Poorly designed microbial control programs – a real risk to oil & gas operators
January 24, 2022 •Corrosion CONTROLLED, Corrosion Essentials, MIC
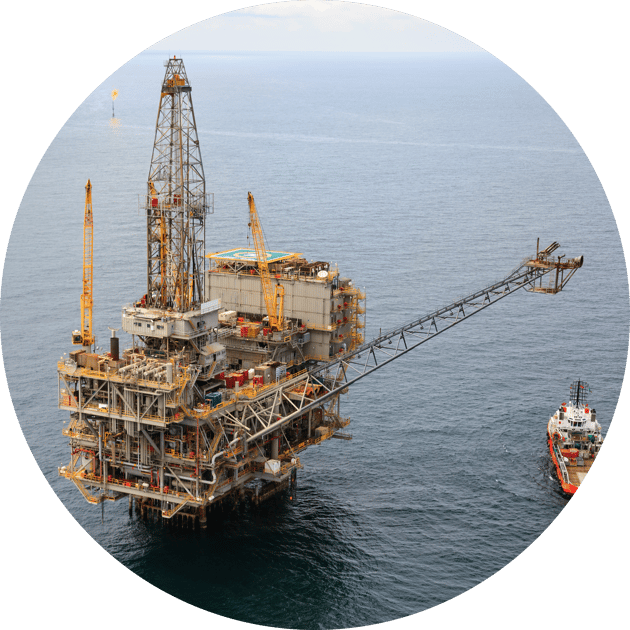
There are consequences of an inadequate microbial control program. Uncontrolled biofouling, microbially influenced corrosion or MIC, and reservoir souring can all exacerbate corrosion.
When microbes are growing in oil and gas operations, they typically attach to a surface and form a protective biofilm that can become highly problematic and very difficult to control and eradicate. These biofilms have three detrimental processes and create big concerns for oil and gas operators as it pertains to corrosion.
The first one is MIC where biofilms will form on equipment or metallurgical surfaces and create or exacerbate corrosion mechanisms, leading to pitting corrosion, which can potentially lead to loss of primary containment (LOPCs) and equipment failure.
The second one is reservoir souring or souring in general. Basically, bacteria or microbes will eat organic compounds. They’ll breathe in sulfate and biosulfate the way people breathe in oxygen, and they’ll exhale H2S. H2S is deadly to personnel if they are exposed to too high of a concentration. It devalues hydrocarbon, so sour crude is less valuable than sweet crude. And, H2S itself is corrosive.
The third one, not impacting corrosion as much but important to the industry, is biofouling. When the biomass grows, it can reduce conductivity through hydraulic fractures and decrease hydrocarbon transport and production. In conventional operations, it can dramatically reduce injectivity. The cost of implementing an effective microbial control program is quite minimal — compared to the long-term benefits of improved production rates, better asset integrity, and hydrocarbon quality.
Operators need to fully understand the risk of poorly designed microbial control programs. For example, chlorine dioxide, bleach, other oxidizers are commonly used in water treatment and hydraulic fracturing due to its very low cost. The operator may say, “I checked the box, I added a biocide. Let’s go run our operations.” However, oxidizers only provide a good short-term kill offering, no long-term activity and, they are highly corrosive at higher prolonged doses.
A look at the math shows:
• Water use in completions contain roughly a million cells per mil or in log, 10 to the sixth.
• Oxidizers often state a “99.99% kill,” which, on the surface is four logs and might appear adequate.
• However, 100 cells per mil alive remain and go into the reservoir. And while not all these cells are going to survive, it is estimated that 1% will.
• A gallon of water, meanwhile, has about 4,000 ml, which is 4,000 microbes.
• When a typical fracking job, for example, uses 5 million gallons of water and that then is multiplied by 4,000, the result is the injection of 20 billion microbes into the reservoir that can thrive, form populations, and produce H2S, because of a poorly designed biocide program.
