Safety Compliance in Abrasive Blasting Operations
July 8, 2024 •AMPP
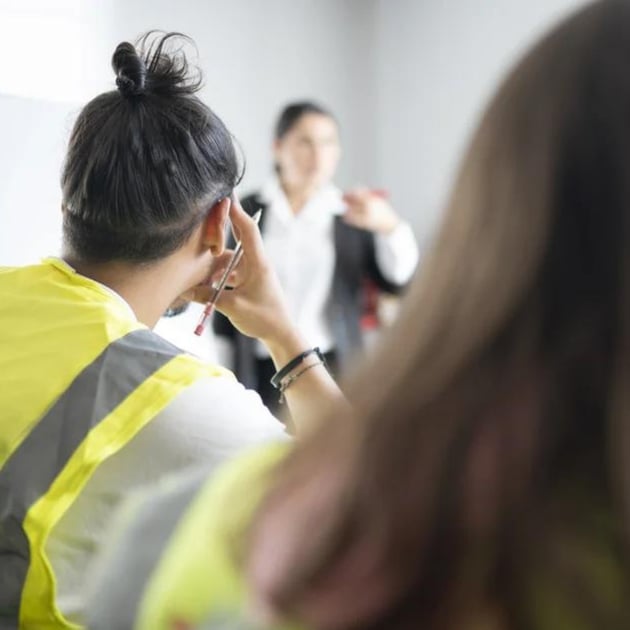
Abrasive blasting uses compressed air or water to direct a high velocity stream of an abrasive material to clean an object or surface, remove burrs, or apply a texture. Blasting materials may include aluminum oxide, steel grit, crushed glass, and garnet. Abrasive blasting is commonly used in the coatings industry to prepare a substrate for painting and other coating applications.
Despite its utility, blasting presents significant hazards to coatings professionals — and not just from the force of the materials themselves. When left unmitigated, these hazards pose the risk of serious injuries to employees and can result in substantial legal and financial consequences for coatings industry employers.
The potential dangers of abrasive blasting are vividly illustrated by the following recent incidents:
• On June 18, 2021, a worker was blasted from a basket inside a tank, and upon exiting the basket, bumped a control valve, causing a stuck-between injury resulting in his death.
• On June 9, 2021, a worker was preparing to blast a 500-pound (226.8 kg) wheel in a blasting booth when the wheel tipped over, striking and killing him.
• On January 29, 2021, a worker was on a scaffold inspecting a water tank for pin holes after blasting when the scaffold collapsed, resulting in a 35-foot (10.7 m) fall to his death.
• On July 1, 2019, a worker was blasting a bridge when a blasting whip came into contact with his hood, breaking the face shield and blasting abrasive particles into his eye, resulting in a serious injury.
• On November 16, 2018, an employee’s hand connected with the rotating fan of a core blaster machine, resulting in the amputation of three of his fingers.
• On April 7, 2018, an employee lost his balance while blasting, resulting in the blasting gun creating a 1-inch (2.5 cm) puncture wound in his arm.
Some of these injuries were avoidable while others were not. However, each incident underscores the need for employers to implement comprehensive safety programs to prevent the risks inherent in abrasive blasting in the field.
Doing so not only helps to prevent injuries but can also mitigate the serious legal and financial consequences resulting from accidents — as high as $161,323 per violation in 2024 per the Occupational Safety and Health Administration (OSHA). Here are three tips on how to engineer these inherent risks out of the jobsite.
1. Assess the risks.
The first critical element of safe abrasive blasting operations involves assessing and appreciating the risks that may be involved. Understanding these risks allows employers to proactively plan and implement effective safety measures that can reduce the chances of catastrophic injury.
Employers should start their safety assessment with a broad review of general risks present in construction and coating operations. For example, fall hazards are present in many construction settings, and they are a leading cause of death in the construction industry.
Likewise, employers should consider risks from the use of vehicles and heavy equipment, which account for a relatively large number of injuries across the industry, regardless of work task.
After accounting for general risks, employers need to assess the specific risks presented by abrasive blasting operations. According to OSHA, blasting presents specific worksite hazards, such as potential exposure to toxic materials through inhalation and contact, loud noises that can damage hearing, and hazards to extremities necessitating the use of personal protective equipment (PPE), such as safety boots, helmets, aprons, and coveralls.
