Study: The Effects of Deep Water on Corrosion and Cathodic Protection
January 5, 2022 •Corrosion CONTROLLED, Corrosion Essentials, CP
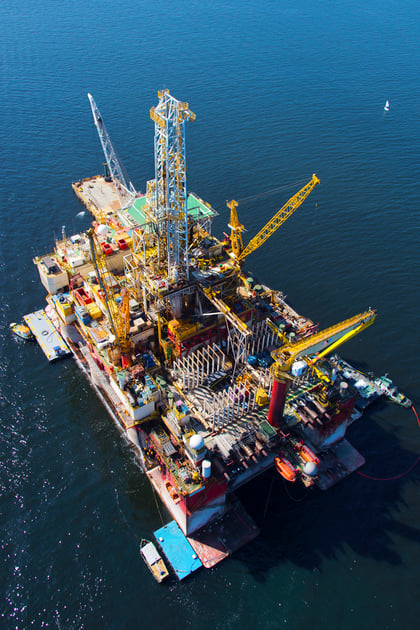
With the continued offshore exploration and recovery of minerals and petroleum, there is need to protect assets used at depths in different oceanic environments. Corrosion prevention mechanisms such as cathodic protection (CP) may be applied to extend asset lifespan or prevent premature, costly failures.
However, there has been a lack of data on how deep water affects CP requirements, according to the French Corrosion Institute (Brest, France). Additionally, the available laboratory results have differed from observations and research in deep water environments, even when conditions are reproduced.
The institute has been conducting a series of studies in Azores in the Atlantic Ocean, including research on the influence of biofilms on cathodic activity and the crevice corrosion of stainless steel (SS) and nickel-based alloys. To investigates these effects, its recent study* exposed CS (ASTM A572 grade 50), as well as corrosion and environmental sensors, for 11 months at depths of 1,020 m (1,115.5 yd) and 2,020 m (2,209.1 yd).
Every 2 h during this time, sensors collected information about the seawater flow velocity, temperature, dissolved oxygen (DO), conductivity, and depth. At the end of the study, the impact of these conditions was studied alongside the corrosion product formed and corrosion rate.
Effects of biofilms on cathodic activity
• The environmental parameters stayed relatively consistent. There were small changes in the current speeds at both depths. The shallower depth had higher temperature and slightly higher flow velocity, but lower DO saturation. The corrosion rate between the two depths was similar, with the 1,020 m depth having a slightly higher rate. The amount of oxygen diffusion may be the reason for this difference—the authors postulate that the higher the temperature, the higher the corrosion rate at a given DO level.
• The current densities (CDs) decreased across time and were slightly lower in the deeper water. This is assumed to be due to the formation of a protective calcareous deposit and the level of oxygen diffusion. The growth of the calcareous deposit, which acted as a physical barrier over the cathode surfaces, was expected to limit oxygen diffusion and current demand over time.
• The makeup of the calcareous deposits was analyzed, and it was found that in the 1,020 m depth, the main compounds were (in decreasing order) magnesium calcite, calcite, and brucite. In the 2,020 m depth, the main compounds were calcite, magnesium calcite, monohydrocalcite, and brucite.
Results from this study were compared to results from other studies that took place in the Arabian Sea and the Indian Ocean. These previous studies used mild steel at different depths and exposure temperatures, finding that corrosion rate was higher in deeper waters. However, the institute instead found a slightly lower corrosion rate in deeper water. Factors such as flow velocity, calcareous deposit formation, and different limiting parameters involved in the electrochemical processes were attributed as the reasons for this difference.
The analysis of the environmental conditions and their effect on corrosion rate and CDs will help to inform future design of appropriate corrosion protection methods used in the Atlantic Ocean.
* Carbon Steel Corrosion and Cathodic Protection Data in Deep North Atlantic Ocean by E. Diler, N. Larché, D. Thierry, Corrosion Journal 76, 11 (2020).
For more maritime insights, look to AMPP's Maritime News.
Source: Originally appeared in AMPP’s Maritime News, authored by Sammy Miles.
