Oil Storage Tank Failure - A MIC Case Study
September 27, 2021 •Corrosion CONTROLLED, Corrosion Essentials, MIC
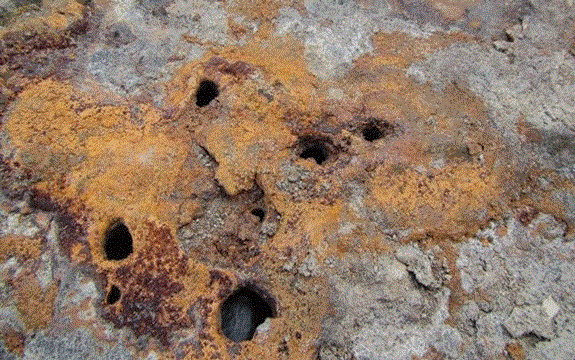
A refinery was experiencing bottom plate underside (soil-side) corrosion of its aboveground storage tanks (ASTs) at an extraordinarily high rate of 1 to 2 mm/y. This resulted in the failure of four tanks within a two-year period that occurred seven years after the refinery was commissioned. All four tanks had severely damaged bottom plates, which were constructed of 8-mm thick uncoated carbon steel.
What caused this premature failure?
Underside corrosion protection for the ASTs was provided by an impressed current cathodic protection (ICCP) system using a mixed-metal oxide (MMO) grid anode system. The corrosion morphology after the failure revealed severe localized corrosion with large, deep pits found under deposits of orange-red tubercles comprised of iron oxides.
Failure analysis of the tanks included a review of the design and function of the CP system and metallurgical tests of a failed bottom plate sample.
For the ICCP system, the MMO anode grid was placed between a high-density polyethylene (HDPE) secondary containment liner and the tank bottom, which sat on a 75-mm thick sand pad. The underside of the bottom plates was uncoated and the CP design was based on 100% bare surface area.
The failures occurred between July 2013 and August 2015, and a detailed CP survey was carried out for the storage tanks in February 2016. The results revealed that none of the tanks achieved the NACE SP0193-2016 protection criterion of –850 mV instant “off” potential. The potentials varied from –200 to –800 mV vs. a copper/copper sulfate (Cu/CuSO4) electrode (CSE), with an average “off” potential of –450 mV vs. CSE across all tanks.
Since the potentials were not meeting the –850 mV criteria, further investigation was done to understand the possible reasons for such low polarized potentials. Analysis found that design deficiencies of the ICCP system—primarily the anode depth/spacing and inappropriate distribution of power feed cables—resulted in a nonuniform potential profile across the tank bottom surface. High current and voltage attenuation along the anode grid did not provide sufficient current and polarization at a distance away from the power feeds, which led to under-protection of the tank bottom.
Because an inefficient CP system alone typically doesn’t cause such aggravated corrosion, a sample from the failed tank bottom was sent to an external laboratory for a detailed metallurgical analysis to identify corrosion products and possible corrosion mechanisms. A form of underdeposit corrosion (UDC) that can corrode steel at the rate of 1 mm/year is microbiologically influenced corrosion (MIC).
X-ray diffraction analysis of the sample plates’ soil side indicated the tubercles were made of porous layers or strata consisting mainly of iron oxides surrounded by magnetite (Fe3O4). The scales appeared to consist of multiple layers. A closer analysis performed on flakes from scale on the pits indicated the probability of iron-oxidizing bacteria (IOB) present in the corrosion, which formed deposits that further aggravated the corrosion by forming a differential aeration cell. IOB produce orange-red tubercles of iron oxides and hydroxides by oxidizing ferrous ions from the bulk medium or the substratum.
The corrosion rates observed were amplified by the ingress of water, primarily from leaking fire water sprinklers, through gaps between the annular plate and foundation, which brought in bacteria and corrosive anions such as chlorides and sulfates. Without an effective CP system and no other means of corrosion control, the tank floor was exposed to a severe form of bacterial and UDC that led to perforation and loss of inventory.
Microbiologically Influenced Corrosion (MIC) resources. Check them out here.
Source: This article was adapted from an article that originally appeared in Materials Performance. It was based on a CORROSION 2017 paper no. 9025, “Premature Failure of API 650 Oil Storage Tank Bottom Plates Due to Soil Side Corrosion."
