The Value of a Corrosion Management System – in 500 Words or Less
June 22, 2021 •Corrosion CONTROLLED, Corrosion Management
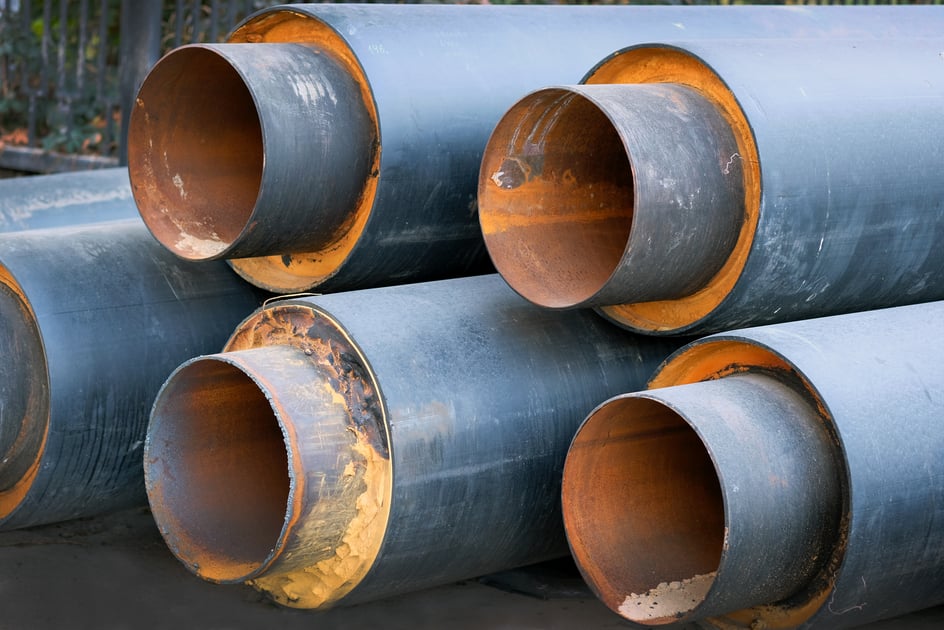
A few years back, NACE International and the NACE Institute (now the Association for Materials Protection and Performance following combining with SSPC: The Society for Protective Coatings) conducted extensive research to determine best corrosion management practices throughout organizations that would ensure safer, long-lasting protection of assets such as pipelines; increase return on investment (ROI) while decreasing life cycle costs; and preserve the environment.
The International Measures of Prevention, Application, and Economics of Corrosion Technologies (IMPACT) Study assessed global corrosion management practices, and a resultant tool from the study, IMPACT PLUS, allows organizations to assess where they are and develop a roadmap for improving their corrosion management programs.
Shortly following the release of the two-year-long study, three experts in oil and gas pipeline corrosion management explained to NACE’s Materials Performance magazine the value of employing a corrosion management system (CMS) in that industry.
Gerry Koch, DNV GL
The greatest benefit, in my opinion, is that with a properly implemented corrosion management program, corrosion decisions and practices can be integrated within an organizational management system. The organization as a whole must commit to the ownership of the CMS and its processes, which means that buy-in at all levels of the organization must exist (i.e., buy-in at both the top and bottom of the organization). Once everyone is “on board” and corrosion has become a culture within the organization, corrosion control and management can be treated as an investment rather than merely an expense, and proper appropriation of funding can be made. This allows the optimization of corrosion management maintaining the integrity of assets while achieving a high ROI.
Dr. Koch is Senior Principal Engineer in the Pipeline Department at DNV GL (US) in Columbus, Ohio. His work focuses on corrosion and asset integrity management. A NACE Fellow, he has published over 90 technical papers, co-authored four books, and holds one patent.
David Kroon, Aegion Corporation
The greatest value is to reap the full financial benefit of compliance with corrosion control and asset integrity regulations while operating in a safe and environmentally responsible manner.
The IMPACT Study was published by NACE International in 2016. The global cost of corrosion was researched and estimated to be $2.5 trillion, or 3.4% of the GDP by country. Most important was that it was demonstrated that 15 to 35% of the cost of corrosion could be saved using currently available corrosion control technologies and practices. Unlike some of the earlier cost of corrosion studies, this work included an evaluation of industry best practices for managing corrosion to reduce operating costs and enhance safety and environmental protection. For the oil and gas pipeline industry, the application of sound corrosion management principles can significantly reduce costs. One of the key areas to address are performance indicators to measure the financial impact of corrosion management. Operational data analysis and corrosion management over the life of the asset are essential.
