Why the Concrete You're Coating Cracks
January 19, 2022 •Corrosion CONTROLLED, Corrosion Essentials, Coatings
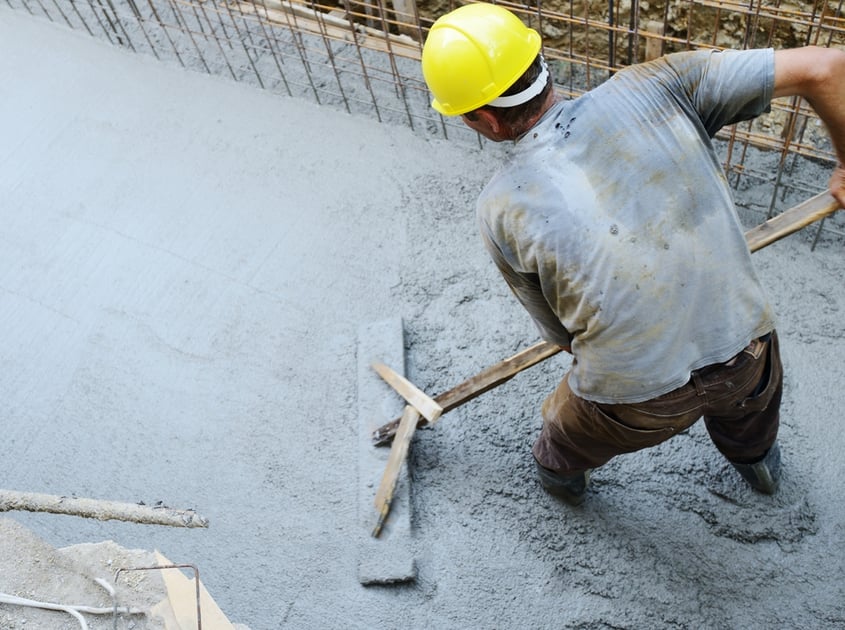
Concrete is by far the most common structural substrate on which resinous flooring materials are applied. Its most basic description: a mixture of cement, various grades and sizes of aggregate, and water. While the makeup of concrete is basic in design, the proper placement, curing, and drying of concrete is an extremely complex process requiring a high degree of expertise.
There are many different mix designs that are used to modify the performance and physical characteristics of concrete. Each design has its pros and cons, but generally, factors that contribute to the amount of concrete cracking include add-mixtures, weather conditions, proper grade selection and compaction, water-to-cement ratios, moisture barriers, proper curing and drying of the concrete, proper layout and cutting of contraction joints (or control joints) and overloading the slab.
And while there is no way to definitively predict when and where concrete will crack, by understanding what caused the crack, flooring contractors can avoid concrete cracking problems.
Top Seven Reasons for Concrete Cracking
The reasons are many but the most common are as follows:
Cracking Due to Corrosion The corrosion of reinforcing rebar and other embedded metals is a major cause of cracking in concrete. As reinforcing steel corrodes, it expands. That creates internal forces that eventually overcome the tensile strength of the concrete, resulting in cracking and other concrete surface failures. Rust can often be seen at the surface and can help in quickly identifying this type of cracking.
Expansion Cracks As with many materials, concrete will expand exponentially as it gets hotter. This expansion can cause immense stress on a concrete floor. As the concrete expands, it pushes against all obstacles in its way. When it comes against an unmovable object, such as another concrete floor, the weaker of the two obstacles will be forced to crack. Designers plan for this by placing expansion joint material -- such as foam, asphalt, and cork -- at the interface between the concrete floor and walls, columns, and other structural components.
Loss of Subbase Support Most often caused when the subbase is washed-out or settles from its original compacted state, loss of support causes an implosion of the concrete slab. Although commonly seen in older slabs, it can be seen in new construction when the concrete form work has been removed too early in the curing stage.
Thermal Cracks Thermal cracks are caused when the temperature increases in the interior portions of the concrete, causing it to expand, while the outside surface of the concrete is cooling, causing it to contract. When the temperature differential between the interior and exterior is too great, consequential tensile stresses can cause thermal cracks at the surface. This kind of cracking is usually seen when concrete is in mass but can also be found in thicker concrete floor pours.
Crazing Cracks Crazing cracks are very common and exhibit themselves as small pattern cracks occurring in a floor slab surface. They are caused when the surface of the concrete floor dries earlier than the underlying concrete. These cracks are usually smaller than 1/8‒1/4-inch (3.2‒6.4 mm) deep and are usually not detrimental to the performance of the concrete.
