The Basics on Corrosion Surveys
August 19, 2021 •Corrosion CONTROLLED, Corrosion Essentials, CP
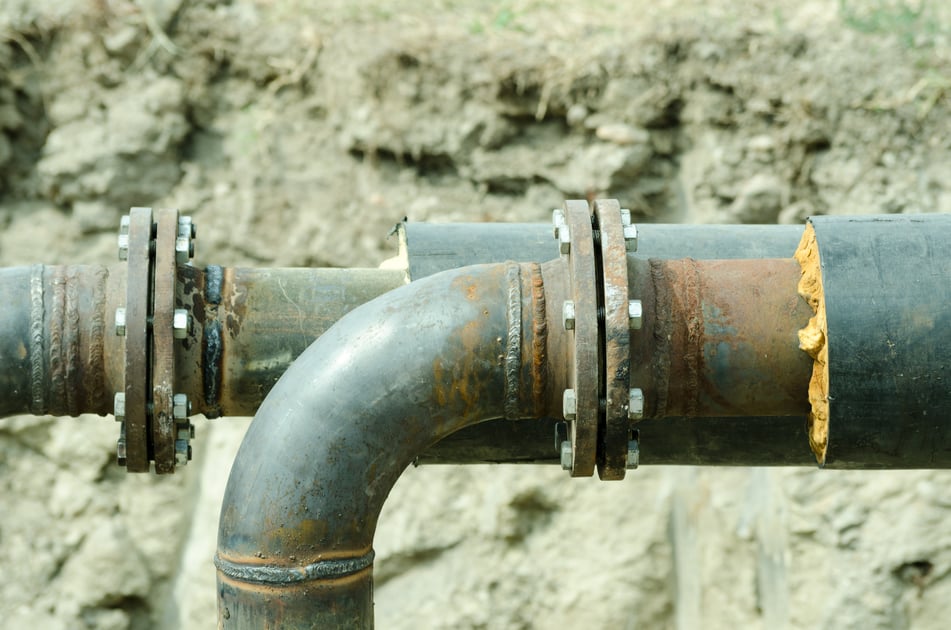
The importance of regular monitoring can not be underestimated in corrosion control. Periodic evaluations, or corrosion surveys, on both cathodic protection (CP) and pipeline coating systems need to be monitored to search for early signs of metal asset corrosion, or worse, a leak on a weak spot on the pipeline.
Corrosion surveys are typically done by examining the asset’s “resistivity,” or how strongly metal resists an electric current. Analyzing an asset’s resistivity and the surrounding soil can pinpoint the areas of the asset that are most likely to become corroded if they aren’t already.
Here’s a quick look at what corrosion surveys entail and why they are important to conduct.
Why do a corrosion survey?
Surveys may be conducted to determine any of these factors:
• How severely a pipeline or other structure is attacked in a proposed location
• How severely an existing structure is being attacked
• How much damage has already been done
Resistivity Surveys
A survey of the resistivity along an existing or proposed route will provide solid answers in determining how severely a pipeline or other structure is attacked in a proposed location (1); how severely an existing structure is being attacked (2); and what steps can be taken to control the corrosive exposure (4). A resistivity survey will also allow for some good estimations to aid in determining how much damage has already been (3).
Except under what can only be described as research conditions, it is seldom profitable to conduct an extensive survey of resistivity along the route of a coated line, either existing or planned. There is only one decision to make about a coated line, and that is whether to place it under cathodic protection (CP).
• If the answer is “no,” then the resistivity data serve no useful purpose
• If it is “yes,” then all that is needed is information about possible anode bed sites, and these should be taken at a greater depth than those for the pipeline corrosion survey
On a bare line, however, a resistivity survey makes a great deal of sense. It assembles data concerning two important problems: it tells where the line is subject to attack (hot spots) and it furnishes data needed for the selection of galvanic anodes of the proper sizes or the amount of impressed current that is likely to be needed.
