Fluoropolymer topcoat offers steel structures decades-long resistance to weathering, water
August 18, 2020 •Corrosion CONTROLLED, Advanced Materials
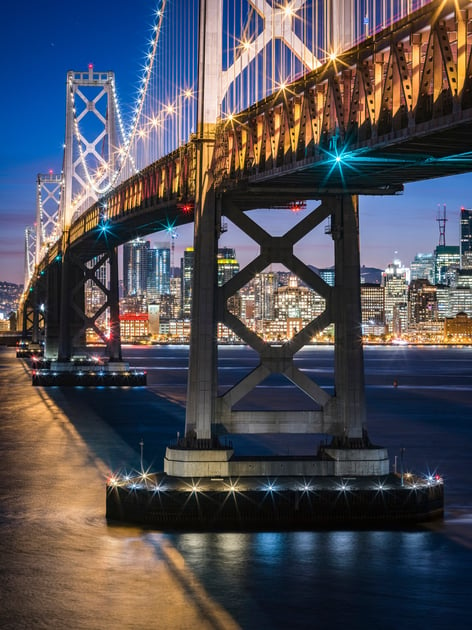
Ambient-cure-type fluoropolymer topcoats were invented in the beginning of the 1980s, and since then, coating systems using fluoropolymer as a topcoat have been applied to a variety of steel and concrete structures. In marine atmospheric environments, the protective performance of coating systems using this advanced material has been demonstrated to be outstanding with fluoropolymer topcoats being adopted in some international standards.
Today, less maintenance, low volatile organic compounds (VOC) content, and low life-cycle costs for coating applications are strong requirements in the global market with respect to the construction of major structures such as long bridges, sky towers, and high-rise buildings. VOC reductions are expected to keep coatings environmentally friendly throughout their service life.
In Japan, several bridges located in marine environments were treated with fluoropolymer topcoat systems: the Ohnaruto Bridge, which is 1,629 m (5,344 ft) in length and the landmark Akashi Strait Bridge, which is 3,911 m (12,831 ft) in length. Their resistance to weathering was superior to other traditional coatings over a 30-year period.
Long-term, outdoor exposure testing of coated panels found fluoropolymer topcoats to be the best for harsh environments. Gloss retention during outdoor exposure service was measured and the surface of each sample was observed using optical microscopy and scanning electron microscopy (SEM). The surface and the cross section were also analyzed by fourier-transform infrared (FTIR) spectroscopy to investigate surface degradation based on chemistry.
Ambient-cure fluoroethylene vinyl ether (FEVE) systems were developed as highly durable polymers for topcoat applications. These comprise regularly alternating fluoroethylene and vinyl-ether segments. While FEVE resins derive their durability from the strong C-F bonds, the regularly alternating sequence contributes to its high level of durability, as compared with conventional polymers such as acrylics.
Table 1 shows the bond energies of the fluoropolymer compound compared with conventional polyurethane (commodity) compounds. The bond energies found in the alternating copolymer of the FEVE resin are higher than the energy in natural ultraviolet (UV) light. This property makes the fluoropolymer resistant to decomposition by natural UV radiation. When UV radiation decomposes a chemical bond, free radicals are formed. These free radicals can initiate degradation of other coating components, including the reacted resin, pigments, and other additives. Generation of these free radicals in the FEVE resin is very difficult. Therefore, the degradation of the crosslinked FEVE coating, which contains several types of chemical bonds, is more difficult.
The S/B FEVE topcoat system and the conventional S/B polyurethane coating systems underwent 30-year exposure in a C5 class environment at Suruga Bay, Japan, which is characterized by 17.4°C (63.3 °F) average temperature and 69% average relative humidity. The tested systems are shown in Table 2, and the results of 20-year exposure to corrosivity category C5 in accordance with ISO 12944 are shown in Figures 1 and 2.
The FEVE topcoat system showed better weathering resistance after 20 years of exposure when compared to the conventional polyurethane topcoat coating system. Cross sections of the tested coatings were evaluated by gloss retention (%) to measure the 60-degree gloss, and then chalking R.N.5 to check the degree of in-service degradation for both topcoats. There was a significant difference between the in-service degradation of the two topcoats (Figures 1 and 2).
The gloss retention of the FEVE topcoats gradually decreased, but there was no chalking. On the other hand, the gloss retention of polyurethane topcoats was drastically reduced, and chalking was significant. The FEVE topcoats are thought to have little film thickness loss because there was no chalking.