Plastic Shrinkage Cracks Plastic shrinkage cracks are caused when moisture evaporates faster from the surface of newly poured concrete, and then bleed water comes to the surface to replace the evaporated water. Low humidity, elevated temperatures, and high winds can all play a part in drying out the top of a concrete slab. As the top of the slab dries, it begins to shrink. The underlying concrete, still wet, restrains this shrinkage, causing tensile stress to develop in the weak uppermost part of the concrete surface. This results in shallow cracks of varying depths. These cracks tend to run in parallel with one another, about 1‒3 feet (30.5‒91.4 cm) apart and can be wide at the surface. Normally, they are a cosmetic defect, and if repaired, they are not detrimental to the performance of the concrete floor.
Drying Shrinkage Cracks In its plastic state, concrete gains volume due to the exothermic hydration reaction of cement and the reaction of calcium sulfate and calcium aluminate to form calcium sulfoaluminate. This gain in volume occurs within the first few hours after mixing with water. As the concrete loses moisture and begins to harden, it loses volume and acts much like a wet sponge as it dries. When shrinkage is restrained by contact with the subbase, surrounding structural components (such as walls, columns, steel reinforcement within the concrete, and piping in and through the concrete) tensile stress is developed within the concrete itself.
Concrete, while being strong in compressive strengths, is weak in tensile strength (approximately 10 percent of its compressive strength) and this weakness is greatly tested as the concrete shrinks and literally pulls itself apart. The result is cracking of the concrete at its weakest points.
Designers plan for this by specifying contraction joints at intervals spaced at distances equal to 24 to 30 times the slab thickness and in areas such as re-entrant corners. To be effective in controlling shrinkage cracks, joints must be troweled into the plastic concrete, or cut to a minimum depth of 25 percent of the actual slab thickness before the concrete has already cracked. Usually, this is as soon as it can be walked on without damaging the finish and almost always before 24 hours of placement. Failure to properly weaken the plane at the proper time can result in cracking alongside the planned joint or at random locations.
Conclusion
Crack issues can be a common experience in the flooring business and often results in finger pointing as to who ultimately is responsible for them. Documentation can help in determining responsibility for those that appear after the installation of coatings or overlays.
The American Concrete Institute’s Guide to Design of Slabs-on-Ground, ACI 302 and ACI360R-10, outlines the most current recommendations for constructing concrete floors and slabs. These standards most likely governed the placement of the concrete that you have been hired to coat. Understanding what should and should not have been done when the concrete was placed is extremely important to reducing cracking.
Stay current with the latest protective coating tips, techniques, and technologies with a free subscription to CoatingsPro Magazine.
Source: Article repurposed with permission from CoatingsPro Magazine; written by Chris O’Brien, president and CEO of Rock-Tred Corporation.
FREE DOWNLOADS
White Paper: An Action Plan for Reducing Pipeline Failures, Costs with Corrosion in the Water Sector
Special Report: The Future of Corrosion Control, Insights from the Experts
Get Updates
Featured Articles
Categories
- 2024 Olympics (1)
- 2024 Water Resource Development Act (1)
- Abrasive Blasting (1)
- Advanced coating materials (9)
- advanced coatings (1)
- Advanced Corrosion Control in Oil and Gas Industry (2)
- Advocacy (3)
- AI (2)
- Aircraft (1)
- Alkanization (1)
- AMPP (4)
- AMPP Annual Conference + Expo (5)
- ampp awards (1)
- ampp certification (2)
- Ampp Chapters (1)
- AMPP conference (1)
- AMPP logo (1)
- Ampp Membership (2)
- Ampp Standards (2)
- ampp training (2)
- Amusement parks (4)
- Architectural (1)
- Architectural Coatings (2)
- argonne national laboratory (1)
- Artificial Intelligence (1)
- Asset integrity (12)
- Asset maintenance (3)
- Asset Protection (1)
- awards (3)
- B2B Marketing (1)
- Bim Software (1)
- Biodeterioration of materials (5)
- Biofouling (4)
- Blasting (1)
- Bridges (4)
- career advancement (3)
- career development (2)
- cathodic protection (2)
- Cathodic Protection-CP (16)
- Ceramic epoxies (1)
- Certification (3)
