The Basics on Testing Protective Coatings
September 7, 2021 •Corrosion CONTROLLED, Corrosion Essentials, M&I
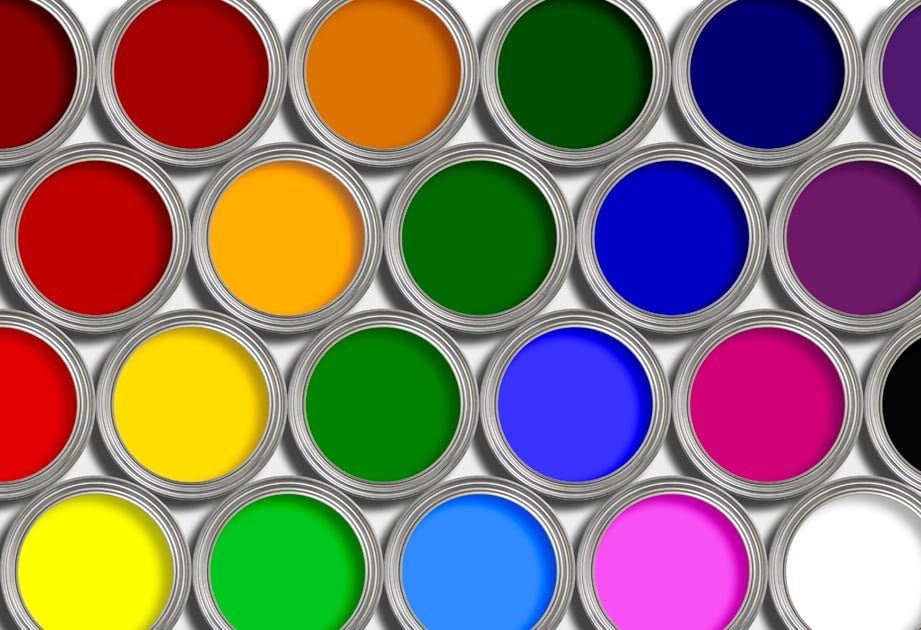
Without historical field performance data, coatings testing programs are the only objective way in which decisions relating to future work can be made. Whether done in-house or contracted out, any type of coating operations must include some type of meaningful test program.
Protective coatings test programs should include the evaluation of:
• materials
• surface preparation
• application
• inspection procedures
Those interested in the operation’s coatings should subscribe to the program and agree on the basis by which decisions are to be made. Whenever possible, standard test procedures and means of evaluation as outlined in standards by NACE International, ASTM, SSPC, and others should be followed. Only in this way can correlation with the results of various workers be made/established.
Basically, there are two main types of tests for coatings subject to atmospheric exposure although, the general approach for buried or submerged coatings is similar.
Field or Service Testing
While delays involved in field or service testing may seem interminably long -- with many cases requiring years for completion of a full-scale field test and hundreds of thousands, if not millions of dollars in coatings expenditures -- it pays to be sure about performance. Most field testing is done on site under the supervision of the customer’s testing staff and involves the following steps.
•Ordinarily, coupons coated with the materials to be tested are exposed in multiples at several test sites in a plant.
• After varying periods of exposure, depending on the design of the test program, coupons are removed from the exposure sites to laboratories where their residual properties are measured. At the end of such a program, it usually is possible to identify the best performance from among a group of coatings similarly exposed. This coating can be applied with some confidence that good service will be obtained.
• As for any other tests, a field test panel and application procedure should be selected to represent common situations or other conditions of interest.
• Once the panel testing is completed, the usual procedure is to apply the most promising two or three candidate materials on tanks or other large metal areas in the plant site, fully realizing that, when proceeding with this step, all surfaces in the field have far from the same exposure. The four quadrants of a tank are different in sunshine exposure, and the top and bottom halves of the tank are not the same because of the internal changes in liquid level.