Summary
Since the invention of solvent-borne (S/B) FEVE-type fluoropolymer coatings much data has been gathered on the performance of these systems on steel structures. The performances of FEVE systems were excellent after 30 years of outdoor exposure. The FEVE topcoats are highly resistant toward exposure to UV rays, where they significantly outperform the conventional polyurethane topcoats in terms of gloss retention and chalking. These characteristics of fluoropolymers come from the strong chemical bonding between carbon and fluorine atoms in the molecular structure of FEVE.
Industry progress of FEVE-type fluoropolymer as topcoat:
• Because of its outstanding and desirable properties, the Japan Road Association specified the FEVE topcoat system for C5 class service (i.e., atmospheric corrosivity category type environments as defined by ISO 12944-2 and ISO 9223).
• The FEVE fluoropolymer was also included in the ISO 12944-5-2018 standard.
• In recent years, FEVE waterborne (W/B) paints used only as topcoats, as well as full systems composed of an epoxy-zincrich primer and an epoxy intermediate coat, were developed and specified for road bridges by the Tokyo metropolitan government.
• In 1985, extensive testing of FEVE topcoat coatings was initiated at a national institution to verify their performance in the exposure of service under corrosivity category C5 of ISO 12944.
• In 2014, following successful testing, it was adopted by the Japan Road Association for the specification of C5 class service.
For more information on advanced coatings, watch these webcasts on demand at CoatingsPro Magazine:
-Polyurea Technology: Common Failures, Fixes, & Everything In Between
-Advantages of Polyurea Installed Panels vs HDP3
Source: Originally appeared in NACE International’s Maritime News, Spring 2020, as “Fluoropolymer Topcoat: 30-Year-Old Bridge Coatings and Weathering Performance” by Hiroyuki Tanabe, G Protective Coating Research Laboratory at Dai Nippon Toryo Co.
FREE DOWNLOADS
White Paper: An Action Plan for Reducing Pipeline Failures, Costs with Corrosion in the Water Sector
Special Report: The Future of Corrosion Control, Insights from the Experts
Get Updates
Featured Articles
Categories
- 2024 Olympics (1)
- 2024 Water Resource Development Act (1)
- Abrasive Blasting (1)
- Advanced coating materials (9)
- advanced coatings (1)
- Advanced Corrosion Control in Oil and Gas Industry (2)
- Advocacy (3)
- AI (2)
- Aircraft (1)
- Alkanization (1)
- AMPP (4)
- AMPP Annual Conference + Expo (5)
- ampp awards (1)
- ampp certification (2)
- Ampp Chapters (1)
- AMPP conference (1)
- AMPP logo (1)
- Ampp Membership (2)
- Ampp Standards (2)
- ampp training (2)
- Amusement parks (4)
- Architectural (1)
- Architectural Coatings (2)
- argonne national laboratory (1)
- Artificial Intelligence (1)
- Asset integrity (12)
- Asset maintenance (3)
- Asset Protection (1)
- awards (3)
- Bim Software (1)
- Biodeterioration of materials (5)
- Biofouling (4)
- Blasting (1)
- Bridges (4)
- career advancement (3)
- career development (2)
- cathodic protection (2)
- Cathodic Protection-CP (16)
- Ceramic epoxies (1)
- Certification (3)
- certification study guide (1)
- Chemical Injection (1)
- CIP (1)
- Civil Engineering (1)
- clean energy (1)
- Coating inspector (2)
- coating inspector job roles (1)
- Coating inspector jobs (2)
- Coating inspector program (2)
- Coatings (18)
- Coatings Application (3)
- coatings certification (1)
- Coatings failures (2)
- Coatings Industry (2)
- coatings inspection (1)
- Coatings inspector (2)
- Coatings measurement and inspection (9)
- coatings project management (1)
- Coatings Systems (1)
- Cold stress (1)
- Concrete (13)
- Concrete corrosion (1)
- concrete cracking (1)
- Conference and Events (2)
- Corrosion (26)
- Corrosion Basics (5)
- corrosion certification (1)
