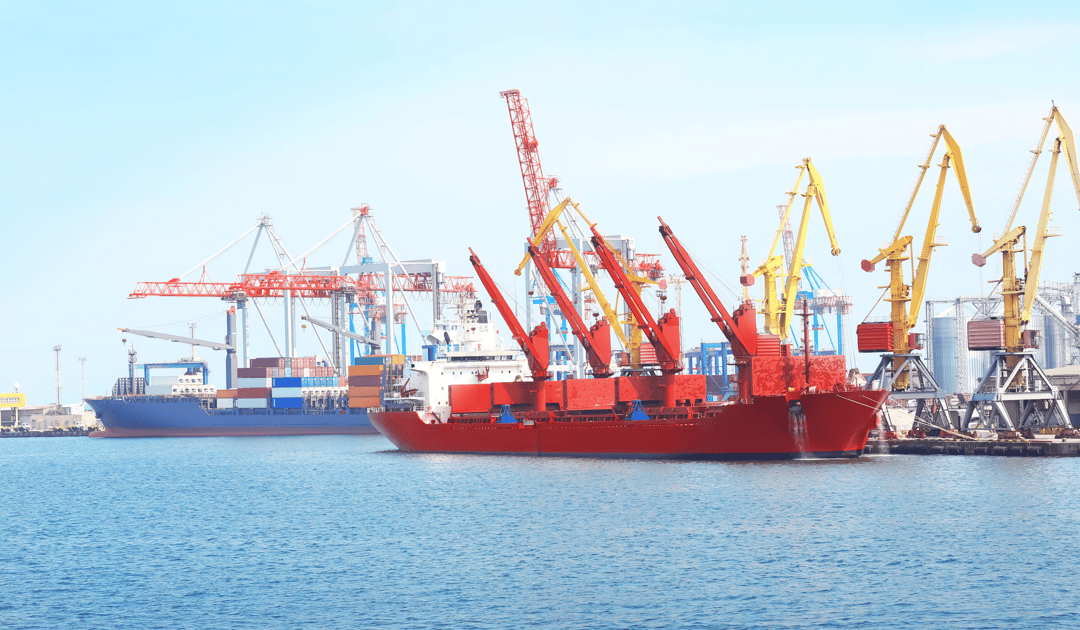
A hybrid nanocoating system is using three-dimensional (3-D) nano-structured polymers to produce high crosslink density and protect against corrosion; restore existing color and gloss; and provide strong resistance to ultraviolet (UV) degradation, extreme weathering, and chemical attack. Based on a proprietary chemical formula from Nanovere Technologies, LLC (Brighton, Michigan, USA) the system also resists abrasions, chipping, marring, gouging, scratching, and more.
Applied over conventional paints, Nano-Clear “reduces maintenance frequency, recoating cycles, chemical costs with mixing, repair, and cleaning, and the volume of coating material required. Thus, it reduces expenses,” says Thomas Choate, CEO of the technology company. He further adds that studies have found the product to reduce the surface maintenance of paint by 50%.
Limitations of Conventional Coatings
According to the company, UV rays can cause conventional coatings to quickly degrade, leading to underlying corrosion. “Surface scratching exposes the steel to the environment, thereby causing corrosion,” Choate explains. “Chemical attack on conventional steel paints also cause underlying corrosion issues.”
The company notes that painted surfaces exposed to the environment are highly susceptible to damage from factors including water, humidity, salts, ice, heat, dirt, smog, oils, chemical attack, acid precipitation, and UV rays. This damage is of particular concern with assets, such as transoceanic ships, chemical tank cars, offshore oil rigs, heavy duty machinery, and fleet vehicles since these assets are regularly exposed to harsh environments.
According to Choate, many of these industrial assets historically have used one- or two-component pigmented epoxy and polyurethane coatings for metal protection. However, while epoxies have strong adhesion to metal with good initial corrosion resistance and surface hardness, Choate says they can fall short in areas of long-term UV and chemical resistance due to poor crosslink density within the linear chain molecules.
Benefits of Nanocoatings
By contrast, the single component, humidity cured, polyurethane/polyurea hybrid nanocoating penetrates into the pores and voids of new or highly oxidized paint systems to form a hard, protective topcoat surface. As a solvent-based system with low volatile organic compound values of 150 g/L, the topcoat also features repellency properties for oil and dirt, water and ice, brake dust, algae, and other environmental and biological contaminants.
