Fundamentals of Rectifier Operation, Monitoring, and Maintenance
November 25, 2024 •AMPP
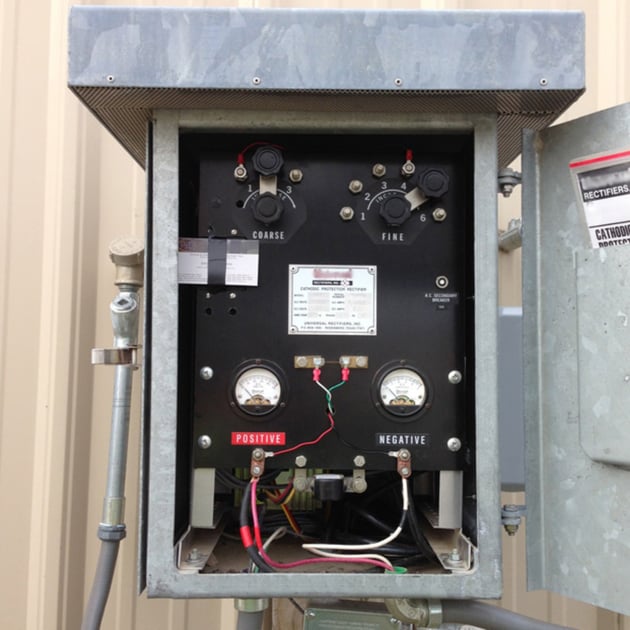
A rectifier is an electrical device that converts alternating current (AC), which periodically reverses direction, to direct current (DC).
Sustainability seems to be the latest catch-phrase, and cathodic protection (CP) is an important component for the sustainability of many metal structures. What better way to preserve and maintain infrastructure than to mitigate corrosion? Some CP systems are comprised of sacrificial anodes that naturally corrode to protect less active metals such as steel. Others require power sources to drive protective current in the right direction. The most common impressed current voltage sources are rectifiers, which can break down. Well-maintained rectifiers can provide uninterrupted CP, which reduces repair costs and labor/technician time. This article discusses the fundamentals of rectifier operation and maintenance along with basic recommendations.
Sustainability is the capacity to endure. The root purpose of any cathodic protection (CP) system is to mitigate corrosion. Preserving a pipe or other metallic structure by preventing corrosion damage allows it to endure. Therefore, corrosion mitigation leads to sustainability.
CP is most commonly achieved by means of a galvanic (sacrificial) or impressed current system. A galvanic CP system is comprised of sacrificial anodes typically made of active metals (aluminum, magnesium, or zinc) that corrode in order to provide protective currents for a less active metal, such as pipeline steel. An impressed current CP (ICCP) system utilizes external power in the form of a rectifier or other voltage source that drives impressed current anodes (e.g., cast iron, graphite, and mixed metal oxide) to corrode in order to distribute protective current to the structure (cathode).
A rectifier is an electrical device that converts alternating current (AC), which periodically reverses direction, to direct current (DC), which flows in only one direction. It is imperative that a rectifier remain in a state of constant operation. Because a rectifier is an electrical device, it is vulnerable to power surges. A nearby lightning strike can cause the circuit breaker to trip or a diode to short. Therefore, routine inspections and monitoring are necessary to maintain a properly functioning, long-lasting rectifier.
Safety is the most important aspect of all inspections. The goal of any task related to rectifier operation is to perform the work safely, which includes wearing the proper protective equipment.
Operation
There are three major components in a rectifier: transformer, stack, and cabinet. The purpose of the transformer is to safely separate the incoming AC voltage (primary side) from the secondary side, which is adjusted to control the output voltage of the rectifier. Typically, these adjustments are made with tap bars connected to the secondary side windings at intervals that offer several setting options. The stack is the actual rectifier and is comprised of a set of silicon diodes or selenium plates that function as unidirectional current valves. The diodes or plates are configured so that cycling AC flows in one direction and is blocked in the other, resulting in both directions of the AC wave flowing in the same direction. The cabinet, which includes the test panel, safely houses these components, and allows for monitoring and other advanced operations.
Additional items that may be found in a typical rectifier include a circuit breaker, voltage and current output meters, lightning arrestors, surge suppressors, transformer tap bars, and fuses.
Table 1 lists general rectifier do’s and don’ts.1 This information helps to ensure personnel safety and reliable, long-term operation of the rectifier.