In addition to general safety assessments, employers should prepare a job hazard analysis (JHA) for abrasive blasting tasks. According to OSHA, a JHA is an analysis technique “that focuses on job tasks as a way to identify hazards before they occur. It focuses on the relationship between the worker, the task, the tools, and the work environment.”
Unlike general safety assessments, JHAs examine specific tasks with high rates of injury or risk of significant injuries, and they attempt to determine what could go wrong. Thus, JHAs are appropriate for blasting tasks, particularly when these tasks involve interconnected risks, such as falling hazards and use of hazardous abrasive materials.
2. Plan for safety.
After assessing the risks associated with abrasive blasting, the next critical element for employers is to plan for safe operations. As with assessments, planning should focus on both general risks and site-specific hazards. Additionally, planning should be comprehensive and continuous throughout the company’s general and project-specific operations.
As a first step, construction and coatings employers should adopt a comprehensive safety manual. This manual serves as the foundation for safe operations and related programs and policies. Safety manuals provide employees and managers with training about each of the hazards they may face in their work environment, identifying the risks and mandatory control measures.
Additionally, safety manuals are intended to address all of the employer’s safety-related topics, such as the delegation of managerial safety responsibilities, employee training programs, emergency response plans, and other key safety information. A physical copy of the manual should be distributed to each employee at onboarding and available for reference at company jobsites. The characteristics of a good safety manual are markups, notes, highlights, and worn pages from continual reference and use. Additionally, the manual should be updated regularly as employers identify new risks and adapt to lessons learned from earlier projects.
Manuals for companies using abrasive blasting should address the following topics, among others:
• Ventilation, respiratory protection, and silica hazards
• Occupational noise exposure and hearing protection
• PPE
• Occupational sanitation
Some of these topics are not merely recommended but required by OSHA standards, such as the mandate for employer hearing conservation programs imposed under 29 CFR 1910.95(c).
Aside from general plans set out in safety manuals, employers should approach each abrasive blasting project by developing a site-specific safety plan (SSSP). Unlike general plans and policies, SSSPs focus on the unique hazards and challenges that may be present at an individual project.
For example, a plan for an abrasive blasting project involving an abrasive that has the potential to be particularly toxic will identify the risks associated with that material and outline administrative and engineering controls for exposure.
Additionally, this plan could mandate refresher training that workers must receive regarding the use of the potentially toxic material before starting work.
3. Implement the plan.
The third, most critical, and most difficult element of safe abrasive blasting operations is implementing the safety plan. Indeed, many employers with impressive safety manuals and policies — but no strategy for implementation — have discovered the catastrophic, sometimes fatal, consequences of this deficiency.
From both practical and legal standpoints (where OSHA is concerned), implementation includes three key elements: (a) training, (b) inspection/supervision, and (c) enforcement.
In short, employers and supervisors should be trained and retrained on safety measures. Next, worksites should be supervised and inspected for compliance. Finally, employees who fail to comply with the plan should be retrained, suspended, or terminated. Let’s go into those elements in more detail.
Training. All new workers should receive initial safety training and a copy of the safety manual upon being hired and, critically, before setting foot on a project. Workers who will perform abrasive blasting operations should receive general safety training as well as training on the specific hazards associated with abrasive blasting. These skills should be tested on a written exam to establish understanding and competence. Retraining should occur frequently (ideally, each week, but not less than monthly). Likewise, managers should receive “train-the-trainer” instructions to ensure they are teaching effectively. For legal purposes, employers should document all training occurrences using course materials, rosters, sign-in sheets, and photographs.
Inspection/Supervision. Employers should implement effective supervision and inspection programs to ensure these lessons are actually put to use in the field. Responsible managers should be assigned to, and present at, the project to enforce compliance. Where this is not practical or feasible, a responsible person should be designated, and managers should conduct programmed and random safety inspections to establish a continuous presence and discover violations of safety policy. For legal purposes, the results of all inspections should be documented, including all corrective measures and retraining efforts that were implemented.
Enforcement. Safety violations should be addressed and disciplined through graduating enforcement mechanisms. First, employees and managers who are caught failing to comply should be warned and retrained regarding their violation. Both of these measures should be documented and acknowledged by the employee in writing. If continued violations occur, the manager or employee should be suspended from work and retrained again, with both actions documented in writing. Finally, an employee or manager who does not respond to retraining, warnings, or suspensions should be terminated. Paperwork should accompany the termination that makes clear that the termination resulted directly from the safety violations.