FREE DOWNLOADS
White Paper: An Action Plan for Reducing Pipeline Failures, Costs with Corrosion in the Water Sector
Special Report: The Future of Corrosion Control, Insights from the Experts
Get Updates
Featured Articles
Categories
- 2024 Olympics (1)
- 2024 Water Resource Development Act (1)
- Abrasive Blasting (1)
- Advanced coating materials (9)
- advanced coatings (1)
- Advanced Corrosion Control in Oil and Gas Industry (2)
- Advocacy (3)
- AI (2)
- Aircraft (1)
- Alkanization (1)
- AMPP (4)
- AMPP Annual Conference + Expo (5)
- ampp awards (1)
- ampp certification (2)
- Ampp Chapters (1)
- AMPP conference (1)
- AMPP logo (1)
- Ampp Membership (2)
- Ampp Standards (2)
- ampp training (2)
- Amusement parks (4)
- Architectural (1)
- Architectural Coatings (2)
- argonne national laboratory (1)
- Artificial Intelligence (1)
- Asset integrity (12)
- Asset maintenance (3)
- Asset Protection (1)
- awards (3)
- B2B Marketing (1)
- Bim Software (1)
- Biodeterioration of materials (5)
- Biofouling (4)
- Blasting (1)
- Bridges (4)
- career advancement (3)
- career development (2)
- cathodic protection (2)
- Cathodic Protection-CP (16)
- Ceramic epoxies (1)
- Certification (3)
- certification study guide (1)
- Chemical Injection (1)
- CIP (1)
- Civil Engineering (1)
- clean energy (1)
- Coating inspector (2)
- coating inspector job roles (1)
- Coating inspector jobs (2)
- Coating inspector program (2)
- Coatings (18)
- Coatings Application (3)
- coatings certification (1)
- Coatings failures (2)
- Coatings Industry (2)
- coatings inspection (1)
- Coatings inspector (2)
- Coatings measurement and inspection (9)
- coatings project management (1)
- Coatings Systems (1)
- Cold stress (1)
- Concrete (13)
- Concrete corrosion (1)
- concrete cracking (1)
- Conference and Events (2)
- Corrosion (26)
- Corrosion Basics (5)
- corrosion certification (1)
- Corrosion Control (17)
- Corrosion Control and Management (23)
- Corrosion detection (1)
- corrosion engineering (1)
- Corrosion Essentials (20)
- Corrosion Inspection (1)
- Corrosion Management (1)
- corrosion mitigation (1)
- corrosion of steel (1)
- corrosion policy (1)
- Corrosion Prevention (12)
- corrosion resistance (1)
- corrosion resources (1)
- Corrosion Under Insulation (2)
- cost of corrosion (1)
- Crevice Corrosion (1)
- Cui (2)
- Data Monitoring (1)
- decarbonization (1)
- defense infrastructure (1)
- Department of Defense (4)
- Deposition corrosion (1)
- Dissimilar Metal Corrosion (1)
- Dissolved gases (1)
- DoD (3)
- Education (2)
- EMERG (1)
- Energy industry (9)
- entertainment industry (1)
- Epoxy (3)
- exam preparation (1)
- FBE Application (1)
- FBE Inspection (1)
- Fireproofing (1)
- Flexible coatings (2)
- Flint, Michigan (1)
- Fluoropolymer coating (3)
- Forms of Corrosion (4)
- Freshwater salinization (1)
- Fusion-bonded epoxy (1)
- Galvanic (1)
- Galvanic Corrosion (4)
- General Corrosion (4)
- General Tips (1)
- glossary (1)
- Hand tools (1)
- honoree night (1)
- Industrial Application (3)
- Industrial Safety (3)
- Industry Best Practices (1)
- Industry Standards (2)
- Infrared Thermography (1)
- infrastructure (4)
- Infrastructure Durability (1)
- Inspection (1)
- integrity management (1)
- Intergranular Corrosion (1)
- Intumescent Coatings (1)
- key note speaker (1)
- leader (1)
- Machine Learning (2)
- Maintenance (2)
- Maintenance Best Practices (1)
- Maritime Coatings (11)
- Maritime industry (11)
- Master Painters Institute (2)
- material protection (1)
- materials performance (1)
- materials science (1)
- Membership (2)
- Membership Benefits (2)
- Michio Kaku (1)
- Microbiological forms (1)
- Microbiologically influenced corrosion-MIC (11)
- Military (2)
- Mineral constituents (1)
- MnDOT (1)
- MPI (3)
- mpi awards (1)
- mpi champion awards (1)
- mpi training (1)
- MPI Update (1)
- National Defense Authorization Act (1)
- national security (1)
- Navy (1)
- nickel-based alloys (1)
- Non-Destructive Testing (1)
- nuclear (1)
- nuclear Materials (1)
- nuclear reactor technology (1)
- Oil and Gas (2)
- Oil Fields (1)
- Organic matter (1)
- Oxgen (1)
- Paint and Protective coatings (32)
- Paint specification (1)
- pcs certification (1)
- Personal Protective Equipment (3)
- Petrochemical Plant Fireproofing Methods (1)
- Petrochemical Plants (1)
- Pipeline (2)
- Pitting Corrosion (2)
- Pitting Detection (1)
- Polymer-Based Coatings (1)
- Power plant (1)
- Power tools (1)
- PPE (3)
- Print Advertising (1)
- Print Marketing Strategy (1)
- professional certification (2)
- professional development (1)
- Protective Coatings (7)
- protective coatings industry (1)
- protective coatings specialist (1)
- quality assurance (1)
- radiation-resistant materials (1)
- Real-Time Corrosion Monitoring in Oil Fields (1)
- Rebar Corrosion (2)
- rectifier (1)
- Reliability (1)
- Remote monitoring and drones (4)
- Repaint (1)
- Restoration (1)
- ride maintenance (1)
- Risk-Based Inspection (1)
- Road deicers (1)
- Roads and bridges (1)
- Roller coaster (1)
- Rust (1)
- sacrificial anodes (1)
- Safety (5)
- Safety Standards (3)
- Salt pollution (1)
- Sensors (1)
- service awards (2)
- Ship Coatings (9)
- Shiptanks (1)
- Standards (10)
- Standards Committees (2)
- Steel (8)
- Steel Reinforcement (2)
- Stress Corrosion Cracking (1)
- Structural Steel (1)
- study tips (1)
- Surface Preparation (13)
- Sustainability (1)
- Sustainability and corrosion (7)
- terminology (1)
- Tools (1)
- Turbine (1)
- Types of Corrosion (1)
- Ultrasonic Testing (1)
- Uniform Corrosion (1)
- us army core of engineers (1)
- Wastewater Systems (1)
- Water crisis (1)
- Water pipe corrosion (1)
- Water quality (1)
- Water tank coatings (5)
- Water/treatment infrastructure (20)
- Waterway salinity (1)
- Workforce development (1)
- WRDA (1)