Monitoring
Routine monitoring is recommended for all rectifier installations. The main purpose of monitoring is to ensure the rectifier is still operating and that a power surge hasn’t tripped the breaker. Some facilities require certain inspections at particular intervals. For example, natural gas and petroleum pipeline operators are required to inspect their rectifiers six times per year in intervals that don’t exceed 21 months. Also, company policy may dictate an even stricter inspection interval.
Monitoring is typically comprised of both a visual inspection and electrical testing. The visual inspection might include looking for physical damage of the installation/ cabinet/components, evidence of overheating, and signs of insect/rodent nests, along with recording the specifics of the rectifier unit and meter readings/tap settings. Testing often includes taking manual measurements of the rectifier output voltage and current to verify meter accuracy and structure-to-electrolyte potentials. Equipment to remotely monitor rectifiers that are difficult to access is also available; however, these devices are best used as an adjunct to on-site monitoring rather than a replacement of it.
Prior to performing visual inspection and testing, it is important to put on the appropriate personal protective equipment (PPE). As a minimum, safety glasses, leather work boots (with moisture barriers where appropriate), and leather or rubber gloves should be used. Company policy may identify additional PPE requirements.
When first approaching the rectifier, be aware of its surroundings, such as uneven footing, poisonous plants, or standing water. Use all senses to detect evidence of malfunction, including visual (e.g., scorching) and audible (e.g., crackling). Test the cabinet for the presence of AC with an approved AC detector. The old-fashioned way of determining whether the cabinet is electrified (or hot) was to brush it with the back of the hand. With the advent of the AC detector, this is no longer necessary or advisable. Knock on the cabinet to notify any inhabitants (wasps, mice, spiders, and even snakes) that you are coming in. Be sure to have insect spray handy.
Maintenance
The major causes of rectifier failure are neglect, age, and lightning. Before performing any troubleshooting of a non-functioning rectifier, be sure to turn it off, both at the circuit breaker and at the panel disconnect. The most common rectifier problems include faulty meters, loose terminals, blown fuses, open structure/groundbed leads, and lightning damage (even where lightning arresters are present). The purpose of troubleshooting is to systematically isolate the rectifier components until the defective part is found, and following the rectifier manufacturer’s recommendations for maintenance and troubleshooting is recommended.
Test the circuit breaker, transformer, rectifier stack, meters, fuses, choke, capacitors, and lightning arrestors separately. Keep an eye out for loose connections, signs of arcing, and strange odors. Additional testing may be required to verify the integrity of the structure and groundbed lead wires.
Table 2 contains a troubleshooting chart2 designed to help diagnose rectifier problems quickly.
Common Scenarios and Tricks of the Trade
Often a rectifier is found with voltage output and no current output. Since output voltage suggests that the rectification circuits are intact, one or both of the output cables might be broken, or the anode groundbed might be completely depleted. To begin troubleshooting, identify a suitable temporary ground that is electrically isolated, such as a culvert, fence, power pole guy wire anchor, or street sign. Turn the rectifier off, then disconnect the structure lead wire, and connect the temporary ground to the negative lug. Adjust the tap bars to one of the lowest settings, and energize the rectifier. If the rectifier now produces both volts and amps, then the structure lead wire is broken. If there are still no amps, then turn the rectifier off, return the structure lead wire to the negative lug, disconnect the anode lead wire, and connect the temporary ground to the positive lug. Energize the rectifier. If the rectifier now produces both volts and amps, then the anode lead wire is broken or the existing groundbed is depleted. If there are still no amps, then additional testing is required to evaluate the effectiveness of the structure and anode lead wires to determine if the problem involves both wires.
Another common occurrence is to find the rectifier with a blown fuse. This may be the result of a power surge and simply requires the installation of a replacement fuse. However, rectifier fuses can be quite expensive. Temporarily installing a circuit breaker across the fuse clips permits testing the rectifier’s operation without consuming several fuses. A typical home-style circuit breaker, appropriately sized for the application, may be used for this test. Simply attach test lead wires to each end of the circuit breaker, and attach the lead wires to each of the fuse’s existing mounting clips. Be sure to prevent the circuit breaker and lead wires from contacting the rectifier cabinet or any other metallic object. Energize the rectifier. If the breaker doesn’t trip, then simply replace the fuse. If the circuit breaker trips, then other problems exist and additional troubleshooting should be performed.
Sometimes a rectifier can be found with a tripped circuit breaker. This might be the result of a power surge and simply requires the circuit breaker to be reset. However, surges are not desirable as the rectifier might remain off for long durations. Be sure to test the effectiveness of the rectifier’s electrical grounding and follow the National Electric Code (NEC) guidelines. Install supplemental grounding as required. In addition, there are available surge suppressors that may be installed to help mitigate power surges. Be sure to follow the manufacturer’s sizing recommendations.