Choate says his company is the first group to utilize 3-D nanostructured polymers within an industrial coating system to achieve a high crosslink density. He explains that the system has been successfully tested by numerous third-party organizations, including a study in Israel where the product was tested in a salt spray chamber for up to 5,000 hours and then put through an in-field test for one full year at industrial plants that experience severe corrosion conditions.
The product uses conventional paint application techniques, including airless high-volume, low-pressure or low-volume, low-pressure spray equipment. As a single-component coating, it is humidity cured and requires only 2 to 3 mils (50.8 to 76.2 microns) to be applied.
It can be applied to coating systems, including two-component epoxies, two-component polyurethanes, powder coatings, polyesters, gelcoats, latexes, fiberglass, and anodized aluminum to prevent filiform corrosion. The system, which Choate says is impervious to water and oxygen, comes with a 10-year warranty.
Topcoat application of Nano-Clear can be used on many different types of commercial and industrial assets as protection. Choate says technology in the polymer-based system is updated each year with the latest nanocoating technology including ice repellency and anti-barnacle prevention.
Note: The Nano-Clear system was one of 10 winners of the 2019 Materials Performance Corrosion Innovation of the Year Award.
Looking for information on maritime corrosion protection solutions? Sign up for a free subscription to AMPP’s Maritime News.
Source: Originally appeared on materialsperformance.com
FREE DOWNLOADS
White Paper: An Action Plan for Reducing Pipeline Failures, Costs with Corrosion in the Water Sector
Special Report: The Future of Corrosion Control, Insights from the Experts
Get Updates
Featured Articles
Categories
- 2024 Olympics (1)
- 2024 Water Resource Development Act (1)
- Abrasive Blasting (1)
- Advanced coating materials (9)
- advanced coatings (1)
- Advanced Corrosion Control in Oil and Gas Industry (2)
- Advocacy (3)
- AI (2)
- Aircraft (1)
- Alkanization (1)
- AMPP (4)
- AMPP Annual Conference + Expo (5)
- ampp awards (1)
- ampp certification (2)
- Ampp Chapters (1)
- AMPP conference (1)
- AMPP logo (1)
- Ampp Membership (2)
- Ampp Standards (2)
- ampp training (2)
- Amusement parks (4)
- Architectural (1)
- Architectural Coatings (2)
- argonne national laboratory (1)
- Artificial Intelligence (1)
- Asset integrity (12)
- Asset maintenance (3)
- Asset Protection (1)
- awards (3)
- B2B Marketing (1)
- Bim Software (1)
- Biodeterioration of materials (5)
- Biofouling (4)
- Blasting (1)
- Bridges (4)
- career advancement (3)
- career development (2)
- cathodic protection (2)
- Cathodic Protection-CP (16)
- Ceramic epoxies (1)
- Certification (3)
- certification study guide (1)
- Chemical Injection (1)
- CIP (1)
- Civil Engineering (1)
- clean energy (1)
- Coating inspector (2)
- coating inspector job roles (1)
- Coating inspector jobs (2)
- Coating inspector program (2)
- Coatings (18)
- Coatings Application (3)
- coatings certification (1)
- Coatings failures (2)
- Coatings Industry (2)
- coatings inspection (1)
- Coatings inspector (2)
- Coatings measurement and inspection (9)
- coatings project management (1)
- Coatings Systems (1)
- Cold stress (1)
- Concrete (13)
- Concrete corrosion (1)
- concrete cracking (1)
- Conference and Events (2)
- Corrosion (26)
- Corrosion Basics (5)
- corrosion certification (1)
- Corrosion Control (17)
- Corrosion Control and Management (23)
- Corrosion detection (1)
- corrosion engineering (1)
- Corrosion Essentials (20)
- Corrosion Inspection (1)