- Corrosion Control (17)
- Corrosion Control and Management (23)
- Corrosion detection (1)
- corrosion engineering (1)
- Corrosion Essentials (20)
- Corrosion Inspection (1)
- Corrosion Management (1)
- corrosion mitigation (1)
- corrosion of steel (1)
- corrosion policy (1)
- Corrosion Prevention (12)
- corrosion resistance (1)
- corrosion resources (1)
- Corrosion Under Insulation (2)
- cost of corrosion (1)
- Crevice Corrosion (1)
- Cui (2)
- Data Monitoring (1)
- decarbonization (1)
- defense infrastructure (1)
- Department of Defense (4)
- Deposition corrosion (1)
- Dissimilar Metal Corrosion (1)
- Dissolved gases (1)
- DoD (3)
- Education (2)
- EMERG (1)
- Energy industry (9)
- entertainment industry (1)
- Epoxy (3)
- exam preparation (1)
- FBE Application (1)
- FBE Inspection (1)
- Fireproofing (1)
- Flexible coatings (2)
- Flint, Michigan (1)
- Fluoropolymer coating (3)
- Forms of Corrosion (4)
- Freshwater salinization (1)
- Fusion-bonded epoxy (1)
- Galvanic (1)
- Galvanic Corrosion (4)
- General Corrosion (4)
- General Tips (1)
- glossary (1)
- Hand tools (1)
- honoree night (1)
- Industrial Application (3)
- Industrial Safety (3)
- Industry Best Practices (1)
- Industry Standards (2)
- Infrared Thermography (1)
- infrastructure (4)
- Infrastructure Durability (1)
- Inspection (1)
- integrity management (1)
- Intergranular Corrosion (1)
- Intumescent Coatings (1)
- key note speaker (1)
- leader (1)
- Machine Learning (2)
- Maintenance (2)
- Maintenance Best Practices (1)
- Maritime Coatings (11)
- Maritime industry (11)
- Master Painters Institute (2)
- material protection (1)
- materials performance (1)
- materials science (1)
- Membership (2)
- Membership Benefits (2)
- Michio Kaku (1)
- Microbiological forms (1)
- Microbiologically influenced corrosion-MIC (11)
- Military (2)
- Mineral constituents (1)
- MnDOT (1)
- MPI (3)
- mpi awards (1)
- mpi champion awards (1)
- mpi training (1)
- MPI Update (1)
- National Defense Authorization Act (1)
- national security (1)
- Navy (1)
- nickel-based alloys (1)
- Non-Destructive Testing (1)
- nuclear (1)
- nuclear Materials (1)
- nuclear reactor technology (1)
- Oil and Gas (2)
- Oil Fields (1)
- Organic matter (1)
- Oxgen (1)
- Paint and Protective coatings (32)
- Paint specification (1)
- pcs certification (1)
- Personal Protective Equipment (3)
- Petrochemical Plant Fireproofing Methods (1)
- Petrochemical Plants (1)
- Pipeline (2)
- Pitting Corrosion (2)
- Pitting Detection (1)
- Polymer-Based Coatings (1)
- Power plant (1)
- Power tools (1)
- PPE (3)
- professional certification (2)
- professional development (1)
- Protective Coatings (7)
- protective coatings industry (1)
- protective coatings specialist (1)
- quality assurance (1)
- radiation-resistant materials (1)
- Real-Time Corrosion Monitoring in Oil Fields (1)
- Rebar Corrosion (2)
- rectifier (1)
- Reliability (1)
- Remote monitoring and drones (4)
- Repaint (1)
- Restoration (1)
- ride maintenance (1)
- Risk-Based Inspection (1)
- Road deicers (1)
- Roads and bridges (1)
- Roller coaster (1)
- Rust (1)
- sacrificial anodes (1)
- Safety (5)
- Safety Standards (3)
- Salt pollution (1)
- Sensors (1)
- service awards (2)
- Ship Coatings (9)
- Shiptanks (1)
- Standards (10)
- Standards Committees (2)
- Steel (8)
- Steel Reinforcement (2)
- Stress Corrosion Cracking (1)
- Structural Steel (1)
- study tips (1)
- Surface Preparation (13)
- Sustainability (1)
- Sustainability and corrosion (7)
- terminology (1)
- Tools (1)
- Turbine (1)
- Types of Corrosion (1)
- Ultrasonic Testing (1)
- Uniform Corrosion (1)
- us army core of engineers (1)
- Wastewater Systems (1)
- Water crisis (1)
- Water pipe corrosion (1)
- Water quality (1)
- Water tank coatings (5)
- Water/treatment infrastructure (20)
- Waterway salinity (1)
- Workforce development (1)
- WRDA (1)