Rectifier housekeeping is also very important to prevent insects, rodents, and other animals from building nests. Insect and rodent nests can be dangerous inside a rectifier cabinet. Insect stings or even snake bites are definitely not desirable. However, the nests themselves can cause problems too. Apart from being a possible fire hazard, a nest can impede air flow through the rectifier cabinet and lead to overheating (and eventual failure) of the components. Ensure that insects and rodents do not move into a rectifier. Some of the ways to keep pests out are to seal all penetrations into the cabinet other than those intended for ventilation, or use a chemical pesticide to dissuade their interest in moving in. For sealing the penetrations and conduits, a duct seal or a viscous-elastic amorphous apolar polyolefin (e.g., VISCOTAQ†) may be used to close any of the cabinet openings. A simple and effective chemical pesticide that is ideal for use within a rectifier is a small, open cup of mothballs. They are easy to acquire and work very well.
Summary
A key to the sustainability of structures is effective CP as a means of corrosion control/mitigation. Rectifiers are great tools that help to provide effective ICCP. They require routine monitoring and, at times, minor repair. Rectifier monitoring and maintenance is a necessity, but it can be performed safely, which helps ensure reliable, long-term rectifier operation.
Acknowledgments
The author acknowledges the support of Integrated Rectifier Technologies, Inc., 15360–116 Ave., Edmonton, AB, Canada, T5M 3Z6; Universal Rectifiers, Inc., 1631 Cottonwood School Rd., Rosenberg, TX 77471; ERICO International, 34600 Solon Rd., Solon, OH 44139; Amcorr Products & Services, 8000 IH 10 W. #600, San Antonio, TX 78230; Tim Jenkins; and Don Olson.
References1 “General Rectifier Do’s and Don’ts,” Integrated Rectifier Technologies, Inc., http://irtrectifier.com/technical-info/rectifier-safety/ (July 15, 2013).
2 “Rectifier Troubleshooting,” Universal Rectifiers, Inc., http://www.universalrectifiers.com/PDF%20Files/Troubleshooting.pdf (July 15, 2013).
This article is based on CORROSION 2015 paper no. 5667, presented in Dallas, Texas.
†Trade name.
About the Author
Get Updates
Featured Articles
Categories
- 2024 Olympics (1)
- 2024 Water Resource Development Act (1)
- Abrasive Blasting (1)
- Advanced coating materials (9)
- advanced coatings (1)
- Advanced Corrosion Control in Oil and Gas Industry (2)
- Advocacy (3)
- AI (2)
- Aircraft (1)
- Alkanization (1)
- AMPP (4)
- AMPP Annual Conference + Expo (5)
- ampp awards (1)
- ampp certification (2)
- Ampp Chapters (1)
- AMPP conference (1)
- AMPP logo (1)
- Ampp Membership (2)
- Ampp Standards (2)
- ampp training (2)
- Amusement parks (4)
- Architectural (1)
- Architectural Coatings (2)
- argonne national laboratory (1)
- Artificial Intelligence (1)
- Asset integrity (12)
- Asset maintenance (3)
- Asset Protection (1)
- awards (3)
- B2B Marketing (1)
- Bim Software (1)
- Biodeterioration of materials (5)
- Biofouling (4)
- Blasting (1)
- Bridges (4)
- career advancement (3)
- career development (2)
- cathodic protection (2)
- Cathodic Protection-CP (16)
- Ceramic epoxies (1)
- Certification (3)
- certification study guide (1)
- Chemical Injection (1)
- CIP (1)
- Civil Engineering (1)
- clean energy (1)
- Coating inspector (2)
- coating inspector job roles (1)
- Coating inspector jobs (2)
- Coating inspector program (2)
- Coatings (18)
- Coatings Application (3)
- coatings certification (1)
- Coatings failures (2)
- Coatings Industry (2)
- coatings inspection (1)
- Coatings inspector (2)
- Coatings measurement and inspection (9)
- coatings project management (1)
- Coatings Systems (1)
- Cold stress (1)
- Concrete (13)
- Concrete corrosion (1)
- concrete cracking (1)
- Conference and Events (2)
- Corrosion (26)
- Corrosion Basics (5)
- corrosion certification (1)