David H. Kroon, P.E. is Chief Technical Officer for Aegion Corporation in Houston, Texas. He has over 47 years of experience in corrosion prevention and asset integrity management in the oil and gas industry. Throughout his career, he has been actively engaged in solving corrosion problems and extending the life of infrastructure for the energy, water, and transportation industries.
Michael Ames, Chapman Engineering
In my experience, most pipeline companies have well-developed corrosion procedures that enable their work staff in the field to control corrosion. For the most part, these procedures are intended to not only protect their assets, but also to meet or exceed regulations concerning pipeline safety both for gas or liquid pipelines. However, for many there is little or no extension of these procedural links to other departments of the company. There are missing opportunities to involve every part of the company to understand their impact to pipeline safety and corrosion management. This is a part of a “silo” mentality in that other parts of the company do not know how they may impact corrosion management, as it has never been discussed or explained. Even essential links such as the engineering/construction groups may not have direct connection with operations and technical management in the important aspects of each group’s involvement in the life cycle implications of corrosion management of the assets they all touch. IMPACT PLUS and specifically, its Corrosion Management Maturity Model (CMMM) clearly shows those links and provides tools to connect them together into the important wholistic approach to a mature corrosion management mode.
Michael Ames has worked in pipeline corrosion control and operations for over 40 years, creating internal and external corrosion management programs. He served with Northern Natural Gas for more than 34 years. Currently Vice President of Chapman Engineering in Boerne, Texas, he has worked with the U.S. DOT, PHMSA, and state agencies in rulemaking, guidance document preparation, and regulatory audit protocols.
Read the study that broke new ground in corrosion management here. Learn of tools that can help you map a path to corrosion management and asset sustainability.
Source: Excerpted from an article originally published in the March 2019 issue of Pipeline & Gas Journal and appeared in Materials Performance.
FREE DOWNLOADS
White Paper: An Action Plan for Reducing Pipeline Failures, Costs with Corrosion in the Water Sector
Special Report: The Future of Corrosion Control, Insights from the Experts
Get Updates
Featured Articles
Categories
- 2024 Olympics (1)
- 2024 Water Resource Development Act (1)
- Abrasive Blasting (1)
- Advanced coating materials (9)
- advanced coatings (1)
- Advanced Corrosion Control in Oil and Gas Industry (2)
- Advocacy (3)
- AI (2)
- Aircraft (1)
- Alkanization (1)
- AMPP (4)
- AMPP Annual Conference + Expo (5)
- ampp awards (1)
- ampp certification (2)
- Ampp Chapters (1)
- AMPP conference (1)
- AMPP logo (1)
- Ampp Membership (2)
- Ampp Standards (2)
- ampp training (2)
- Amusement parks (4)
- Architectural (1)
- Architectural Coatings (2)
- argonne national laboratory (1)
- Artificial Intelligence (1)
- Asset integrity (12)
- Asset maintenance (3)
- Asset Protection (1)
- awards (3)
- B2B Marketing (1)
- Bim Software (1)
- Biodeterioration of materials (5)
- Biofouling (4)
- Blasting (1)
- Bridges (4)
- career advancement (3)
- career development (2)
- cathodic protection (2)
- Cathodic Protection-CP (16)
- Ceramic epoxies (1)
- Certification (3)
- certification study guide (1)
- Chemical Injection (1)
- CIP (1)
- Civil Engineering (1)
- clean energy (1)
- Coating inspector (2)
- coating inspector job roles (1)
- Coating inspector jobs (2)
- Coating inspector program (2)
- Coatings (18)
- Coatings Application (3)
- coatings certification (1)
- Coatings failures (2)
- Coatings Industry (2)
- coatings inspection (1)
- Coatings inspector (2)
- Coatings measurement and inspection (9)
- coatings project management (1)
- Coatings Systems (1)
