Air Force researches microbiologically induced corrosion in aircraft
April 22, 2021 •Corrosion CONTROLLED, Corrosion Essentials, MIC
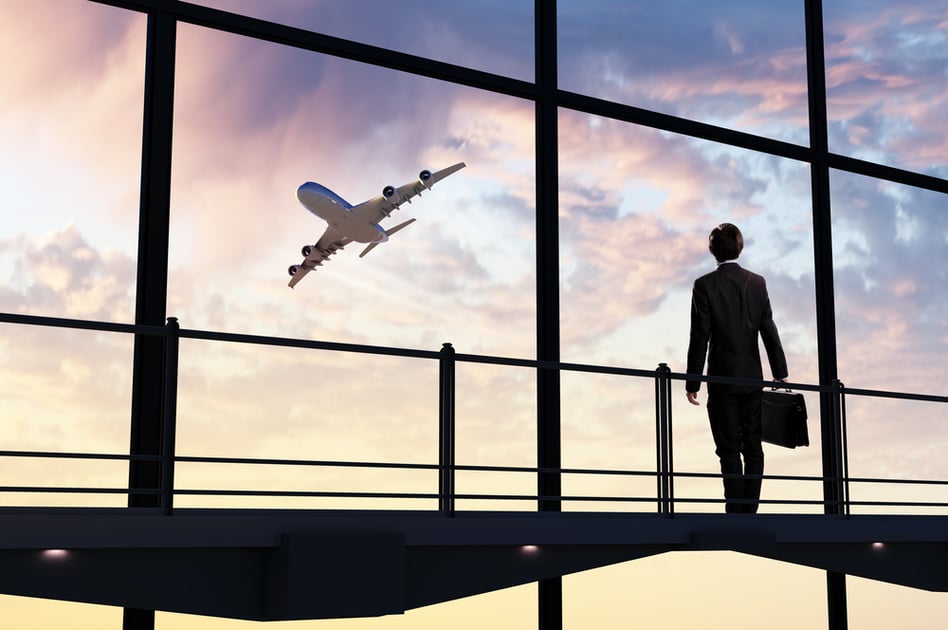
Corrosion is a major factor affecting the overall health of military aircraft. Anything from changing temperatures to environmental factors can cause corrosion. Microbes, however, are major contributors that are often overlooked.
The biological materials and processing research team at the Air Force Research Laboratory (AFRL) (Wright-Patterson Air Force Base, Ohio) is shining a new light on microbiologically influenced corrosion (MIC) and how it affects aircraft structures and fuel systems by studying the causes, effects, and prevention of corrosion caused by living organisms.
Decontamination enclosure can eliminate corrosion-causing microbes
Over time, mold, mildew, fungi, bacteria, and other organic contaminants can build up on aircraft structures as a result of a number of factors, including moisture, humidity, and human contact. Contaminants not only pose potential health hazards to maintenance crews, but some also can produce acids and enzymes that slowly corrode aircraft surfaces.
“Microorganisms can eat away at surface materials, and some of the worst areas affected are tight, hard-to-reach areas that maintainers have difficulty disinfecting,” says Wendy Goodson, the AFRL biological materials team lead.
As the military fleet ages, microbial contamination is poised to become an increasingly urgent issue. To address the problem, Goodson helped validate and test the Joint Biological Agent Decontamination System (JBADS), an environmentally controlled enclosure in which an entire aircraft—even areas inaccessible to maintenance crews—can be heated to temperatures of up to 180 °F (82 °C). The process eliminates over 99.9% of biological contaminants on aircraft surfaces safely and quickly, without putting aircrews and support personnel at risk of exposure. Also, because the microbes are virtually eliminated, regrowth is greatly inhibited.
JBADS offers numerous other benefits over traditional manual decontamination. It enables the full decontamination of an aircraft in hours as opposed to days, allowing it to be returned to service more quickly. It also reduces manpower, thereby lowering maintenance costs.
System could also reduce biofouling costs on fuel storage tanks
In addition to surface contamination, Goodson’s team is also looking into the effects of bio-contaminants in fuel systems.
In an effort to move toward more environmentally friendly energy solutions, the Air Force increasingly relies on biofuels, which come with their own challenges. Since biofuels are processed from organic materials, such as vegetable oils and animal fats, microbes live and thrive in them. These microbial contaminants can create unwanted consequences, such as fuel fouling, fuel degradation, and material degradation.