To put this in perspective, the earth’s population is 8 billion. The operator has wasted money in paying for the oxidizer and potentially caused massive and chronic corrosion, souring, and biofouling issues.
There are other chemistries that can also cause problems. Tributyl tetradecyl phosphonium chloride, or TTPC, is a quad-based biocide common in hydraulic fracturing, and it is marketed as both quick-quick biocide for top side as well as a long-acting preservative down hole.
But under real-world conditions, this chemistry is deactivated by high TBS. A lot of the water used in frack is salty, interacts with potential, and potentially damages frack packages and slick water fracks. Additionally, it’s deactivated by binding to proppant and shale. Like oxidizers, TTPC is not available for long-term control and without it, 20 billion bacteria are entering the reservoir.
Microbiologically influenced corrosion resources at AMPP, the Association for Materials Protection and Performance.
Source: Excerpted from a Materials Performance podcast with Ken Wunch, energy technology advisor at DuPont Microbial Control.
FREE DOWNLOADS
White Paper: An Action Plan for Reducing Pipeline Failures, Costs with Corrosion in the Water Sector
Special Report: The Future of Corrosion Control, Insights from the Experts
Get Updates
Featured Articles
Categories
- 2024 Olympics (1)
- 2024 Water Resource Development Act (1)
- Abrasive Blasting (1)
- Advanced coating materials (9)
- advanced coatings (1)
- Advanced Corrosion Control in Oil and Gas Industry (2)
- Advocacy (3)
- AI (2)
- Aircraft (1)
- Alkanization (1)
- AMPP (4)
- AMPP Annual Conference + Expo (5)
- ampp awards (1)
- ampp certification (2)
- Ampp Chapters (1)
- AMPP conference (1)
- AMPP logo (1)
- Ampp Membership (2)
- Ampp Standards (2)
- ampp training (2)
- Amusement parks (4)
- Architectural (1)
- Architectural Coatings (2)
- argonne national laboratory (1)
- Artificial Intelligence (1)
- Asset integrity (12)
- Asset maintenance (3)
- Asset Protection (1)
- awards (3)
- B2B Marketing (1)
- Bim Software (1)
- Biodeterioration of materials (5)
- Biofouling (4)
- Blasting (1)
- Bridges (4)
- career advancement (3)
- career development (2)
- cathodic protection (2)
- Cathodic Protection-CP (16)
- Ceramic epoxies (1)
- Certification (3)
- certification study guide (1)
- Chemical Injection (1)
- CIP (1)
- Civil Engineering (1)
- clean energy (1)
- Coating inspector (2)
- coating inspector job roles (1)
- Coating inspector jobs (2)
- Coating inspector program (2)
- Coatings (18)
- Coatings Application (3)
- coatings certification (1)
- Coatings failures (2)
- Coatings Industry (2)
- coatings inspection (1)
- Coatings inspector (2)
- Coatings measurement and inspection (9)
- coatings project management (1)
- Coatings Systems (1)
- Cold stress (1)
- Concrete (13)
- Concrete corrosion (1)
- concrete cracking (1)
- Conference and Events (2)
- Corrosion (26)
- Corrosion Basics (5)
- corrosion certification (1)
- Corrosion Control (17)
- Corrosion Control and Management (23)
- Corrosion detection (1)
- corrosion engineering (1)
- Corrosion Essentials (20)
- Corrosion Inspection (1)
- Corrosion Management (1)
- corrosion mitigation (1)
- corrosion of steel (1)
- corrosion policy (1)
- Corrosion Prevention (12)
- corrosion resistance (1)
- corrosion resources (1)
- Corrosion Under Insulation (2)
- cost of corrosion (1)
- Crevice Corrosion (1)
- Cui (2)