- Corrosion Control (17)
- Corrosion Control and Management (23)
- Corrosion detection (1)
- corrosion engineering (1)
- Corrosion Essentials (20)
- Corrosion Inspection (1)
- Corrosion Management (1)
- corrosion mitigation (1)
- corrosion of steel (1)
- corrosion policy (1)
- Corrosion Prevention (12)
- corrosion resistance (1)
- corrosion resources (1)
- Corrosion Under Insulation (2)
- cost of corrosion (1)
- Crevice Corrosion (1)
- Cui (2)
- Data Monitoring (1)
- decarbonization (1)
- defense infrastructure (1)
- Department of Defense (4)
- Deposition corrosion (1)
- Dissimilar Metal Corrosion (1)
- Dissolved gases (1)
- DoD (3)
- Education (2)
- EMERG (1)
- Energy industry (9)
- entertainment industry (1)
- Epoxy (3)
- exam preparation (1)
- FBE Application (1)
- FBE Inspection (1)
- Fireproofing (1)
- Flexible coatings (2)
- Flint, Michigan (1)
- Fluoropolymer coating (3)
- Forms of Corrosion (4)
- Freshwater salinization (1)
- Fusion-bonded epoxy (1)
- Galvanic (1)
- Galvanic Corrosion (4)
- General Corrosion (4)
- General Tips (1)
- glossary (1)
- Hand tools (1)
- honoree night (1)
- Industrial Application (3)
- Industrial Safety (3)
- Industry Best Practices (1)
- Industry Standards (2)
- Infrared Thermography (1)
- infrastructure (4)
- Infrastructure Durability (1)
- Inspection (1)
- integrity management (1)
- Intergranular Corrosion (1)
- Intumescent Coatings (1)
- key note speaker (1)
- leader (1)
- Machine Learning (2)
- Maintenance (2)
- Maintenance Best Practices (1)
- Maritime Coatings (11)
- Maritime industry (11)
- Master Painters Institute (2)
- material protection (1)
- materials performance (1)
- materials science (1)
- Membership (2)
- Membership Benefits (2)
- Michio Kaku (1)
- Microbiological forms (1)
- Microbiologically influenced corrosion-MIC (11)
- Military (2)
- Mineral constituents (1)
- MnDOT (1)
- MPI (3)
- mpi awards (1)
- mpi champion awards (1)
- mpi training (1)
- MPI Update (1)
- National Defense Authorization Act (1)
- national security (1)
- Navy (1)
- nickel-based alloys (1)
- Non-Destructive Testing (1)
- nuclear (1)
- nuclear Materials (1)
- nuclear reactor technology (1)
- Oil and Gas (2)
- Oil Fields (1)
- Organic matter (1)
- Oxgen (1)
- Paint and Protective coatings (32)
- Paint specification (1)
- pcs certification (1)
- Personal Protective Equipment (3)
- Petrochemical Plant Fireproofing Methods (1)
- Petrochemical Plants (1)
- Pipeline (2)
- Pitting Corrosion (2)
- Pitting Detection (1)
- Polymer-Based Coatings (1)
- Power plant (1)
- Power tools (1)
- PPE (3)
- Print Advertising (1)
- Print Marketing Strategy (1)
- professional certification (2)
- professional development (1)
- Protective Coatings (7)
- protective coatings industry (1)
- protective coatings specialist (1)
- quality assurance (1)
- radiation-resistant materials (1)
- Real-Time Corrosion Monitoring in Oil Fields (1)
- Rebar Corrosion (2)
- rectifier (1)
- Reliability (1)
- Remote monitoring and drones (4)
- Repaint (1)
- Restoration (1)
- ride maintenance (1)
- Risk-Based Inspection (1)
- Road deicers (1)
- Roads and bridges (1)
- Roller coaster (1)
- Rust (1)
- sacrificial anodes (1)
- Safety (5)
- Safety Standards (3)
- Salt pollution (1)
- Sensors (1)
- service awards (2)
- Ship Coatings (9)
- Shiptanks (1)
- Standards (10)
- Standards Committees (2)
- Steel (8)
- Steel Reinforcement (2)
- Stress Corrosion Cracking (1)
- Structural Steel (1)
- study tips (1)
- Surface Preparation (13)
- Sustainability (1)
- Sustainability and corrosion (7)
- terminology (1)
- Tools (1)
- Turbine (1)
- Types of Corrosion (1)
- Ultrasonic Testing (1)
- Uniform Corrosion (1)
- us army core of engineers (1)
- Wastewater Systems (1)
- Water crisis (1)
- Water pipe corrosion (1)
- Water quality (1)
- Water tank coatings (5)
- Water/treatment infrastructure (20)
- Waterway salinity (1)
- Workforce development (1)
- WRDA (1)