Ideally, these efforts will reduce the risk of employee injuries in construction and abrasive blasting operations. Additionally, in the event of a reportable injury or random OSHA inspection, the efforts will be crucial for establishing that the incident resulted from unpreventable employee misconduct and not the employer’s lack of compliance.
Prioritizing Safety
While abrasive blasting is a powerful technique widely used in the coatings industry, its effectiveness comes with significant hazards in and around the jobsite that can lead to tragic incidents and severe consequences for employees and employers. Countless examples of injuries underscore the importance of proactive safety measures.
Employers who are engaged in abrasive blasting should diligently assess the risks, plan comprehensive safety programs, and implement these plans through rigorous training, inspection, and enforcement.
By prioritizing and being consistent with safety, employers not only protect their workforce but also shield themselves from legal and financial liabilities arising from potential incidents related to abrasive blasting.
The information in this article does not, and is not intended to, constitute legal advice; instead, all information, content, and materials in this article are for general informational purposes only.
Editor’s note: This article By Travis S. McConnell, Construction Attorney with Ready Legal first appeared in the May 2024 print issue of CoatingsPro Magazine. Reprinted with permission. on 6/4/2024 6:54 PM
About the Author:
Travis S. McConnell is a construction attorney with Ready Legal, a business law firm located in Orlando, Fla. His practice focuses on all aspects of construction law, including OSHA defense and compliance, lien and bond claims, defective construction litigation, and contractor licensing. He represents all members of the construction industry, including contractors, subcontractors, suppliers, property owners, and design professionals.
McConnell has been involved in construction for more than a decade, since serving in the U.S. Army as an Engineer Officer and safety leader. For more information, contact: Ready Legal, www.ReadyLegal.net.
Get Updates
Featured Articles
Categories
- 2024 Olympics (1)
- 2024 Water Resource Development Act (1)
- Abrasive Blasting (1)
- Advanced coating materials (9)
- advanced coatings (1)
- Advanced Corrosion Control in Oil and Gas Industry (2)
- Advocacy (3)
- AI (2)
- Aircraft (1)
- Alkanization (1)
- AMPP (4)
- AMPP Annual Conference + Expo (5)
- ampp awards (1)
- ampp certification (2)
- Ampp Chapters (1)
- AMPP conference (1)
- AMPP logo (1)
- Ampp Membership (2)
- Ampp Standards (2)
- ampp training (2)
- Amusement parks (4)
- Architectural (1)
- Architectural Coatings (2)
- argonne national laboratory (1)
- Artificial Intelligence (1)
- Asset integrity (12)
- Asset maintenance (3)
- Asset Protection (1)
- awards (3)
- B2B Marketing (1)
- Bim Software (1)
- Biodeterioration of materials (5)
- Biofouling (4)
- Blasting (1)
- Bridges (4)
- career advancement (3)
- career development (2)
- cathodic protection (2)
- Cathodic Protection-CP (16)
- Ceramic epoxies (1)
- Certification (3)
- certification study guide (1)
- Chemical Injection (1)
- CIP (1)
- Civil Engineering (1)
- clean energy (1)
- Coating inspector (2)
- coating inspector job roles (1)
- Coating inspector jobs (2)
- Coating inspector program (2)
- Coatings (18)
- Coatings Application (3)
- coatings certification (1)
- Coatings failures (2)
- Coatings Industry (2)
- coatings inspection (1)
- Coatings inspector (2)
- Coatings measurement and inspection (9)
- coatings project management (1)
- Coatings Systems (1)
- Cold stress (1)
- Concrete (13)
- Concrete corrosion (1)
- concrete cracking (1)
- Conference and Events (2)
- Corrosion (26)
- Corrosion Basics (5)
- corrosion certification (1)
