Prepare steel surfaces for the best coatings outcome by using these new guidelines
October 7, 2020 •Corrosion CONTROLLED, Corrosion Essentials, Coatings
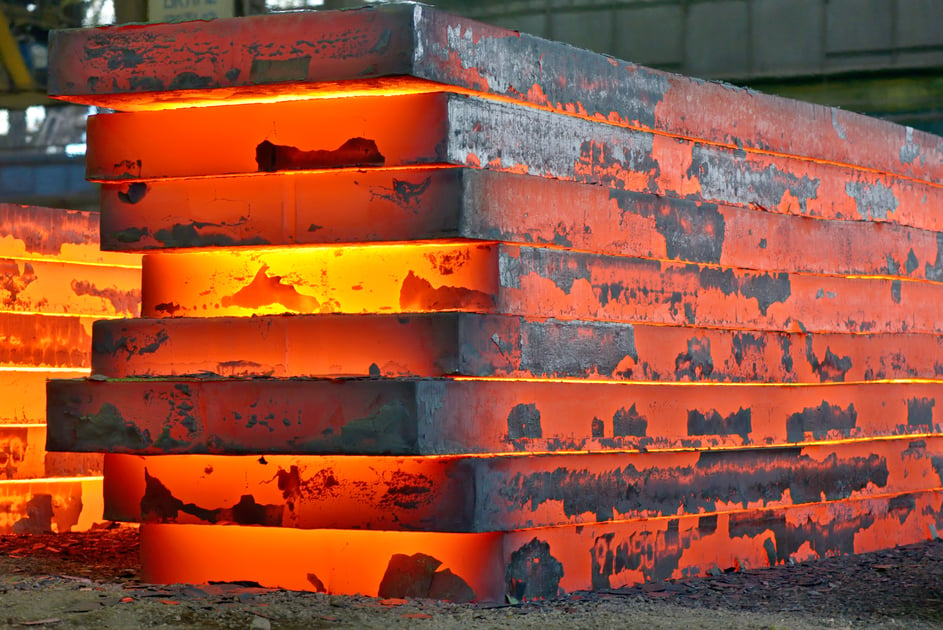
How can you be sure that a metallic surface is well prepped for the best possible coating application outcome? New standards, jointly developed by NACE International and the Society for Protective Coatings (SSPC), offer guidelines for the degrees of surface cleanliness needed to meet job specifications. These wet abrasive blast (WAB) and waterjet (WJ) cleaning surface preparation standards are briefly outlined below and when met, can help ensure the quality coating of steel surfaces.
Wet Abrasive Blast Standards
WAB cleaning uses a mixture of water and abrasive that can produce various levels of surface cleanliness and surface profile (roughness). WAB cleaning may be specified when dust suppression is desired, and it may also be a means for reducing soluble salt contamination.
The NACE/SSPC WAB standards define the process for preparing a carbon steel surface to a specific degree of surface cleanliness using a WAB method of cleaning.
