New methods needed for MIC testing in fracking wells
February 24, 2021 •Corrosion CONTROLLED, Corrosion Essentials, MIC
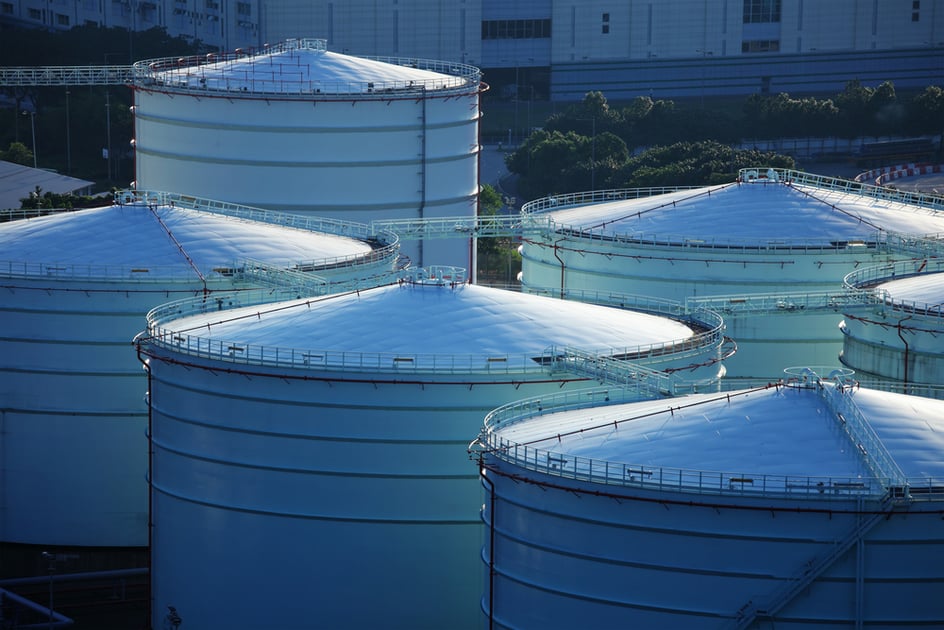
More than one bacterial family can cause microbiologically induced corrosion (MIC)
Most current industry tests focus on the detection of sulfate-reducing bacteria (SRB) as corrosive agents in U.S. shale infrastructure. However, testing could be missing a separate bacterial family also responsible for toxic, corrosive sulfides, according to a published case study conducted by researchers at several major institutions.
Funded by the National Science Foundation (Arlington, Virginia) and the U.S. Department of Energy (Washington, DC), the Ohio State University (Columbus, Ohio), West Virginia University (Morgantown, West Virginia), and the U.S. Pacific Northwest National Lab (Richland, Washington) decided to study cycling catalyzed by the microbial community in a hydraulically fractured well in the Utica Shale formation near Flushing, Ohio.
“The well continually pulls up fluids that have been sitting in the fractures for months, so it’s a good way to get a chemical and biological look at what’s going on down there,” says Mike Wilkins, an environmental microbiologist at Ohio State and senior researcher on the study. Based on their findings, the researchers believe the oil and gas industry may need to adopt new methods of monitoring and mitigating sulfide-producing bacteria in fractured shales.
How fracking influences microbiologically induced corrosion (MIC)
The “fracking” process involves high-pressure injections of water, sand, and chemicals to create fracture networks that release oil and gas, which are pumped back to the surface and recovered. According to Wilkins, since this process has only taken off in the past decade, not much is known about the microbial ecosystems in these networks.
“This is a pretty inhospitable environment of high pressure, salinity, and temperature some 2,000 meters underground,” Wilkins explains. “And the industry spends a fair amount of money trying to keep microbes out of these systems.”
These sulfide-producing microbes can cause a number of problems for drilling operators, including the corrosive degradation of metal pipelines and toxic exposure to workers on the drilling pad. Hydrogen sulfide (H2S) can also “sour” a well, Wilkins says, noting that H2S must be separated from oil and gas in an expensive process. Furthermore, the microbes themselves can gum up the extraction process by filling in tiny fractures with either biomass or excreted precipitates, he adds.
In metallic pipelines, this microbiologically influenced corrosion (MIC) is most frequently seen in the form of localized pitting.
Microbiologically induced corrosion (MIC) and fracking study results
Wilkins’ team had previously found that one bacterial family in particular, Halanaerobium, was particularly present in fractured well ecosystems. These bacteria can convert thiosulfates found in the well environment to sulfide, in contrast to sulfate-reducing bacteria (SRB)—which convert sulfate to sulfide.