Many adhere to the belief that any soil that is sufficiently corrosive to justify coating a line also justifies CP. In other words, no line should be coated unless it is also protected. Acceptance of this conclusion, of course, covers the first decision referred to previously, thereby eliminating any justification (except as a research study) for a detailed resistivity survey along a coated line. Instead, a much more limited survey is conducted in conjunction with current requirement tests to obtain the data needed for the design of the CP system.
Potential Surveys
Once the line has been placed under CP, potential surveys, with readings usually at wide spacing using permanent test leads, are needed to ensure complete and continued protection. If trouble occurs and some sections of the line are found to be less than fully protected, then close potential measurements—for• example, 8-m spacing—may be useful in tracking down the difficulty.
A profile of the potential, along the survey of the soil immediately above the pipeline, can be run by any of several methods. Any sharp break in that profile must have an explanation. It may be:
•an uninsulated lateral
• an accidentally shorted crossing line
• a shorted casing
•a sharp change in soil resistivity
•something else
However, it must have some reason for existence, and whatever is causing it may be what is robbing the line of protection.
Corrosion affects nearly every industry, and AMPP's training programs are designed to thoroughly prepare students for the next step in their professional lives, no matter where their career takes them. Learn more.
Source: MaterialsPerformance.com article adapted from Corrosion Basics -- An Introduction, Second Edition, Pierre R. Roberge.
FREE DOWNLOADS
White Paper: An Action Plan for Reducing Pipeline Failures, Costs with Corrosion in the Water Sector
Special Report: The Future of Corrosion Control, Insights from the Experts
Get Updates
Featured Articles
Categories
- 2024 Olympics (1)
- 2024 Water Resource Development Act (1)
- Abrasive Blasting (1)
- Advanced coating materials (9)
- advanced coatings (1)
- Advanced Corrosion Control in Oil and Gas Industry (2)
- Advocacy (3)
- AI (2)
- Aircraft (1)
- Alkanization (1)
- AMPP (4)
- AMPP Annual Conference + Expo (5)
- ampp awards (1)
- ampp certification (2)
- Ampp Chapters (1)
- AMPP conference (1)
- AMPP logo (1)
- Ampp Membership (2)
- Ampp Standards (2)
- ampp training (2)
- Amusement parks (4)
- Architectural (1)
- Architectural Coatings (2)
- argonne national laboratory (1)
- Artificial Intelligence (1)
- Asset integrity (12)
- Asset maintenance (3)
- Asset Protection (1)
- awards (3)
- B2B Marketing (1)
- Bim Software (1)
- Biodeterioration of materials (5)
- Biofouling (4)
- Blasting (1)
- Bridges (4)
- career advancement (3)
- career development (2)
- cathodic protection (2)
- Cathodic Protection-CP (16)
- Ceramic epoxies (1)
- Certification (3)
- certification study guide (1)
- Chemical Injection (1)
- CIP (1)
- Civil Engineering (1)
- clean energy (1)
- Coating inspector (2)
- coating inspector job roles (1)
- Coating inspector jobs (2)
- Coating inspector program (2)
- Coatings (18)
- Coatings Application (3)
- coatings certification (1)
- Coatings failures (2)
- Coatings Industry (2)
- coatings inspection (1)
- Coatings inspector (2)
- Coatings measurement and inspection (9)
- coatings project management (1)
- Coatings Systems (1)
- Cold stress (1)
- Concrete (13)
- Concrete corrosion (1)
- concrete cracking (1)
- Conference and Events (2)
- Corrosion (26)
- Corrosion Basics (5)
- corrosion certification (1)
- Corrosion Control (17)
- Corrosion Control and Management (23)
- Corrosion detection (1)
- corrosion engineering (1)
- Corrosion Essentials (20)