FREE DOWNLOADS
White Paper: An Action Plan for Reducing Pipeline Failures, Costs with Corrosion in the Water Sector
Special Report: The Future of Corrosion Control, Insights from the Experts
Get Updates
Featured Articles
Categories
- 2024 Olympics (1)
- 2024 Water Resource Development Act (1)
- Abrasive Blasting (1)
- Advanced coating materials (9)
- advanced coatings (1)
- Advanced Corrosion Control in Oil and Gas Industry (2)
- Advocacy (3)
- AI (2)
- Aircraft (1)
- Alkanization (1)
- AMPP (4)
- AMPP Annual Conference + Expo (5)
- ampp awards (1)
- ampp certification (2)
- Ampp Chapters (1)
- AMPP conference (1)
- AMPP logo (1)
- Ampp Membership (2)
- Ampp Standards (2)
- ampp training (2)
- Amusement parks (4)
- Architectural (1)
- Architectural Coatings (2)
- argonne national laboratory (1)
- Artificial Intelligence (1)
- Asset integrity (12)
- Asset maintenance (3)
- Asset Protection (1)
- awards (3)
- B2B Marketing (1)
- Bim Software (1)
- Biodeterioration of materials (5)
- Biofouling (4)
- Blasting (1)
- Bridges (4)
- career advancement (3)
- career development (2)
- cathodic protection (2)
- Cathodic Protection-CP (16)
- Ceramic epoxies (1)
- Certification (3)
- certification study guide (1)
- Chemical Injection (1)
- CIP (1)
- Civil Engineering (1)
- clean energy (1)
- Coating inspector (2)
- coating inspector job roles (1)
- Coating inspector jobs (2)
- Coating inspector program (2)
- Coatings (18)
- Coatings Application (3)
- coatings certification (1)
- Coatings failures (2)
- Coatings Industry (2)
- coatings inspection (1)
- Coatings inspector (2)
- Coatings measurement and inspection (9)
- coatings project management (1)
- Coatings Systems (1)
- Cold stress (1)
- Concrete (13)
- Concrete corrosion (1)
- concrete cracking (1)
- Conference and Events (2)
- Corrosion (26)
- Corrosion Basics (5)
- corrosion certification (1)
- Corrosion Control (17)
- Corrosion Control and Management (23)
- Corrosion detection (1)
- corrosion engineering (1)
- Corrosion Essentials (20)
- Corrosion Inspection (1)
- Corrosion Management (1)
- corrosion mitigation (1)
- corrosion of steel (1)
- corrosion policy (1)
- Corrosion Prevention (12)
- corrosion resistance (1)
- corrosion resources (1)
- Corrosion Under Insulation (2)
- cost of corrosion (1)
- Crevice Corrosion (1)
- Cui (2)
- Data Monitoring (1)
- decarbonization (1)
- defense infrastructure (1)
- Department of Defense (4)
- Deposition corrosion (1)
- Dissimilar Metal Corrosion (1)
- Dissolved gases (1)
- DoD (3)
- Education (2)
- EMERG (1)
- Energy industry (9)
- entertainment industry (1)
- Epoxy (3)
- exam preparation (1)
- FBE Application (1)
- FBE Inspection (1)
- Fireproofing (1)
- Flexible coatings (2)
- Flint, Michigan (1)
- Fluoropolymer coating (3)
- Forms of Corrosion (4)
- Freshwater salinization (1)
- Fusion-bonded epoxy (1)
- Galvanic (1)
- Galvanic Corrosion (4)
- General Corrosion (4)
- General Tips (1)
- glossary (1)
- Hand tools (1)
- honoree night (1)
- Industrial Application (3)
- Industrial Safety (3)
- Industry Best Practices (1)
- Industry Standards (2)
- Infrared Thermography (1)
- infrastructure (4)
- Infrastructure Durability (1)
- Inspection (1)
- integrity management (1)
- Intergranular Corrosion (1)
- Intumescent Coatings (1)
- key note speaker (1)
- leader (1)
- Machine Learning (2)
- Maintenance (2)
- Maintenance Best Practices (1)
- Maritime Coatings (11)
- Maritime industry (11)
- Master Painters Institute (2)
- material protection (1)
- materials performance (1)
- materials science (1)
- Membership (2)
- Membership Benefits (2)
- Michio Kaku (1)
- Microbiological forms (1)
- Microbiologically influenced corrosion-MIC (11)
- Military (2)
- Mineral constituents (1)
- MnDOT (1)
- MPI (3)
- mpi awards (1)
- mpi champion awards (1)
- mpi training (1)
- MPI Update (1)
- National Defense Authorization Act (1)
- national security (1)
- Navy (1)
- nickel-based alloys (1)
- Non-Destructive Testing (1)
- nuclear (1)
- nuclear Materials (1)
- nuclear reactor technology (1)
- Oil and Gas (2)
- Oil Fields (1)
- Organic matter (1)
- Oxgen (1)
- Paint and Protective coatings (32)
- Paint specification (1)
- pcs certification (1)
- Personal Protective Equipment (3)
- Petrochemical Plant Fireproofing Methods (1)
- Petrochemical Plants (1)
- Pipeline (2)
- Pitting Corrosion (2)
- Pitting Detection (1)
- Polymer-Based Coatings (1)
- Power plant (1)
- Power tools (1)
- PPE (3)
- Print Advertising (1)
- Print Marketing Strategy (1)
- professional certification (2)
- professional development (1)
- Protective Coatings (7)
- protective coatings industry (1)
- protective coatings specialist (1)
- quality assurance (1)
- radiation-resistant materials (1)
- Real-Time Corrosion Monitoring in Oil Fields (1)
- Rebar Corrosion (2)
- rectifier (1)
- Reliability (1)
- Remote monitoring and drones (4)
- Repaint (1)
- Restoration (1)
- ride maintenance (1)
- Risk-Based Inspection (1)
- Road deicers (1)
- Roads and bridges (1)
- Roller coaster (1)
- Rust (1)
- sacrificial anodes (1)
- Safety (5)
- Safety Standards (3)
- Salt pollution (1)
- Sensors (1)
- service awards (2)
- Ship Coatings (9)
- Shiptanks (1)
- Standards (10)
- Standards Committees (2)
- Steel (8)
- Steel Reinforcement (2)
- Stress Corrosion Cracking (1)
- Structural Steel (1)
- study tips (1)
- Surface Preparation (13)
- Sustainability (1)
- Sustainability and corrosion (7)
- terminology (1)
- Tools (1)
- Turbine (1)
- Types of Corrosion (1)
- Ultrasonic Testing (1)
- Uniform Corrosion (1)
- us army core of engineers (1)
- Wastewater Systems (1)
- Water crisis (1)
- Water pipe corrosion (1)
- Water quality (1)
- Water tank coatings (5)
- Water/treatment infrastructure (20)
- Waterway salinity (1)
- Workforce development (1)
- WRDA (1)