The five degrees of surface cleanliness achieved by a WAB cleaning method are addressed in these individual standards:
White Metal WAB Cleaning This standard defines the process for preparing a carbon steel surface to the white metal degree of surface cleanliness using a WAB cleaning method. White metal WAB cleaning is used when the objective is to remove all rust and other corrosion products, coating, mill scale, and other foreign matter from the surface. It does not permit any staining to remain on the surface. (Standard - NACE WAB-1/SSPC-SP-5, WAB)
Near-White Metal WAB Cleaning This standard defines the process for preparing a carbon steel surface to the near-white metal degree of surface cleanliness using a WAB method. Near-white metal WAB cleaning is used when the objective is to remove all rust and other corrosion products, coating, and mill scale, but when the extra effort required to remove all stains of these materials is determined to be unwarranted. Near-white metal WAB cleaning allows staining on no more than 5 percent of each unit area of surface. (Standard - NACE WAB-2/SSPC-SP 10, WAB)
Commercial WAB Cleaning This standard defines the process for preparing a carbon steel surface to the commercial degree of surface cleanliness using WAB cleaning. Commercial WAB cleaning is used when the objective is to remove all rust, coating, and mill scale, but when the extra effort required to remove all stains of these materials is determined to be unwarranted. Commercial WAB cleaning allows staining on no more than 33 percent of each unit area of surface. (Standard - NACE WAB-3/SSPC-SP 6 WAB)
Brush-Off WAB Cleaning This standard defines the process for preparing a carbon steel surface to the brush-off degree of surface cleanliness using a WAB method of cleaning. The objective of a brush-off WAB cleaning is to allow as much of an existing adherent coating to remain as possible and to roughen the surface before coating application. (Standard - NACE WAB-4/SSPC-SP 7, WAB)
Industrial WAB Cleaning This standard defines the process for preparing a carbon steel surface to the industrial degree of surface cleanliness using WAB cleaning. Industrial WAB cleaning allows tightly adherent paint, mill scale, and rust to remain on no more than 10 percent of each unit area of surface. (Standard - NACE WAB-8/SSPC-SP 14, WAB)
Waterjet Cleaning Standards
WJ is the use of pressurized surface preparation water for removing coatings and other materials, including hazardous materials from a substrate, to achieve a defined degree of surface cleanliness. WJ includes various methods, such as low-pressure water cleaning (LP WC), high-pressure water cleaning (HP WC), high-pressure waterjetting (HP WJ), and ultrahigh-pressure waterjetting (UHP WJ).
WJ does not provide the primary anchor pattern on the metallic substrate known as “surface profile.” The coatings industry uses WJ primarily for recoating or relining projects in which there is an adequate pre-existing surface profile. The degrees of surface cleanliness to be achieved by WJ methods are not intended to require that a surface profile be present or defined prior to coating application.
WJ reduces and may completely remove water-soluble surface contaminants, notably those contaminants found at the bottom of pits on the surface of corroded metallic substrates. WJ also helps remove oil, grease, rust and other corrosion products, and other foreign matter (e.g., shotcrete spatter) from the surface, and it is used when it is a more feasible method of surface preparation than, for example, abrasive blast cleaning, power or hand tool cleaning, or chemical stripping. It may be used when the application of high-performance coatings requires extensive surface preparation, surface decontamination, or both.
The waterjet standards define a standard degree of surface cleanliness to be achieved by WJ methods.
The four degrees of surface cleanliness achieved by WJ are addressed in these separate standards:
Clean to Bare Substrate This standard defines the clean to bare substrate degree of surface cleanliness of coated or uncoated metallic substrates achieved by the use of WJ before the application of a protective coating or lining. WJ to achieve clean to bare substrate (WJ-1) surface cleanliness is used when the objective is to remove every trace of rust and other corrosion products, coating, and mill scale. Discoloration of the surface may be present. (Standard – NACE WJ-1/SSPC-SP, WJ-1)
Very Thorough Cleaning This standard defines the very thorough cleaning degree of surface cleanliness of coated or uncoated metallic substrates achieved by the use of WJ before the application of a protective coating or lining. WJ to achieve very thorough cleaning (WJ-2) surface cleanliness is used when the objective is to remove almost all rust and other corrosion products, coating, and mill scale, but when the extra effort required to remove all of these materials is determined to be unwarranted. Discoloration of the surface may be present. (Standard – NACE WJ-2/SSPC-SP, WJ-2)
Thorough Cleaning This standard defines the thorough cleaning degree of surface cleanliness of coated or uncoated metallic substrates achieved by the use of WJ before the application of a protective coating or lining. WJ to achieve thorough cleaning (WJ-3) surface cleanliness is used when the objective is to remove much of the rust and other corrosion products, coating, and mill scale, and leave tightly adherent thin films, but when the extra effort required to remove almost all of these materials is determined to be unwarranted. Discoloration of the surface may be present. (Standard – NACE WJ-3/SSPC-SP, WJ-3)
Light Cleaning This standard defines the light cleaning degree of surface cleanliness of coated or uncoated metallic substrates achieved by the use of WJ before the application of a protective coating or lining. WJ to achieve light cleaning (WJ-4) surface cleanliness is used when the objective is to allow as much of the tightly adherent rust and other corrosion products, coating, and mill scale to remain as possible, but when the extra effort required to remove more of these materials is determined to be unwarranted. Discoloration of the surface may be present. (Standard – NACE WJ-4/SSPC-SP, WJ-4)
For more coatings tips as well as the latest techniques and technologies in the industry, sign up for NACE’s CoatingsPro Magazine. Subscriptions are FREE.