- Data Monitoring (1)
- decarbonization (1)
- defense infrastructure (1)
- Department of Defense (4)
- Deposition corrosion (1)
- Dissimilar Metal Corrosion (1)
- Dissolved gases (1)
- DoD (3)
- Education (2)
- EMERG (1)
- Energy industry (9)
- entertainment industry (1)
- Epoxy (3)
- exam preparation (1)
- FBE Application (1)
- FBE Inspection (1)
- Fireproofing (1)
- Flexible coatings (2)
- Flint, Michigan (1)
- Fluoropolymer coating (3)
- Forms of Corrosion (4)
- Freshwater salinization (1)
- Fusion-bonded epoxy (1)
- Galvanic (1)
- Galvanic Corrosion (4)
- General Corrosion (4)
- General Tips (1)
- glossary (1)
- Hand tools (1)
- honoree night (1)
- Industrial Application (3)
- Industrial Safety (3)
- Industry Best Practices (1)
- Industry Standards (2)
- Infrared Thermography (1)
- infrastructure (4)
- Infrastructure Durability (1)
- Inspection (1)
- integrity management (1)
- Intergranular Corrosion (1)
- Intumescent Coatings (1)
- key note speaker (1)
- leader (1)
- Machine Learning (2)
- Maintenance (2)
- Maintenance Best Practices (1)
- Maritime Coatings (11)
- Maritime industry (11)
- Master Painters Institute (2)
- material protection (1)
- materials performance (1)
- materials science (1)
- Membership (2)
- Membership Benefits (2)
- Michio Kaku (1)
- Microbiological forms (1)
- Microbiologically influenced corrosion-MIC (11)
- Military (2)
- Mineral constituents (1)
- MnDOT (1)
- MPI (3)
- mpi awards (1)
- mpi champion awards (1)
- mpi training (1)
- MPI Update (1)
- National Defense Authorization Act (1)
- national security (1)
- Navy (1)
- nickel-based alloys (1)
- Non-Destructive Testing (1)
- nuclear (1)
- nuclear Materials (1)
- nuclear reactor technology (1)
- Oil and Gas (2)
- Oil Fields (1)
- Organic matter (1)
- Oxgen (1)
- Paint and Protective coatings (32)
- Paint specification (1)
- pcs certification (1)
- Personal Protective Equipment (3)
- Petrochemical Plant Fireproofing Methods (1)
- Petrochemical Plants (1)
- Pipeline (2)
- Pitting Corrosion (2)
- Pitting Detection (1)
- Polymer-Based Coatings (1)
- Power plant (1)
- Power tools (1)
- PPE (3)
- Print Advertising (1)
- Print Marketing Strategy (1)
- professional certification (2)
- professional development (1)
- Protective Coatings (7)
- protective coatings industry (1)
- protective coatings specialist (1)
- quality assurance (1)
- radiation-resistant materials (1)
- Real-Time Corrosion Monitoring in Oil Fields (1)
- Rebar Corrosion (2)
- rectifier (1)
- Reliability (1)
- Remote monitoring and drones (4)
- Repaint (1)
- Restoration (1)
- ride maintenance (1)
- Risk-Based Inspection (1)
- Road deicers (1)
- Roads and bridges (1)
- Roller coaster (1)
- Rust (1)
- sacrificial anodes (1)
- Safety (5)
- Safety Standards (3)
- Salt pollution (1)
- Sensors (1)
- service awards (2)
- Ship Coatings (9)
- Shiptanks (1)
- Standards (10)
- Standards Committees (2)
- Steel (8)
- Steel Reinforcement (2)
- Stress Corrosion Cracking (1)
- Structural Steel (1)
- study tips (1)
- Surface Preparation (13)
- Sustainability (1)
- Sustainability and corrosion (7)
- terminology (1)
- Tools (1)
- Turbine (1)
- Types of Corrosion (1)
- Ultrasonic Testing (1)
- Uniform Corrosion (1)
- us army core of engineers (1)
- Wastewater Systems (1)
- Water crisis (1)
- Water pipe corrosion (1)
- Water quality (1)
- Water tank coatings (5)
- Water/treatment infrastructure (20)
- Waterway salinity (1)
- Workforce development (1)
- WRDA (1)