In any large chemical or industrial plant, corrosivity at one plant location may be more or less severe by several orders of magnitude than the corrosivity at another location. Exposure at a single location may not give results that can be anticipated with confidence everywhere in the plant. Additionally, because some locations are less corrosive than others, they may not require systems as expensive as those used in the most aggressive locations.
Laboratory Testing
The number and types of tests that can be conducted in the laboratory are almost limitless. Because field testing of coatings is so costly in time, labor, and facilities, it has been the persistent aim of the formulators, raw materials producers, and users of coatings to establish meaningful accelerated laboratory tests. These may involve a wide variety of procedures, ranging from comparatively simple to highly sophisticated.
The tests can define certain characteristics of a coating system. This discrimination usually is specific to the type of accelerated test and frequently does not indicate in advance how a given coating will perform in service. Nonetheless, the tests are invaluable when developing a coating or appraising new concepts in coating application or use.
Stay current with the latest protective coating tips, techniques, and technologies with a a free subscription to CoatingsPro Magazine.
Source: MaterialsPerformance.com article adapted from Corrosion Basics -- An Introduction, Second Edition, Pierre R. Roberge.
FREE DOWNLOADS
White Paper: An Action Plan for Reducing Pipeline Failures, Costs with Corrosion in the Water Sector
Special Report: The Future of Corrosion Control, Insights from the Experts
Get Updates
Featured Articles
Categories
- 2024 Olympics (1)
- 2024 Water Resource Development Act (1)
- Abrasive Blasting (1)
- Advanced coating materials (9)
- advanced coatings (1)
- Advanced Corrosion Control in Oil and Gas Industry (2)
- Advocacy (3)
- AI (2)
- Aircraft (1)
- Alkanization (1)
- AMPP (4)
- AMPP Annual Conference + Expo (5)
- ampp awards (1)
- ampp certification (2)
- Ampp Chapters (1)
- AMPP conference (1)
- AMPP logo (1)
- Ampp Membership (2)
- Ampp Standards (2)
- ampp training (2)
- Amusement parks (4)
- Architectural (1)
- Architectural Coatings (2)
- argonne national laboratory (1)
- Artificial Intelligence (1)
- Asset integrity (12)
- Asset maintenance (3)
- Asset Protection (1)
- awards (3)
- B2B Marketing (1)
- Bim Software (1)
- Biodeterioration of materials (5)
- Biofouling (4)
- Blasting (1)
- Bridges (4)
- career advancement (3)
- career development (2)
- cathodic protection (2)
- Cathodic Protection-CP (16)
- Ceramic epoxies (1)
- Certification (3)
- certification study guide (1)
- Chemical Injection (1)
- CIP (1)
- Civil Engineering (1)
- clean energy (1)
- Coating inspector (2)
- coating inspector job roles (1)
- Coating inspector jobs (2)
- Coating inspector program (2)
- Coatings (18)
- Coatings Application (3)
- coatings certification (1)
- Coatings failures (2)
- Coatings Industry (2)
- coatings inspection (1)
- Coatings inspector (2)
- Coatings measurement and inspection (9)
- coatings project management (1)
- Coatings Systems (1)
- Cold stress (1)
- Concrete (13)
- Concrete corrosion (1)
- concrete cracking (1)
- Conference and Events (2)
- Corrosion (26)
- Corrosion Basics (5)
- corrosion certification (1)
- Corrosion Control (17)
- Corrosion Control and Management (23)
- Corrosion detection (1)
- corrosion engineering (1)
- Corrosion Essentials (20)
- Corrosion Inspection (1)
- Corrosion Management (1)
- corrosion mitigation (1)
- corrosion of steel (1)