Source: Originally published in CoatingsPro Magazine, Steel Supplement, authored by Trudy Schreiner, Committee Liaison and Standards Editor for NACE International.
FREE DOWNLOADS
White Paper: An Action Plan for Reducing Pipeline Failures, Costs with Corrosion in the Water Sector
Special Report: The Future of Corrosion Control, Insights from the Experts
Get Updates
Featured Articles
Categories
- 2024 Olympics (1)
- 2024 Water Resource Development Act (1)
- Abrasive Blasting (1)
- Advanced coating materials (9)
- advanced coatings (1)
- Advanced Corrosion Control in Oil and Gas Industry (2)
- Advocacy (3)
- AI (2)
- Aircraft (1)
- Alkanization (1)
- AMPP (4)
- AMPP Annual Conference + Expo (5)
- ampp awards (1)
- ampp certification (2)
- Ampp Chapters (1)
- AMPP conference (1)
- AMPP logo (1)
- Ampp Membership (2)
- Ampp Standards (2)
- ampp training (2)
- Amusement parks (4)
- Architectural (1)
- Architectural Coatings (2)
- argonne national laboratory (1)
- Artificial Intelligence (1)
- Asset integrity (12)
- Asset maintenance (3)
- Asset Protection (1)
- awards (3)
- B2B Marketing (1)
- Bim Software (1)
- Biodeterioration of materials (5)
- Biofouling (4)
- Blasting (1)
- Bridges (4)
- career advancement (3)
- career development (2)
- cathodic protection (2)
- Cathodic Protection-CP (16)
- Ceramic epoxies (1)
- Certification (3)
- certification study guide (1)
- Chemical Injection (1)
- CIP (1)
- Civil Engineering (1)
- clean energy (1)
- Coating inspector (2)
- coating inspector job roles (1)
- Coating inspector jobs (2)
- Coating inspector program (2)
- Coatings (18)
- Coatings Application (3)
- coatings certification (1)
- Coatings failures (2)
- Coatings Industry (2)
- coatings inspection (1)
- Coatings inspector (2)
- Coatings measurement and inspection (9)
- coatings project management (1)
- Coatings Systems (1)
- Cold stress (1)
- Concrete (13)
- Concrete corrosion (1)
- concrete cracking (1)
- Conference and Events (2)
- Corrosion (26)
- Corrosion Basics (5)
- corrosion certification (1)
- Corrosion Control (17)
- Corrosion Control and Management (23)
- Corrosion detection (1)
- corrosion engineering (1)
- Corrosion Essentials (20)
- Corrosion Inspection (1)
- Corrosion Management (1)
- corrosion mitigation (1)
- corrosion of steel (1)
- corrosion policy (1)
- Corrosion Prevention (12)
- corrosion resistance (1)
- corrosion resources (1)
- Corrosion Under Insulation (2)
- cost of corrosion (1)
- Crevice Corrosion (1)
- Cui (2)
- Data Monitoring (1)
- decarbonization (1)
- defense infrastructure (1)
- Department of Defense (4)
- Deposition corrosion (1)
- Dissimilar Metal Corrosion (1)
- Dissolved gases (1)
- DoD (3)
- Education (2)
- EMERG (1)
- Energy industry (9)
- entertainment industry (1)
- Epoxy (3)
- exam preparation (1)
- FBE Application (1)
- FBE Inspection (1)
- Fireproofing (1)
- Flexible coatings (2)
- Flint, Michigan (1)
- Fluoropolymer coating (3)
- Forms of Corrosion (4)
