Zebra Mussels Are the Pits — Literally
May 23, 2022 •Corrosion CONTROLLED, Infrastructure, Water
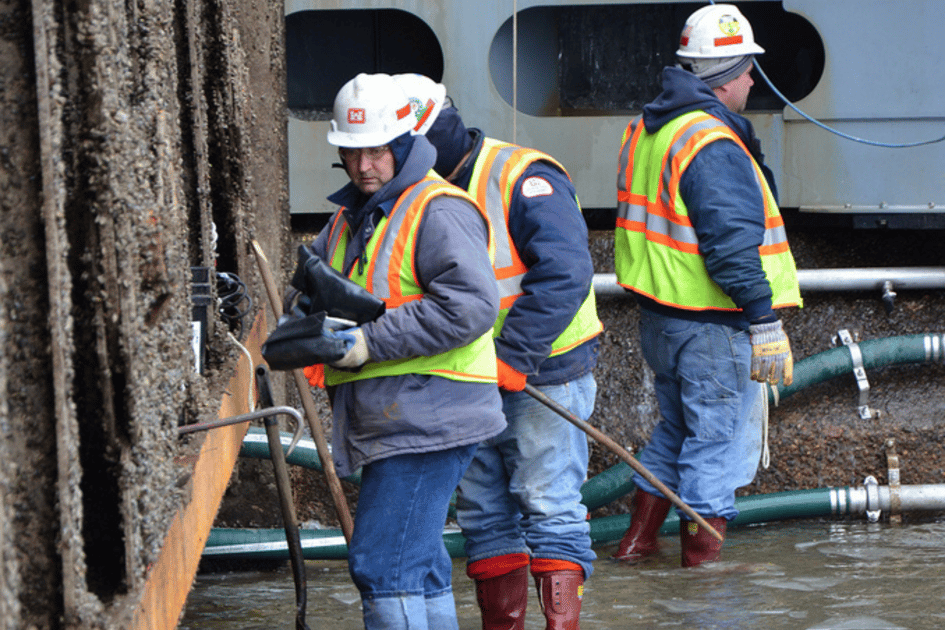
Zebra mussels, a small freshwater mollusk native to the Caspian and Black Seas, have been causing big problems in North American waters.
In addition to causing water quality issues and disrupting aquatic ecosystems, the prolific shellfish and their cousin, the quagga mussel, accumulate on underwater infrastructure and boats. This accumulation is called biofouling.
The freeloading mollusks cause corrosion via their acidic fecal matter, and the sticky protein threads they use to attach to surfaces have been shown to increase the corrosion rate of steel and iron, according to a 2001 study of shipwrecks in Lake Champlain.
According to a report by the U.S. Department of the Interior, these mussels “grow on a variety of infrastructure systems, including water intake pipes for drinking water, irrigation, and power plants. They also attach to locks, the faces and interiors of dams, and canal systems, greatly impacting operation and maintenance costs. With continual attachment, the mussels can increase corrosion rates of steel and concrete, leaving equipment and infrastructure vulnerable to failure.”
The Emsworth Locks and Dam, located on the Ohio River in Pittsburgh, Pennsylvania, is evidence of this. Operated by the US Army Corps of Engineers (USACE), the Emsworth project is one of six major river facilities on the Ohio River.
The presence of zebra mussels was throwing a wrench in the dam’s gate system, and to add insult to injury, the bulkhead structures were built using two different metals, aluminum and steel — a “perfect storm” scenario for developing corrosion problems.
To restore the bulkheads, USACE called in the experts from Coatings Unlimited, a St. Louis-based industrial coatings company.
“Typically, you don’t coat aluminum because it doesn’t need it, but [USACE] were having problems with zebra mussels attaching themselves to the bulkhead,” said Gene Ebbinghaus, project manager at contractor Coatings Unlimited Inc. “Secretions from the zebra mussels were causing pitting in the aluminum,” he continued. “They were concerned about losing the structural integrity of the bulkheads.”
The crew worked on one bulkhead at a time, starting with installing two types of containment. They used 85 percent containment underneath to avoid re-introducing the mussels and 100 percent (impenetrable) tarps when prepping.
That prep included pressure washing the aluminum with 5,000 psi to eliminate contaminants such as algae. The crew also blasted the surface to achieve a blast profile compliant with SSPC SP 16 Standard (Brush-off Blast Cleaning Non-Ferrous Metals).