- corrosion policy (1)
- Corrosion Prevention (12)
- corrosion resistance (1)
- corrosion resources (1)
- Corrosion Under Insulation (2)
- cost of corrosion (1)
- Crevice Corrosion (1)
- Cui (2)
- Data Monitoring (1)
- decarbonization (1)
- defense infrastructure (1)
- Department of Defense (4)
- Deposition corrosion (1)
- Dissimilar Metal Corrosion (1)
- Dissolved gases (1)
- DoD (3)
- Education (2)
- EMERG (1)
- Energy industry (9)
- entertainment industry (1)
- Epoxy (3)
- exam preparation (1)
- FBE Application (1)
- FBE Inspection (1)
- Fireproofing (1)
- Flexible coatings (2)
- Flint, Michigan (1)
- Fluoropolymer coating (3)
- Forms of Corrosion (4)
- Freshwater salinization (1)
- Fusion-bonded epoxy (1)
- Galvanic (1)
- Galvanic Corrosion (4)
- General Corrosion (4)
- General Tips (1)
- glossary (1)
- Hand tools (1)
- honoree night (1)
- Industrial Application (3)
- Industrial Safety (3)
- Industry Best Practices (1)
- Industry Standards (2)
- Infrared Thermography (1)
- infrastructure (4)
- Infrastructure Durability (1)
- Inspection (1)
- integrity management (1)
- Intergranular Corrosion (1)
- Intumescent Coatings (1)
- key note speaker (1)
- leader (1)
- Machine Learning (2)
- Maintenance (2)
- Maintenance Best Practices (1)
- Maritime Coatings (11)
- Maritime industry (11)
- Master Painters Institute (2)
- material protection (1)
- materials performance (1)
- materials science (1)
- Membership (2)
- Membership Benefits (2)
- Michio Kaku (1)
- Microbiological forms (1)
- Microbiologically influenced corrosion-MIC (11)
- Military (2)
- Mineral constituents (1)
- MnDOT (1)
- MPI (3)
- mpi awards (1)
- mpi champion awards (1)
- mpi training (1)
- MPI Update (1)
- National Defense Authorization Act (1)
- national security (1)
- Navy (1)
- nickel-based alloys (1)
- Non-Destructive Testing (1)
- nuclear (1)
- nuclear Materials (1)
- nuclear reactor technology (1)
- Oil and Gas (2)
- Oil Fields (1)
- Organic matter (1)
- Oxgen (1)
- Paint and Protective coatings (32)
- Paint specification (1)
- pcs certification (1)
- Personal Protective Equipment (3)
- Petrochemical Plant Fireproofing Methods (1)
- Petrochemical Plants (1)
- Pipeline (2)
- Pitting Corrosion (2)
- Pitting Detection (1)
- Polymer-Based Coatings (1)
- Power plant (1)
- Power tools (1)
- PPE (3)
- Print Advertising (1)
- Print Marketing Strategy (1)
- professional certification (2)
- professional development (1)
- Protective Coatings (7)
- protective coatings industry (1)
- protective coatings specialist (1)
- quality assurance (1)
- radiation-resistant materials (1)
- Real-Time Corrosion Monitoring in Oil Fields (1)
- Rebar Corrosion (2)
- rectifier (1)
- Reliability (1)
- Remote monitoring and drones (4)
- Repaint (1)
- Restoration (1)
- ride maintenance (1)
- Risk-Based Inspection (1)
- Road deicers (1)
- Roads and bridges (1)
- Roller coaster (1)
- Rust (1)
- sacrificial anodes (1)
- Safety (5)
- Safety Standards (3)
- Salt pollution (1)
- Sensors (1)
- service awards (2)
- Ship Coatings (9)
- Shiptanks (1)
- Standards (10)
- Standards Committees (2)
- Steel (8)
- Steel Reinforcement (2)
- Stress Corrosion Cracking (1)
- Structural Steel (1)
- study tips (1)
- Surface Preparation (13)
- Sustainability (1)
- Sustainability and corrosion (7)
- terminology (1)
- Tools (1)
- Turbine (1)
- Types of Corrosion (1)
- Ultrasonic Testing (1)
- Uniform Corrosion (1)
- us army core of engineers (1)
- Wastewater Systems (1)
- Water crisis (1)
- Water pipe corrosion (1)
- Water quality (1)
- Water tank coatings (5)
- Water/treatment infrastructure (20)
- Waterway salinity (1)
- Workforce development (1)
- WRDA (1)