Goodson’s team studies the impact of microbial contamination on biofuels, including how quickly and under what environmental conditions contamination occurs, how susceptible biofuels are to contamination, and the effect of biofilm buildup on aircraft and ground fuel systems. The team is studying potential effects of biofuel contamination on tanker aircraft, establishing baseline microbial readings, and pinpointing areas that harbor microbiology.
A matter of particular interest to the team is the impact of bioaccumulation on fuel storage tanks. By conducting coupon tests, the team has discovered that microbes immediately begin affecting steel and other structural materials. Over time, the biofilms cause pitting and corrosion. This information tells the team that contamination of biofuels is a potential threat to tanker and storage structures as well.
To combat fuel storage tank contamination, maintainers typically power wash the tanks; however, tanks that store biofuels require much more frequent decontamination than nonorganic jet fuel storage tanks, and power-washing methods have proven less effective for biofuels.
“It is impossible to remove every trace of microbial matter,” Goodson says. “Power-washing removes visible biomass, but leaves billions of microorganisms that begin reinfecting the next batch of fuel as soon as in it introduced into the tank.”
This is where JBADS comes into play again. The AFRL team is working to expand JBADS for use on fuel storage tanks. By using JBADS, maintainers will not only clean the tanks but also sanitize them, greatly reducing the rate of reaccumulation of microbes and, therefore, increasing the amount of time between cleaning cycles.
Summary
The Air Force spends approximately $6 billion annually on corrosion issues, of which up to $1.2 billion is potentially spent on MIC. Add to that the costs of biofuel fouling, storage tank and structure cleaning, and other preventive and maintenance costs, and Goodson says the technologies her team is developing could be critical tools for the future of the warfighter.
“These solutions are essential in light the changing face of fuels and fuel systems. They could be real game changers for military aircraft sustainment,” Goodson says.
You may also be interested in:
• SSPC Aerospace Coating Application Specialist Program (Education)
•Microbiologically Influenced Corrosion in the Upstream Oil & Gas Industry (Publication)
Source: Originally appeared on materialsperformance.com, authored by Holly Jordan, Air Force Research Laboratory Materials and Manufacturing Directorate.
FREE DOWNLOADS
White Paper: An Action Plan for Reducing Pipeline Failures, Costs with Corrosion in the Water Sector
Special Report: The Future of Corrosion Control, Insights from the Experts
Get Updates
Featured Articles
Categories
- 2024 Olympics (1)
- 2024 Water Resource Development Act (1)
- Abrasive Blasting (1)
- Advanced coating materials (9)
- advanced coatings (1)
- Advanced Corrosion Control in Oil and Gas Industry (2)
- Advocacy (3)
- AI (2)
- Aircraft (1)
- Alkanization (1)
- AMPP (4)
- AMPP Annual Conference + Expo (5)
- ampp awards (1)
- ampp certification (2)
- Ampp Chapters (1)
- AMPP conference (1)
- AMPP logo (1)
- Ampp Membership (2)
- Ampp Standards (2)
- ampp training (2)
- Amusement parks (4)
- Architectural (1)
- Architectural Coatings (2)
- argonne national laboratory (1)
- Artificial Intelligence (1)
- Asset integrity (12)
- Asset maintenance (3)
- Asset Protection (1)
- awards (3)
- B2B Marketing (1)
- Bim Software (1)
- Biodeterioration of materials (5)
- Biofouling (4)
- Blasting (1)
- Bridges (4)
- career advancement (3)
- career development (2)
- cathodic protection (2)
- Cathodic Protection-CP (16)
- Ceramic epoxies (1)
- Certification (3)
- certification study guide (1)
- Chemical Injection (1)
- CIP (1)
- Civil Engineering (1)
- clean energy (1)
- Coating inspector (2)
- coating inspector job roles (1)
- Coating inspector jobs (2)
- Coating inspector program (2)
- Coatings (18)
- Coatings Application (3)
- coatings certification (1)
- Coatings failures (2)
- Coatings Industry (2)
- coatings inspection (1)
- Coatings inspector (2)