- Corrosion Management (1)
- corrosion mitigation (1)
- corrosion of steel (1)
- corrosion policy (1)
- Corrosion Prevention (12)
- corrosion resistance (1)
- corrosion resources (1)
- Corrosion Under Insulation (2)
- cost of corrosion (1)
- Crevice Corrosion (1)
- Cui (2)
- Data Monitoring (1)
- decarbonization (1)
- defense infrastructure (1)
- Department of Defense (4)
- Deposition corrosion (1)
- Dissimilar Metal Corrosion (1)
- Dissolved gases (1)
- DoD (3)
- Education (2)
- EMERG (1)
- Energy industry (9)
- entertainment industry (1)
- Epoxy (3)
- exam preparation (1)
- FBE Application (1)
- FBE Inspection (1)
- Fireproofing (1)
- Flexible coatings (2)
- Flint, Michigan (1)
- Fluoropolymer coating (3)
- Forms of Corrosion (4)
- Freshwater salinization (1)
- Fusion-bonded epoxy (1)
- Galvanic (1)
- Galvanic Corrosion (4)
- General Corrosion (4)
- General Tips (1)
- glossary (1)
- Hand tools (1)
- honoree night (1)
- Industrial Application (3)
- Industrial Safety (3)
- Industry Best Practices (1)
- Industry Standards (2)
- Infrared Thermography (1)
- infrastructure (4)
- Infrastructure Durability (1)
- Inspection (1)
- integrity management (1)
- Intergranular Corrosion (1)
- Intumescent Coatings (1)
- key note speaker (1)
- leader (1)
- Machine Learning (2)
- Maintenance (2)
- Maintenance Best Practices (1)
- Maritime Coatings (11)
- Maritime industry (11)
- Master Painters Institute (2)
- material protection (1)
- materials performance (1)
- materials science (1)
- Membership (2)
- Membership Benefits (2)
- Michio Kaku (1)
- Microbiological forms (1)
- Microbiologically influenced corrosion-MIC (11)
- Military (2)
- Mineral constituents (1)
- MnDOT (1)
- MPI (3)
- mpi awards (1)
- mpi champion awards (1)
- mpi training (1)
- MPI Update (1)
- National Defense Authorization Act (1)
- national security (1)
- Navy (1)
- nickel-based alloys (1)
- Non-Destructive Testing (1)
- nuclear (1)
- nuclear Materials (1)
- nuclear reactor technology (1)
- Oil and Gas (2)
- Oil Fields (1)
- Organic matter (1)
- Oxgen (1)
- Paint and Protective coatings (32)
- Paint specification (1)
- pcs certification (1)
- Personal Protective Equipment (3)
- Petrochemical Plant Fireproofing Methods (1)
- Petrochemical Plants (1)
- Pipeline (2)
- Pitting Corrosion (2)
- Pitting Detection (1)
- Polymer-Based Coatings (1)
- Power plant (1)
- Power tools (1)
- PPE (3)
- Print Advertising (1)
- Print Marketing Strategy (1)
- professional certification (2)
- professional development (1)
- Protective Coatings (7)
- protective coatings industry (1)
- protective coatings specialist (1)
- quality assurance (1)
- radiation-resistant materials (1)
- Real-Time Corrosion Monitoring in Oil Fields (1)
- Rebar Corrosion (2)
- rectifier (1)
- Reliability (1)
- Remote monitoring and drones (4)
- Repaint (1)
- Restoration (1)
- ride maintenance (1)
- Risk-Based Inspection (1)
- Road deicers (1)
- Roads and bridges (1)
- Roller coaster (1)
- Rust (1)
- sacrificial anodes (1)
- Safety (5)
- Safety Standards (3)
- Salt pollution (1)
- Sensors (1)
- service awards (2)
- Ship Coatings (9)
- Shiptanks (1)
- Standards (10)
- Standards Committees (2)
- Steel (8)
- Steel Reinforcement (2)
- Stress Corrosion Cracking (1)
- Structural Steel (1)
- study tips (1)
- Surface Preparation (13)
- Sustainability (1)
- Sustainability and corrosion (7)
- terminology (1)
- Tools (1)
- Turbine (1)
- Types of Corrosion (1)
- Ultrasonic Testing (1)
- Uniform Corrosion (1)
- us army core of engineers (1)
- Wastewater Systems (1)
- Water crisis (1)
- Water pipe corrosion (1)
- Water quality (1)
- Water tank coatings (5)
- Water/treatment infrastructure (20)
- Waterway salinity (1)
- Workforce development (1)
- WRDA (1)