To begin the coating process, the crew used a ceramic epoxy-based composite material to patch corrosive pits created by the bulkheads’ dissimilar metals. Then, the crew came back in to work on the three-coat spray-applied system — sanding, tackling defects, and verifying coating thickness measurements at each step. In total, the crew covered 40,000 square feet of aluminum.
While this approach addressed an existing biofouling problem, researchers are working to find new ways to prevent biofouling before it begins. Although many of these solutions address marine biofouling in the shipping industry, they may also have freshwater applications to fight the zebra mussel invasion in North America’s lakes and rivers.
- In 2018, APV Engineered Coatings announced an experimental marine coating that would prevent damage caused by barnacle and zebra mussel fouling while reducing maintenance costs and environmental effects. This new antifouling coating is based on the Marine Organism Sensory Interference (MOSI) concept, which “tricks” juvenile barnacles into creating a type of adhesive that does not allow itself to attach to ship hulls and other marine assets.
- Protective coatings applied to vessels usually contain copper-based biocides, which may harm the environment and become ineffective due to resistance developed by organisms. A German research team simulated a defense mechanism employed by algae, and discovered that cerium dioxide (CeO2) nanoparticles can effectively prevent fouling. This discovery could lead to the production of new protective coatings that are much less environmentally harmful than current antifouling coatings.
- Dutch paint and performance coatings company, AkzoNobel, is working to develop a biocide-free fouling prevention technology using ultraviolet light-emitting diodes (UV-LED) for the hulls of ships and boats.
Sources and Additional Reading
AMPP Interview Series. “AMPP Technical Exchange on Ship Biofouling.” 2021.
Chizik, Stephanie M. "Coatings Crew Mussels Through Corroded Bulkheads." CoatingsPro Magazine, January 2019.
Koch, Sophie. “Invasive Zebra Mussels.” U.S. National Park Service.(2017)
US Army Corps of Engineers. Emsworth Locks & Dams.
US Army Corps of Engineers. Zebra Mussel Resource Document (2013)
US Department of the Interior, Invasive Species Advisory Committee. Invasive Species Impacts on Infrastructure (2016)
Watson, Mary, Arthur B. Cohn, and Bryan P. Emerson. Zebra Mussels, Shipwrecks, and the Environment. (2001)
Featured Image
USACE operations employees scrape zebra mussels off the lock wall. The U.S. Army Corps of Engineers St. Paul District dewatered Lock and Dam 7, located near La Crescent, Minn., to do major renovation and rehabilitation work. (U.S. Army Corps of Engineers photo by Shannon Bauer)
Get Updates
Featured Articles
Categories
- 2024 Olympics (1)
- 2024 Water Resource Development Act (1)
- Abrasive Blasting (1)
- Advanced coating materials (9)
- advanced coatings (1)
- Advanced Corrosion Control in Oil and Gas Industry (2)
- Advocacy (3)
- AI (2)
- Aircraft (1)
- Alkanization (1)
- AMPP (4)
- AMPP Annual Conference + Expo (5)
- ampp awards (1)
- ampp certification (2)
- Ampp Chapters (1)
- AMPP conference (1)
- AMPP logo (1)
- Ampp Membership (2)
- Ampp Standards (2)
- ampp training (2)
- Amusement parks (4)
- Architectural (1)
- Architectural Coatings (2)
- argonne national laboratory (1)
- Artificial Intelligence (1)
- Asset integrity (12)
- Asset maintenance (3)
- Asset Protection (1)
- awards (3)
- Bim Software (1)
- Biodeterioration of materials (5)
- Biofouling (4)
- Blasting (1)
- Bridges (4)
- career advancement (3)
- career development (2)
- cathodic protection (2)
- Cathodic Protection-CP (16)
- Ceramic epoxies (1)
- Certification (3)
- certification study guide (1)
- Chemical Injection (1)
- CIP (1)
- Civil Engineering (1)
- clean energy (1)
- Coating inspector (2)
- coating inspector job roles (1)
- Coating inspector jobs (2)
- Coating inspector program (2)
- Coatings (18)
- Coatings Application (3)
- coatings certification (1)
- Coatings failures (2)
- Coatings Industry (2)
- coatings inspection (1)