- Coatings measurement and inspection (9)
- coatings project management (1)
- Coatings Systems (1)
- Cold stress (1)
- Concrete (13)
- Concrete corrosion (1)
- concrete cracking (1)
- Conference and Events (2)
- Corrosion (26)
- Corrosion Basics (5)
- corrosion certification (1)
- Corrosion Control (17)
- Corrosion Control and Management (23)
- Corrosion detection (1)
- corrosion engineering (1)
- Corrosion Essentials (20)
- Corrosion Inspection (1)
- Corrosion Management (1)
- corrosion mitigation (1)
- corrosion of steel (1)
- corrosion policy (1)
- Corrosion Prevention (12)
- corrosion resistance (1)
- corrosion resources (1)
- Corrosion Under Insulation (2)
- cost of corrosion (1)
- Crevice Corrosion (1)
- Cui (2)
- Data Monitoring (1)
- decarbonization (1)
- defense infrastructure (1)
- Department of Defense (4)
- Deposition corrosion (1)
- Dissimilar Metal Corrosion (1)
- Dissolved gases (1)
- DoD (3)
- Education (2)
- EMERG (1)
- Energy industry (9)
- entertainment industry (1)
- Epoxy (3)
- exam preparation (1)
- FBE Application (1)
- FBE Inspection (1)
- Fireproofing (1)
- Flexible coatings (2)
- Flint, Michigan (1)
- Fluoropolymer coating (3)
- Forms of Corrosion (4)
- Freshwater salinization (1)
- Fusion-bonded epoxy (1)
- Galvanic (1)
- Galvanic Corrosion (4)
- General Corrosion (4)
- General Tips (1)
- glossary (1)
- Hand tools (1)
- honoree night (1)
- Industrial Application (3)
- Industrial Safety (3)
- Industry Best Practices (1)
- Industry Standards (2)
- Infrared Thermography (1)
- infrastructure (4)
- Infrastructure Durability (1)
- Inspection (1)
- integrity management (1)
- Intergranular Corrosion (1)
- Intumescent Coatings (1)
- key note speaker (1)
- leader (1)
- Machine Learning (2)
- Maintenance (2)
- Maintenance Best Practices (1)
- Maritime Coatings (11)
- Maritime industry (11)
- Master Painters Institute (2)
- material protection (1)
- materials performance (1)
- materials science (1)
- Membership (2)
- Membership Benefits (2)
- Michio Kaku (1)
- Microbiological forms (1)
- Microbiologically influenced corrosion-MIC (11)
- Military (2)
- Mineral constituents (1)
- MnDOT (1)
- MPI (3)
- mpi awards (1)
- mpi champion awards (1)
- mpi training (1)
- MPI Update (1)
- National Defense Authorization Act (1)
- national security (1)
- Navy (1)
- nickel-based alloys (1)
- Non-Destructive Testing (1)
- nuclear (1)
- nuclear Materials (1)
- nuclear reactor technology (1)
- Oil and Gas (2)
- Oil Fields (1)
- Organic matter (1)
- Oxgen (1)
- Paint and Protective coatings (32)
- Paint specification (1)
- pcs certification (1)
- Personal Protective Equipment (3)
- Petrochemical Plant Fireproofing Methods (1)
- Petrochemical Plants (1)
- Pipeline (2)
- Pitting Corrosion (2)
- Pitting Detection (1)
- Polymer-Based Coatings (1)
- Power plant (1)
- Power tools (1)
- PPE (3)
- Print Advertising (1)
- Print Marketing Strategy (1)
- professional certification (2)
- professional development (1)
- Protective Coatings (7)
- protective coatings industry (1)
- protective coatings specialist (1)
- quality assurance (1)
- radiation-resistant materials (1)
- Real-Time Corrosion Monitoring in Oil Fields (1)
- Rebar Corrosion (2)
- rectifier (1)
- Reliability (1)
- Remote monitoring and drones (4)
- Repaint (1)
- Restoration (1)
- ride maintenance (1)
- Risk-Based Inspection (1)
- Road deicers (1)
- Roads and bridges (1)
- Roller coaster (1)
- Rust (1)
- sacrificial anodes (1)
- Safety (5)
- Safety Standards (3)
- Salt pollution (1)
- Sensors (1)
- service awards (2)
- Ship Coatings (9)
- Shiptanks (1)
- Standards (10)
- Standards Committees (2)
- Steel (8)
- Steel Reinforcement (2)
- Stress Corrosion Cracking (1)
- Structural Steel (1)
- study tips (1)
- Surface Preparation (13)
- Sustainability (1)
- Sustainability and corrosion (7)
- terminology (1)
- Tools (1)
- Turbine (1)
- Types of Corrosion (1)
- Ultrasonic Testing (1)
- Uniform Corrosion (1)
- us army core of engineers (1)
- Wastewater Systems (1)
- Water crisis (1)
- Water pipe corrosion (1)
- Water quality (1)
- Water tank coatings (5)
- Water/treatment infrastructure (20)
- Waterway salinity (1)
- Workforce development (1)
- WRDA (1)