- Corrosion Inspection (1)
- Corrosion Management (1)
- corrosion mitigation (1)
- corrosion of steel (1)
- corrosion policy (1)
- Corrosion Prevention (12)
- corrosion resistance (1)
- corrosion resources (1)
- Corrosion Under Insulation (2)
- cost of corrosion (1)
- Crevice Corrosion (1)
- Cui (2)
- Data Monitoring (1)
- decarbonization (1)
- defense infrastructure (1)
- Department of Defense (4)
- Deposition corrosion (1)
- Dissimilar Metal Corrosion (1)
- Dissolved gases (1)
- DoD (3)
- Education (2)
- EMERG (1)
- Energy industry (9)
- entertainment industry (1)
- Epoxy (3)
- exam preparation (1)
- FBE Application (1)
- FBE Inspection (1)
- Fireproofing (1)
- Flexible coatings (2)
- Flint, Michigan (1)
- Fluoropolymer coating (3)
- Forms of Corrosion (4)
- Freshwater salinization (1)
- Fusion-bonded epoxy (1)
- Galvanic (1)
- Galvanic Corrosion (4)
- General Corrosion (4)
- General Tips (1)
- glossary (1)
- Hand tools (1)
- honoree night (1)
- Industrial Application (3)
- Industrial Safety (3)
- Industry Best Practices (1)
- Industry Standards (2)
- Infrared Thermography (1)
- infrastructure (4)
- Infrastructure Durability (1)
- Inspection (1)
- integrity management (1)
- Intergranular Corrosion (1)
- Intumescent Coatings (1)
- key note speaker (1)
- leader (1)
- Machine Learning (2)
- Maintenance (2)
- Maintenance Best Practices (1)
- Maritime Coatings (11)
- Maritime industry (11)
- Master Painters Institute (2)
- material protection (1)
- materials performance (1)
- materials science (1)
- Membership (2)
- Membership Benefits (2)
- Michio Kaku (1)
- Microbiological forms (1)
- Microbiologically influenced corrosion-MIC (11)
- Military (2)
- Mineral constituents (1)
- MnDOT (1)
- MPI (3)
- mpi awards (1)
- mpi champion awards (1)
- mpi training (1)
- MPI Update (1)
- National Defense Authorization Act (1)
- national security (1)
- Navy (1)
- nickel-based alloys (1)
- Non-Destructive Testing (1)
- nuclear (1)
- nuclear Materials (1)
- nuclear reactor technology (1)
- Oil and Gas (2)
- Oil Fields (1)
- Organic matter (1)
- Oxgen (1)
- Paint and Protective coatings (32)
- Paint specification (1)
- pcs certification (1)
- Personal Protective Equipment (3)
- Petrochemical Plant Fireproofing Methods (1)
- Petrochemical Plants (1)
- Pipeline (2)
- Pitting Corrosion (2)
- Pitting Detection (1)
- Polymer-Based Coatings (1)
- Power plant (1)
- Power tools (1)
- PPE (3)
- Print Advertising (1)
- Print Marketing Strategy (1)
- professional certification (2)
- professional development (1)
- Protective Coatings (7)
- protective coatings industry (1)
- protective coatings specialist (1)
- quality assurance (1)
- radiation-resistant materials (1)
- Real-Time Corrosion Monitoring in Oil Fields (1)
- Rebar Corrosion (2)
- rectifier (1)
- Reliability (1)
- Remote monitoring and drones (4)
- Repaint (1)
- Restoration (1)
- ride maintenance (1)
- Risk-Based Inspection (1)
- Road deicers (1)
- Roads and bridges (1)
- Roller coaster (1)
- Rust (1)
- sacrificial anodes (1)
- Safety (5)
- Safety Standards (3)
- Salt pollution (1)
- Sensors (1)
- service awards (2)
- Ship Coatings (9)
- Shiptanks (1)
- Standards (10)
- Standards Committees (2)
- Steel (8)
- Steel Reinforcement (2)
- Stress Corrosion Cracking (1)
- Structural Steel (1)
- study tips (1)
- Surface Preparation (13)
- Sustainability (1)
- Sustainability and corrosion (7)
- terminology (1)
- Tools (1)
- Turbine (1)
- Types of Corrosion (1)
- Ultrasonic Testing (1)
- Uniform Corrosion (1)
- us army core of engineers (1)
- Wastewater Systems (1)
- Water crisis (1)
- Water pipe corrosion (1)
- Water quality (1)
- Water tank coatings (5)
- Water/treatment infrastructure (20)
- Waterway salinity (1)
- Workforce development (1)
- WRDA (1)