Within 10 days after the pumping and sampling of well fluids had begun, the researchers found the Halanaerobium family had reached nearly 100% dominance within the bacterial community and remained so for the next 100 days.
The researchers then examined the genes present to find enzymes that might be capable of catalyzing sulfur reactions. In doing so, they found multiple copies of rhodanese, an enzyme that can reduce thiosulfate to sulfite and elemental sulfur. They also discovered multiple copies of anaerobic sulfite reductase, an enzyme that reduces sulfite to sulfide. With these two enzymes together in the well environment, it would be possible to convert thiosulfate to sulfide, Wilkins explains.
To confirm this, the researchers cultured Halanaerobium isolated from well samples. In their test, the lab-grown bacteria produced both enzymes. And when fed thiosulfate in the culture, sulfide was produced. The team also measured a particular sulfur isotope that microbes prefer to consume and found that it decreased in the well samples over time.
“That’s a sign that the sulfur cycling seen in this well is a microbial process, rather than an abiotic one,” Wilkins says.
Problems with existing microbiologically induced corrosion (MIC) testing
But according to Wilkins, most current industry tests monitor for these microbes by only searching for SRB activity. “Sulfate-reducing bacteria (SRB) are super common in seawater and groundwater and convert sulfate to sulfide,” he explains. As a result, efforts are frequently made to ensure that low-sulfate fluids are used for fracking injections.
In the Utica case study, however, no evidence of SRB was found in the data sets. Based on that, Wilkins says many existing industry tests could mistakenly lead a well operator to think that no sulfide was produced. In reality, of course, the researchers found the Halanaerobium bacteria—not SRB—had led to the formation of sulfides.
“Knowing which microbes are doing potential damage is important so that well operators can target them better,” Wilkins says, adding that the Halanaerobium family has been found in fractured well ecosystems from Texas to Pennsylvania.
AMPP has the resources to help you get the job done: Materials Performance; CoatingsPro Magazine - FREE; Maritime News - FREE.
Source: Originally appeared on materialsperformance.com and authored by staff writer, Ben DuBose.
FREE DOWNLOADS
White Paper: An Action Plan for Reducing Pipeline Failures, Costs with Corrosion in the Water Sector
Special Report: The Future of Corrosion Control, Insights from the Experts
Get Updates
Featured Articles
Categories
- 2024 Olympics (1)
- 2024 Water Resource Development Act (1)
- Abrasive Blasting (1)
- Advanced coating materials (9)
- advanced coatings (1)
- Advanced Corrosion Control in Oil and Gas Industry (2)
- Advocacy (3)
- AI (2)
- Aircraft (1)
- Alkanization (1)
- AMPP (4)
- AMPP Annual Conference + Expo (5)
- ampp awards (1)
- ampp certification (2)
- Ampp Chapters (1)
- AMPP conference (1)
- AMPP logo (1)
- Ampp Membership (2)
- Ampp Standards (2)
- ampp training (2)
- Amusement parks (4)
- Architectural (1)
- Architectural Coatings (2)
- argonne national laboratory (1)
- Artificial Intelligence (1)
- Asset integrity (12)
- Asset maintenance (3)
- Asset Protection (1)
- awards (3)
- B2B Marketing (1)
- Bim Software (1)
- Biodeterioration of materials (5)
- Biofouling (4)
- Blasting (1)
- Bridges (4)
- career advancement (3)
- career development (2)
- cathodic protection (2)
- Cathodic Protection-CP (16)
- Ceramic epoxies (1)
- Certification (3)
- certification study guide (1)
- Chemical Injection (1)
- CIP (1)
- Civil Engineering (1)
- clean energy (1)
- Coating inspector (2)
- coating inspector job roles (1)
- Coating inspector jobs (2)
- Coating inspector program (2)
- Coatings (18)
- Coatings Application (3)
- coatings certification (1)
- Coatings failures (2)
- Coatings Industry (2)
- coatings inspection (1)
- Coatings inspector (2)
- Coatings measurement and inspection (9)
- coatings project management (1)
- Coatings Systems (1)