- Corrosion Control (17)
- Corrosion Control and Management (23)
- Corrosion detection (1)
- corrosion engineering (1)
- Corrosion Essentials (20)
- Corrosion Inspection (1)
- Corrosion Management (1)
- corrosion mitigation (1)
- corrosion of steel (1)
- corrosion policy (1)
- Corrosion Prevention (12)
- corrosion resistance (1)
- corrosion resources (1)
- Corrosion Under Insulation (2)
- cost of corrosion (1)
- Crevice Corrosion (1)
- Cui (2)
- Data Monitoring (1)
- decarbonization (1)
- defense infrastructure (1)
- Department of Defense (4)
- Deposition corrosion (1)
- Dissimilar Metal Corrosion (1)
- Dissolved gases (1)
- DoD (3)
- Education (2)
- EMERG (1)
- Energy industry (9)
- entertainment industry (1)
- Epoxy (3)
- exam preparation (1)
- FBE Application (1)
- FBE Inspection (1)
- Fireproofing (1)
- Flexible coatings (2)
- Flint, Michigan (1)
- Fluoropolymer coating (3)
- Forms of Corrosion (4)
- Freshwater salinization (1)
- Fusion-bonded epoxy (1)
- Galvanic (1)
- Galvanic Corrosion (4)
- General Corrosion (4)
- General Tips (1)
- glossary (1)
- Hand tools (1)
- honoree night (1)
- Industrial Application (3)
- Industrial Safety (3)
- Industry Best Practices (1)
- Industry Standards (2)
- Infrared Thermography (1)
- infrastructure (4)
- Infrastructure Durability (1)
- Inspection (1)
- integrity management (1)
- Intergranular Corrosion (1)
- Intumescent Coatings (1)
- key note speaker (1)
- leader (1)
- Machine Learning (2)
- Maintenance (2)
- Maintenance Best Practices (1)
- Maritime Coatings (11)
- Maritime industry (11)
- Master Painters Institute (2)
- material protection (1)
- materials performance (1)
- materials science (1)
- Membership (2)
- Membership Benefits (2)
- Michio Kaku (1)
- Microbiological forms (1)
- Microbiologically influenced corrosion-MIC (11)
- Military (2)
- Mineral constituents (1)
- MnDOT (1)
- MPI (3)
- mpi awards (1)
- mpi champion awards (1)
- mpi training (1)
- MPI Update (1)
- National Defense Authorization Act (1)
- national security (1)
- Navy (1)
- nickel-based alloys (1)
- Non-Destructive Testing (1)
- nuclear (1)
- nuclear Materials (1)
- nuclear reactor technology (1)
- Oil and Gas (2)
- Oil Fields (1)
- Organic matter (1)
- Oxgen (1)
- Paint and Protective coatings (32)
- Paint specification (1)
- pcs certification (1)
- Personal Protective Equipment (3)
- Petrochemical Plant Fireproofing Methods (1)
- Petrochemical Plants (1)
- Pipeline (2)
- Pitting Corrosion (2)
- Pitting Detection (1)
- Polymer-Based Coatings (1)
- Power plant (1)
- Power tools (1)
- PPE (3)
- Print Advertising (1)
- Print Marketing Strategy (1)
- professional certification (2)
- professional development (1)
- Protective Coatings (7)
- protective coatings industry (1)
- protective coatings specialist (1)
- quality assurance (1)
- radiation-resistant materials (1)
- Real-Time Corrosion Monitoring in Oil Fields (1)
- Rebar Corrosion (2)
- rectifier (1)
- Reliability (1)
- Remote monitoring and drones (4)
- Repaint (1)
- Restoration (1)
- ride maintenance (1)
- Risk-Based Inspection (1)
- Road deicers (1)
- Roads and bridges (1)
- Roller coaster (1)
- Rust (1)
- sacrificial anodes (1)
- Safety (5)
- Safety Standards (3)
- Salt pollution (1)
- Sensors (1)
- service awards (2)
- Ship Coatings (9)
- Shiptanks (1)
- Standards (10)
- Standards Committees (2)
- Steel (8)
- Steel Reinforcement (2)
- Stress Corrosion Cracking (1)
- Structural Steel (1)
- study tips (1)
- Surface Preparation (13)
- Sustainability (1)
- Sustainability and corrosion (7)
- terminology (1)
- Tools (1)
- Turbine (1)
- Types of Corrosion (1)
- Ultrasonic Testing (1)
- Uniform Corrosion (1)
- us army core of engineers (1)
- Wastewater Systems (1)
- Water crisis (1)
- Water pipe corrosion (1)
- Water quality (1)
- Water tank coatings (5)
- Water/treatment infrastructure (20)
- Waterway salinity (1)
- Workforce development (1)
- WRDA (1)