- Cold stress (1)
- Concrete (13)
- Concrete corrosion (1)
- concrete cracking (1)
- Conference and Events (2)
- Corrosion (26)
- Corrosion Basics (5)
- corrosion certification (1)
- Corrosion Control (17)
- Corrosion Control and Management (23)
- Corrosion detection (1)
- corrosion engineering (1)
- Corrosion Essentials (20)
- Corrosion Inspection (1)
- Corrosion Management (1)
- corrosion mitigation (1)
- corrosion of steel (1)
- corrosion policy (1)
- Corrosion Prevention (12)
- corrosion resistance (1)
- corrosion resources (1)
- Corrosion Under Insulation (2)
- cost of corrosion (1)
- Crevice Corrosion (1)
- Cui (2)
- Data Monitoring (1)
- decarbonization (1)
- defense infrastructure (1)
- Department of Defense (4)
- Deposition corrosion (1)
- Dissimilar Metal Corrosion (1)
- Dissolved gases (1)
- DoD (3)
- Education (2)
- EMERG (1)
- Energy industry (9)
- entertainment industry (1)
- Epoxy (3)
- exam preparation (1)
- FBE Application (1)
- FBE Inspection (1)
- Fireproofing (1)
- Flexible coatings (2)
- Flint, Michigan (1)
- Fluoropolymer coating (3)
- Forms of Corrosion (4)
- Freshwater salinization (1)
- Fusion-bonded epoxy (1)
- Galvanic (1)
- Galvanic Corrosion (4)
- General Corrosion (4)
- General Tips (1)
- glossary (1)
- Hand tools (1)
- honoree night (1)
- Industrial Application (3)
- Industrial Safety (3)
- Industry Best Practices (1)
- Industry Standards (2)
- Infrared Thermography (1)
- infrastructure (4)
- Infrastructure Durability (1)
- Inspection (1)
- integrity management (1)
- Intergranular Corrosion (1)
- Intumescent Coatings (1)
- key note speaker (1)
- leader (1)
- Machine Learning (2)
- Maintenance (2)
- Maintenance Best Practices (1)
- Maritime Coatings (11)
- Maritime industry (11)
- Master Painters Institute (2)
- material protection (1)
- materials performance (1)
- materials science (1)
- Membership (2)
- Membership Benefits (2)
- Michio Kaku (1)
- Microbiological forms (1)
- Microbiologically influenced corrosion-MIC (11)
- Military (2)
- Mineral constituents (1)
- MnDOT (1)
- MPI (3)
- mpi awards (1)
- mpi champion awards (1)
- mpi training (1)
- MPI Update (1)
- National Defense Authorization Act (1)
- national security (1)
- Navy (1)
- nickel-based alloys (1)
- Non-Destructive Testing (1)
- nuclear (1)
- nuclear Materials (1)
- nuclear reactor technology (1)
- Oil and Gas (2)
- Oil Fields (1)
- Organic matter (1)
- Oxgen (1)
- Paint and Protective coatings (32)
- Paint specification (1)
- pcs certification (1)
- Personal Protective Equipment (3)
- Petrochemical Plant Fireproofing Methods (1)
- Petrochemical Plants (1)
- Pipeline (2)
- Pitting Corrosion (2)
- Pitting Detection (1)
- Polymer-Based Coatings (1)
- Power plant (1)
- Power tools (1)
- PPE (3)
- Print Advertising (1)
- Print Marketing Strategy (1)
- professional certification (2)
- professional development (1)
- Protective Coatings (7)
- protective coatings industry (1)
- protective coatings specialist (1)
- quality assurance (1)
- radiation-resistant materials (1)
- Real-Time Corrosion Monitoring in Oil Fields (1)
- Rebar Corrosion (2)
- rectifier (1)
- Reliability (1)
- Remote monitoring and drones (4)
- Repaint (1)
- Restoration (1)
- ride maintenance (1)
- Risk-Based Inspection (1)
- Road deicers (1)
- Roads and bridges (1)
- Roller coaster (1)
- Rust (1)
- sacrificial anodes (1)
- Safety (5)
- Safety Standards (3)
- Salt pollution (1)
- Sensors (1)
- service awards (2)
- Ship Coatings (9)
- Shiptanks (1)
- Standards (10)
- Standards Committees (2)
- Steel (8)
- Steel Reinforcement (2)
- Stress Corrosion Cracking (1)
- Structural Steel (1)
- study tips (1)
- Surface Preparation (13)
- Sustainability (1)
- Sustainability and corrosion (7)
- terminology (1)
- Tools (1)
- Turbine (1)
- Types of Corrosion (1)
- Ultrasonic Testing (1)
- Uniform Corrosion (1)
- us army core of engineers (1)
- Wastewater Systems (1)
- Water crisis (1)
- Water pipe corrosion (1)
- Water quality (1)
- Water tank coatings (5)
- Water/treatment infrastructure (20)
- Waterway salinity (1)
- Workforce development (1)
- WRDA (1)