- Cold stress (1)
- Concrete (13)
- Concrete corrosion (1)
- concrete cracking (1)
- Conference and Events (2)
- Corrosion (26)
- Corrosion Basics (5)
- corrosion certification (1)
- Corrosion Control (17)
- Corrosion Control and Management (23)
- Corrosion detection (1)
- corrosion engineering (1)
- Corrosion Essentials (20)
- Corrosion Inspection (1)
- Corrosion Management (1)
- corrosion mitigation (1)
- corrosion of steel (1)
- corrosion policy (1)
- Corrosion Prevention (12)
- corrosion resistance (1)
- corrosion resources (1)
- Corrosion Under Insulation (2)
- cost of corrosion (1)
- Crevice Corrosion (1)
- Cui (2)
- Data Monitoring (1)
- decarbonization (1)
- defense infrastructure (1)
- Department of Defense (4)
- Deposition corrosion (1)
- Dissimilar Metal Corrosion (1)
- Dissolved gases (1)
- DoD (3)
- Education (2)
- EMERG (1)
- Energy industry (9)
- entertainment industry (1)
- Epoxy (3)
- exam preparation (1)
- FBE Application (1)
- FBE Inspection (1)
- Fireproofing (1)
- Flexible coatings (2)
- Flint, Michigan (1)
- Fluoropolymer coating (3)
- Forms of Corrosion (4)
- Freshwater salinization (1)
- Fusion-bonded epoxy (1)
- Galvanic (1)
- Galvanic Corrosion (4)
- General Corrosion (4)
- General Tips (1)
- glossary (1)
- Hand tools (1)
- honoree night (1)
- Industrial Application (3)
- Industrial Safety (3)
- Industry Best Practices (1)
- Industry Standards (2)
- Infrared Thermography (1)
- infrastructure (4)
- Infrastructure Durability (1)
- Inspection (1)
- integrity management (1)
- Intergranular Corrosion (1)
- Intumescent Coatings (1)
- key note speaker (1)
- leader (1)
- Machine Learning (2)
- Maintenance (2)
- Maintenance Best Practices (1)
- Maritime Coatings (11)
- Maritime industry (11)
- Master Painters Institute (2)
- material protection (1)
- materials performance (1)
- materials science (1)
- Membership (2)
- Membership Benefits (2)
- Michio Kaku (1)
- Microbiological forms (1)
- Microbiologically influenced corrosion-MIC (11)
- Military (2)
- Mineral constituents (1)
- MnDOT (1)
- MPI (3)
- mpi awards (1)
- mpi champion awards (1)
- mpi training (1)
- MPI Update (1)
- National Defense Authorization Act (1)
- national security (1)
- Navy (1)
- nickel-based alloys (1)
- Non-Destructive Testing (1)
- nuclear (1)
- nuclear Materials (1)
- nuclear reactor technology (1)
- Oil and Gas (2)
- Oil Fields (1)
- Organic matter (1)
- Oxgen (1)
- Paint and Protective coatings (32)
- Paint specification (1)
- pcs certification (1)
- Personal Protective Equipment (3)
- Petrochemical Plant Fireproofing Methods (1)
- Petrochemical Plants (1)
- Pipeline (2)
- Pitting Corrosion (2)
- Pitting Detection (1)
- Polymer-Based Coatings (1)
- Power plant (1)
- Power tools (1)
- PPE (3)
- Print Advertising (1)
- Print Marketing Strategy (1)
- professional certification (2)
- professional development (1)
- Protective Coatings (7)
- protective coatings industry (1)
- protective coatings specialist (1)
- quality assurance (1)
- radiation-resistant materials (1)
- Real-Time Corrosion Monitoring in Oil Fields (1)
- Rebar Corrosion (2)
- rectifier (1)
- Reliability (1)
- Remote monitoring and drones (4)
- Repaint (1)
- Restoration (1)
- ride maintenance (1)
- Risk-Based Inspection (1)
- Road deicers (1)
- Roads and bridges (1)
- Roller coaster (1)
- Rust (1)
- sacrificial anodes (1)
- Safety (5)
- Safety Standards (3)
- Salt pollution (1)
- Sensors (1)
- service awards (2)
- Ship Coatings (9)
- Shiptanks (1)
- Standards (10)
- Standards Committees (2)
- Steel (8)
- Steel Reinforcement (2)
- Stress Corrosion Cracking (1)
- Structural Steel (1)
- study tips (1)
- Surface Preparation (13)
- Sustainability (1)
- Sustainability and corrosion (7)
- terminology (1)
- Tools (1)
- Turbine (1)
- Types of Corrosion (1)
- Ultrasonic Testing (1)
- Uniform Corrosion (1)
- us army core of engineers (1)
- Wastewater Systems (1)
- Water crisis (1)
- Water pipe corrosion (1)
- Water quality (1)
- Water tank coatings (5)
- Water/treatment infrastructure (20)
- Waterway salinity (1)
- Workforce development (1)
- WRDA (1)