- Freshwater salinization (1)
- Fusion-bonded epoxy (1)
- Galvanic (1)
- Galvanic Corrosion (4)
- General Corrosion (4)
- General Tips (1)
- glossary (1)
- Hand tools (1)
- honoree night (1)
- Industrial Application (3)
- Industrial Safety (3)
- Industry Best Practices (1)
- Industry Standards (2)
- Infrared Thermography (1)
- infrastructure (4)
- Infrastructure Durability (1)
- Inspection (1)
- integrity management (1)
- Intergranular Corrosion (1)
- Intumescent Coatings (1)
- key note speaker (1)
- leader (1)
- Machine Learning (2)
- Maintenance (2)
- Maintenance Best Practices (1)
- Maritime Coatings (11)
- Maritime industry (11)
- Master Painters Institute (2)
- material protection (1)
- materials performance (1)
- materials science (1)
- Membership (2)
- Membership Benefits (2)
- Michio Kaku (1)
- Microbiological forms (1)
- Microbiologically influenced corrosion-MIC (11)
- Military (2)
- Mineral constituents (1)
- MnDOT (1)
- MPI (3)
- mpi awards (1)
- mpi champion awards (1)
- mpi training (1)
- MPI Update (1)
- National Defense Authorization Act (1)
- national security (1)
- Navy (1)
- nickel-based alloys (1)
- Non-Destructive Testing (1)
- nuclear (1)
- nuclear Materials (1)
- nuclear reactor technology (1)
- Oil and Gas (2)
- Oil Fields (1)
- Organic matter (1)
- Oxgen (1)
- Paint and Protective coatings (32)
- Paint specification (1)
- pcs certification (1)
- Personal Protective Equipment (3)
- Petrochemical Plant Fireproofing Methods (1)
- Petrochemical Plants (1)
- Pipeline (2)
- Pitting Corrosion (2)
- Pitting Detection (1)
- Polymer-Based Coatings (1)
- Power plant (1)
- Power tools (1)
- PPE (3)
- Print Advertising (1)
- Print Marketing Strategy (1)
- professional certification (2)
- professional development (1)
- Protective Coatings (7)
- protective coatings industry (1)
- protective coatings specialist (1)
- quality assurance (1)
- radiation-resistant materials (1)
- Real-Time Corrosion Monitoring in Oil Fields (1)
- Rebar Corrosion (2)
- rectifier (1)
- Reliability (1)
- Remote monitoring and drones (4)
- Repaint (1)
- Restoration (1)
- ride maintenance (1)
- Risk-Based Inspection (1)
- Road deicers (1)
- Roads and bridges (1)
- Roller coaster (1)
- Rust (1)
- sacrificial anodes (1)
- Safety (5)
- Safety Standards (3)
- Salt pollution (1)
- Sensors (1)
- service awards (2)
- Ship Coatings (9)
- Shiptanks (1)
- Standards (10)
- Standards Committees (2)
- Steel (8)
- Steel Reinforcement (2)
- Stress Corrosion Cracking (1)
- Structural Steel (1)
- study tips (1)
- Surface Preparation (13)
- Sustainability (1)
- Sustainability and corrosion (7)
- terminology (1)
- Tools (1)
- Turbine (1)
- Types of Corrosion (1)
- Ultrasonic Testing (1)
- Uniform Corrosion (1)
- us army core of engineers (1)
- Wastewater Systems (1)
- Water crisis (1)
- Water pipe corrosion (1)
- Water quality (1)
- Water tank coatings (5)
- Water/treatment infrastructure (20)
- Waterway salinity (1)
- Workforce development (1)
- WRDA (1)