- certification study guide (1)
- Chemical Injection (1)
- CIP (1)
- Civil Engineering (1)
- clean energy (1)
- Coating inspector (2)
- coating inspector job roles (1)
- Coating inspector jobs (2)
- Coating inspector program (2)
- Coatings (18)
- Coatings Application (3)
- coatings certification (1)
- Coatings failures (2)
- Coatings Industry (2)
- coatings inspection (1)
- Coatings inspector (2)
- Coatings measurement and inspection (9)
- coatings project management (1)
- Coatings Systems (1)
- Cold stress (1)
- Concrete (13)
- Concrete corrosion (1)
- concrete cracking (1)
- Conference and Events (2)
- Corrosion (26)
- Corrosion Basics (5)
- corrosion certification (1)
- Corrosion Control (17)
- Corrosion Control and Management (23)
- Corrosion detection (1)
- corrosion engineering (1)
- Corrosion Essentials (20)
- Corrosion Inspection (1)
- Corrosion Management (1)
- corrosion mitigation (1)
- corrosion of steel (1)
- corrosion policy (1)
- Corrosion Prevention (12)
- corrosion resistance (1)
- corrosion resources (1)
- Corrosion Under Insulation (2)
- cost of corrosion (1)
- Crevice Corrosion (1)
- Cui (2)
- Data Monitoring (1)
- decarbonization (1)
- defense infrastructure (1)
- Department of Defense (4)
- Deposition corrosion (1)
- Dissimilar Metal Corrosion (1)
- Dissolved gases (1)
- DoD (3)
- Education (2)
- EMERG (1)
- Energy industry (9)
- entertainment industry (1)
- Epoxy (3)
- exam preparation (1)
- FBE Application (1)
- FBE Inspection (1)
- Fireproofing (1)
- Flexible coatings (2)
- Flint, Michigan (1)
- Fluoropolymer coating (3)
- Forms of Corrosion (4)
- Freshwater salinization (1)
- Fusion-bonded epoxy (1)
- Galvanic (1)
- Galvanic Corrosion (4)
- General Corrosion (4)
- General Tips (1)
- glossary (1)
- Hand tools (1)
- honoree night (1)
- Industrial Application (3)
- Industrial Safety (3)
- Industry Best Practices (1)
- Industry Standards (2)
- Infrared Thermography (1)
- infrastructure (4)
- Infrastructure Durability (1)
- Inspection (1)
- integrity management (1)
- Intergranular Corrosion (1)
- Intumescent Coatings (1)
- key note speaker (1)
- leader (1)
- Machine Learning (2)
- Maintenance (2)
- Maintenance Best Practices (1)
- Maritime Coatings (11)
- Maritime industry (11)
- Master Painters Institute (2)
- material protection (1)
- materials performance (1)
- materials science (1)
- Membership (2)
- Membership Benefits (2)
- Michio Kaku (1)
- Microbiological forms (1)
- Microbiologically influenced corrosion-MIC (11)
- Military (2)
- Mineral constituents (1)
- MnDOT (1)
- MPI (3)
- mpi awards (1)
- mpi champion awards (1)
- mpi training (1)
- MPI Update (1)
- National Defense Authorization Act (1)
- national security (1)
- Navy (1)
- nickel-based alloys (1)
- Non-Destructive Testing (1)
- nuclear (1)
- nuclear Materials (1)
- nuclear reactor technology (1)
- Oil and Gas (2)
- Oil Fields (1)
- Organic matter (1)
- Oxgen (1)
- Paint and Protective coatings (32)
- Paint specification (1)
- pcs certification (1)
- Personal Protective Equipment (3)
- Petrochemical Plant Fireproofing Methods (1)
- Petrochemical Plants (1)
- Pipeline (2)
- Pitting Corrosion (2)
- Pitting Detection (1)
- Polymer-Based Coatings (1)
- Power plant (1)
- Power tools (1)
- PPE (3)
- Print Advertising (1)
- Print Marketing Strategy (1)
- professional certification (2)
- professional development (1)
- Protective Coatings (7)
- protective coatings industry (1)
- protective coatings specialist (1)
- quality assurance (1)
- radiation-resistant materials (1)
- Real-Time Corrosion Monitoring in Oil Fields (1)
- Rebar Corrosion (2)
- rectifier (1)
- Reliability (1)
- Remote monitoring and drones (4)
- Repaint (1)
- Restoration (1)
- ride maintenance (1)
- Risk-Based Inspection (1)
- Road deicers (1)
- Roads and bridges (1)
- Roller coaster (1)
- Rust (1)
- sacrificial anodes (1)
- Safety (5)
- Safety Standards (3)
- Salt pollution (1)
- Sensors (1)
- service awards (2)
- Ship Coatings (9)
- Shiptanks (1)
- Standards (10)
- Standards Committees (2)
- Steel (8)
- Steel Reinforcement (2)
- Stress Corrosion Cracking (1)
- Structural Steel (1)
- study tips (1)
- Surface Preparation (13)
- Sustainability (1)
- Sustainability and corrosion (7)
- terminology (1)
- Tools (1)
- Turbine (1)
- Types of Corrosion (1)
- Ultrasonic Testing (1)
- Uniform Corrosion (1)
- us army core of engineers (1)
- Wastewater Systems (1)
- Water crisis (1)
- Water pipe corrosion (1)
- Water quality (1)
- Water tank coatings (5)
- Water/treatment infrastructure (20)
- Waterway salinity (1)
- Workforce development (1)
- WRDA (1)