- Coatings inspector (2)
- Coatings measurement and inspection (9)
- coatings project management (1)
- Coatings Systems (1)
- Cold stress (1)
- Concrete (13)
- Concrete corrosion (1)
- concrete cracking (1)
- Conference and Events (2)
- Corrosion (26)
- Corrosion Basics (5)
- corrosion certification (1)
- Corrosion Control (17)
- Corrosion Control and Management (23)
- Corrosion detection (1)
- corrosion engineering (1)
- Corrosion Essentials (20)
- Corrosion Inspection (1)
- Corrosion Management (1)
- corrosion mitigation (1)
- corrosion of steel (1)
- corrosion policy (1)
- Corrosion Prevention (12)
- corrosion resistance (1)
- corrosion resources (1)
- Corrosion Under Insulation (2)
- cost of corrosion (1)
- Crevice Corrosion (1)
- Cui (2)
- Data Monitoring (1)
- decarbonization (1)
- defense infrastructure (1)
- Department of Defense (4)
- Deposition corrosion (1)
- Dissimilar Metal Corrosion (1)
- Dissolved gases (1)
- DoD (3)
- Education (2)
- EMERG (1)
- Energy industry (9)
- entertainment industry (1)
- Epoxy (3)
- exam preparation (1)
- FBE Application (1)
- FBE Inspection (1)
- Fireproofing (1)
- Flexible coatings (2)
- Flint, Michigan (1)
- Fluoropolymer coating (3)
- Forms of Corrosion (4)
- Freshwater salinization (1)
- Fusion-bonded epoxy (1)
- Galvanic (1)
- Galvanic Corrosion (4)
- General Corrosion (4)
- General Tips (1)
- glossary (1)
- Hand tools (1)
- honoree night (1)
- Industrial Application (3)
- Industrial Safety (3)
- Industry Best Practices (1)
- Industry Standards (2)
- Infrared Thermography (1)
- infrastructure (4)
- Infrastructure Durability (1)
- Inspection (1)
- integrity management (1)
- Intergranular Corrosion (1)
- Intumescent Coatings (1)
- key note speaker (1)
- leader (1)
- Machine Learning (2)
- Maintenance (2)
- Maintenance Best Practices (1)
- Maritime Coatings (11)
- Maritime industry (11)
- Master Painters Institute (2)
- material protection (1)
- materials performance (1)
- materials science (1)
- Membership (2)
- Membership Benefits (2)
- Michio Kaku (1)
- Microbiological forms (1)
- Microbiologically influenced corrosion-MIC (11)
- Military (2)
- Mineral constituents (1)
- MnDOT (1)
- MPI (3)
- mpi awards (1)
- mpi champion awards (1)
- mpi training (1)
- MPI Update (1)
- National Defense Authorization Act (1)
- national security (1)
- Navy (1)
- nickel-based alloys (1)
- Non-Destructive Testing (1)
- nuclear (1)
- nuclear Materials (1)
- nuclear reactor technology (1)
- Oil and Gas (2)
- Oil Fields (1)
- Organic matter (1)
- Oxgen (1)
- Paint and Protective coatings (32)
- Paint specification (1)
- pcs certification (1)
- Personal Protective Equipment (3)
- Petrochemical Plant Fireproofing Methods (1)
- Petrochemical Plants (1)
- Pipeline (2)
- Pitting Corrosion (2)
- Pitting Detection (1)
- Polymer-Based Coatings (1)
- Power plant (1)
- Power tools (1)
- PPE (3)
- professional certification (2)
- professional development (1)
- Protective Coatings (7)
- protective coatings industry (1)
- protective coatings specialist (1)
- quality assurance (1)
- radiation-resistant materials (1)
- Real-Time Corrosion Monitoring in Oil Fields (1)
- Rebar Corrosion (2)
- rectifier (1)
- Reliability (1)
- Remote monitoring and drones (4)
- Repaint (1)
- Restoration (1)
- ride maintenance (1)
- Risk-Based Inspection (1)
- Road deicers (1)
- Roads and bridges (1)
- Roller coaster (1)
- Rust (1)
- sacrificial anodes (1)
- Safety (5)
- Safety Standards (3)
- Salt pollution (1)
- Sensors (1)
- service awards (2)
- Ship Coatings (9)
- Shiptanks (1)
- Standards (10)
- Standards Committees (2)
- Steel (8)
- Steel Reinforcement (2)
- Stress Corrosion Cracking (1)
- Structural Steel (1)
- study tips (1)
- Surface Preparation (13)
- Sustainability (1)
- Sustainability and corrosion (7)
- terminology (1)
- Tools (1)
- Turbine (1)
- Types of Corrosion (1)
- Ultrasonic Testing (1)
- Uniform Corrosion (1)
- us army core of engineers (1)
- Wastewater Systems (1)
- Water crisis (1)
- Water pipe corrosion (1)
- Water quality (1)
- Water tank coatings (5)
- Water/treatment infrastructure (20)
- Waterway salinity (1)
- Workforce development (1)
- WRDA (1)